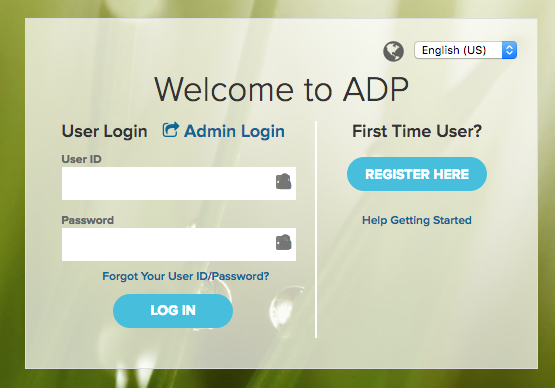
Human resources specialists have many responsibilities. It is important that you are able to communicate with all types of people. You will need to interact with both senior executives and employees at all levels. This job requires you to be meticulous and able to manage large quantities of information daily. This is because you will be making important decisions daily, and you'll be expected to evaluate different options.
Responsibilities of a human resources specialist
The management of an organisation often requires support from human resources specialists. These specialists also help resolve issues related to employee relations, FMLA cases, and workers' compensation. The human resources specialist is responsible for applicant tracking and new hire paperwork. They also ensure that all documentation is current and accurate. This job requires high communication skills. Other duties for a human resources specialist include maintaining employee records or databases, preparing and giving reports, and helping with the preparation of a company’s financial plan.
Human resource specialists must be proficient in labor laws. They also must be familiar with all company policies, and ensure that they are enforced. They also respond to concerns of employees and provide advice on how to retain and attract the best employees. They must also prepare orientation materials to new recruits and maintain records of all HR paperwork.
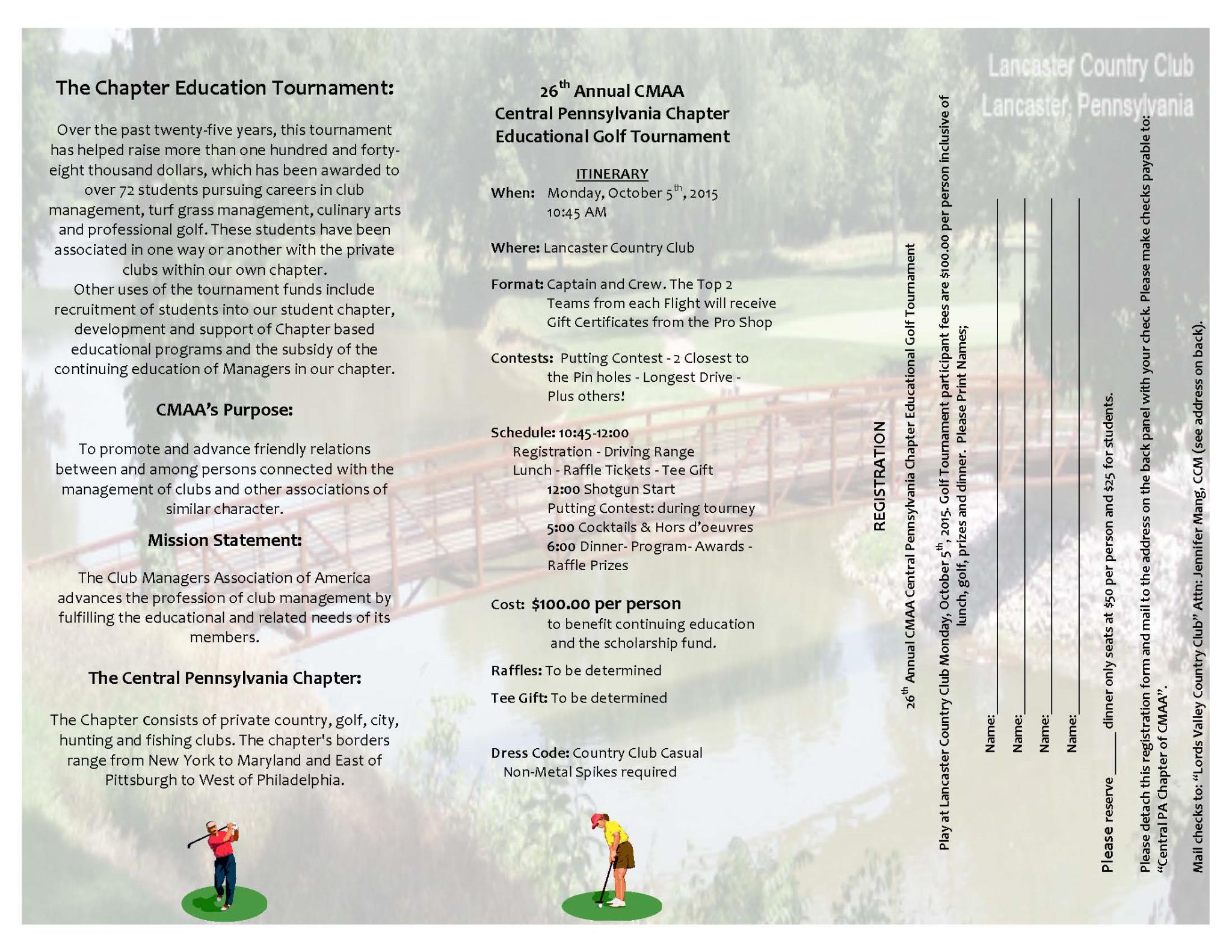
To become a human resource specialist
For those interested in becoming a human resources specialist, there are a number of education requirements. An undergraduate degree is sufficient to give you basic knowledge, but an MBA program focusing on human resources will equip you with more in-depth skills and knowledge. Employers prefer MBA graduates because they have strong business and critical thinking skills. Moreover, an MBA degree gives you the opportunity to pursue a career in any industry and will help you gain more experience and knowledge in the field.
