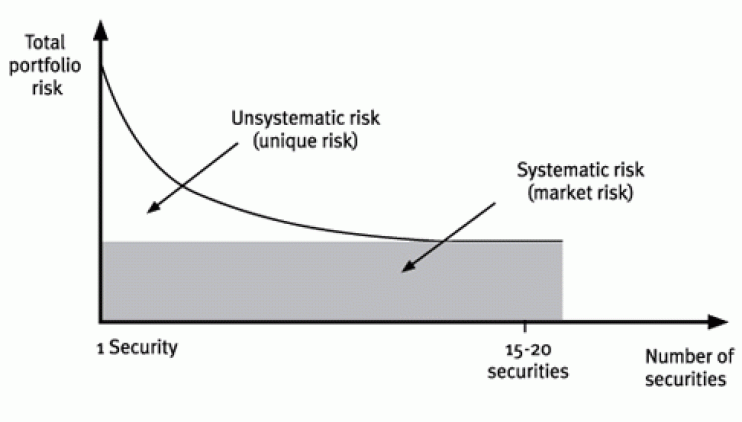
Accenture is the world's largest supply chain consultancy and has acquired GRA, a logistics and supply chains consulting firm. By combining these services, Accenture helps its clients meet the increasing demands of the modern supply chain. Accenture's supply chains experts work with clients to deliver positive customer experiences. Accenture has recently acquired Blue Horseshoe Group, and Xoomworks Group. We will be discussing the importance and role of supply-chain capabilities in modern business strategy.
Accenture's Supply Chain Strategy
Recently, Accenture completed a global supply chain strategy for MedShare International, a 501(c)(3) charitable organization based in Atlanta that distributes surplus medical supplies in developing nations. The strategy was designed to optimize the entire supply chains, from procurement and sourcing to warehouse operations and customer interaction. It will be implemented over several consecutive years with the aim of increasing the organization's profitability. MedShare was able to accomplish its mission of solving the global health crisis through helping the most vulnerable.
Companies must redesign their entire supply network to be more customer-centric in order meet consumer needs. Customer-centricity allows them to create hyper-personalized products and experiences by leveraging it. These networks are vital for both a company's bottom line as well as the global economy. Accenture's supply chain strategy can help organizations accelerate their journey to customer-centricity. It identifies targeted commercial interventions, cash flow, and other ways to increase revenue.
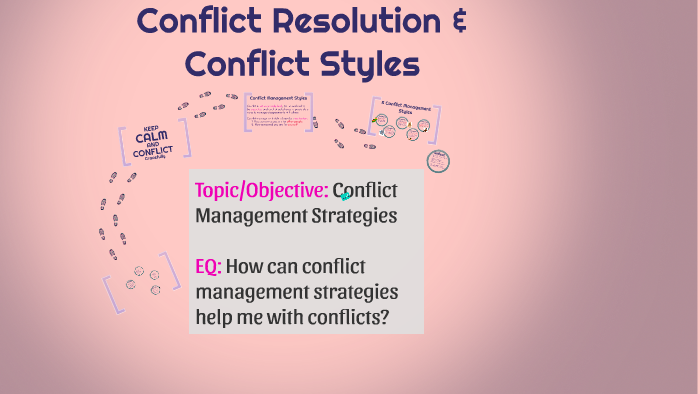
Accenture's acquisition of Alfa Consulting
Accenture recently acquired a company that specializes on operations strategy for capital-intensive sectors. Alfa is based in Spain and has offices in Spain, Portugal, Mexico, and Spain. Alfa is an expert in supply chain management, as well as analytical models, for a wide range of industries including tech, capital goods, energy, and tech. Accenture's growing global business will add Alfa to its supply chain management team. Clients can expect greater efficiency and sustainability for their supply chain operations.
Accenture will integrate Alfa Consulting into its Supply Chain & Operations group. It helps clients create customer-centric supply chains and sourcing transformations. Accenture will continue offering its own value-based maintenance plans and workforce planning services in addition Alfa's supply chain consulting. Accenture's Iberia supply chain capabilities will be enhanced by the acquisition. Accenture still has a strong presence throughout the U.S.
Accenture acquires Xoomworks Group
Accenture announced the acquisition by Xoomworks, a technology- and innovation consulting firm. Accenture's Closed Loop Spend Administration capabilities are strengthened by the acquisition of Xoomworks, a technology and innovation consultancy. Clients have unparalleled visibility into all price categories and insights through this system. It also strengthens its ecosystem partners, who have deep expertise in digital change management and innovation. Accenture has added a new talent pool with this acquisition. It employs more than 62,000 people around the globe, making it one of the most