Apart from the education requirements, you need strong interpersonal and communications skills to be a human resources specialist. To provide the best services, you must be able listen to employees and job applicants. You must also be able to effectively deal with conflicts and disputes.
For a human resource specialist, career options
For a human resource specialist, there are many career options. These include payroll, engagement and recruiting, leave of absenteeism, diversity, inclusion, recruitment and benefits. The right one for you will depend on your interests. Understanding the opportunities available in this field will allow you to choose the right path for your future.
A career in human resources can include working in various departments within an organization. Many HR specialists are generalists. They have broad responsibilities that are vital for a company's operations. Larger companies hire HR specialists who are experts in a specific area such as labor relations.
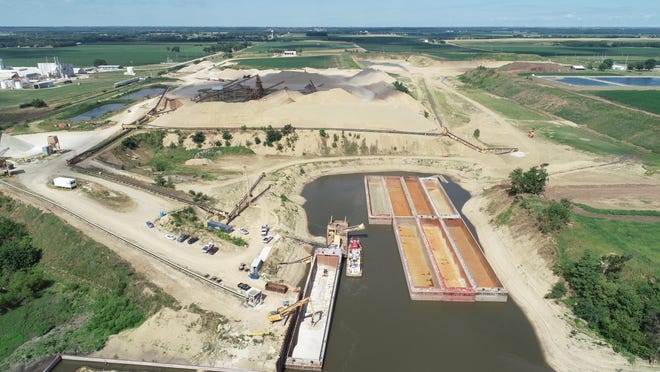
A Human Resources Specialist acts as an intermediary between employees, management and the general public. They will deal with grievances and negotiate contracts.
FAQ
What is the difference between TQM and Six Sigma?
The main difference in these two quality management tools lies in the fact that six sigma is focused on eliminating defects and total quality management (TQM), emphasizes improving processes and reducing costs.
Six Sigma is an approach for continuous improvement. It emphasizes the elimination and improvement of defects using statistical methods, such as control charts, P-charts and Pareto analysis.
This method attempts to reduce variations in product output. This is accomplished by identifying the root cause of problems and fixing them.
Total quality management includes monitoring and measuring all aspects of an organization's performance. It also involves training employees to improve performance.
It is often used to increase productivity.
What is TQM exactly?
The industrial revolution saw the realization that prices alone were not sufficient to sustain manufacturing companies. This led to the birth of quality. To remain competitive, they had to improve quality as well as efficiency.
Management responded to the need to improve, and developed Total Quality Management (TQM). This focused on improving every aspect of an organization’s performance. It included continuous improvement and employee involvement as well as customer satisfaction.
How do we create a company culture that is productive?
A positive company culture creates a sense of belonging and respect in its people.
It is based on three principles:
-
Everyone has something to contribute
-
People are treated with respect
-
There is mutual respect between individuals and groups
These values are evident in the way that people act. They will show consideration and courtesy to others.
They will listen to other people's opinions respectfully.
These people will inspire others to share thoughts and feelings.
A company culture encourages collaboration and communication.
People feel safe to voice their opinions without fear of reprisal.
They know mistakes will be accepted as long as they are dealt with honestly.
Finally, the company culture promotes integrity and honesty.
Everyone knows that they must always tell truth.
Everyone understands there are rules that they must follow.
And no one expects special treatment or favors.
What does it mean to say "project management"
That is the management of all activities associated with a project.
These include planning the scope and identifying the needs, creating the budget, organizing the team, scheduling the work and monitoring progress. Finally, we close down the project.
Statistics
- UpCounsel accepts only the top 5 percent of lawyers on its site. (upcounsel.com)
- The average salary for financial advisors in 2021 is around $60,000 per year, with the top 10% of the profession making more than $111,000 per year. (wgu.edu)
- Your choice in Step 5 may very likely be the same or similar to the alternative you placed at the top of your list at the end of Step 4. (umassd.edu)
- 100% of the courses are offered online, and no campus visits are required — a big time-saver for you. (online.uc.edu)
- This field is expected to grow about 7% by 2028, a bit faster than the national average for job growth. (wgu.edu)
External Links
How To
How does Lean Manufacturing work?
Lean Manufacturing is a method to reduce waste and increase efficiency using structured methods. They were created in Japan by Toyota Motor Corporation during the 1980s. The main goal was to produce products at lower costs while maintaining quality. Lean manufacturing is about eliminating redundant steps and activities from the manufacturing process. It consists of five basic elements: pull systems, continuous improvement, just-in-time, kaizen (continuous change), and 5S. The production of only what the customer needs without extra work is called pull systems. Continuous improvement involves constantly improving upon existing processes. Just-in-time refers to when components and materials are delivered directly to the point where they are needed. Kaizen means continuous improvement, which is achieved by implementing small changes continuously. Five-S stands for sort. It is also the acronym for shine, standardize (standardize), and sustain. To achieve the best results, these five elements must be used together.
Lean Production System
Six key concepts form the foundation of the lean production system:
-
Flow: The goal is to move material and information as close as possible from customers.
-
Value stream mapping is the ability to divide a process into smaller tasks, and then create a flowchart that shows the entire process.
-
Five S's, Sort, Set in Order, Shine. Standardize. and Sustain.
-
Kanban - use visual signals such as colored tape, stickers, or other visual cues to keep track of inventory;
-
Theory of constraints - identify bottlenecks in the process and eliminate them using lean tools like kanban boards;
-
Just-in-time delivery - Deliver components and materials right to your point of use.
-
Continuous improvement: Make incremental improvements to the process instead of overhauling it completely.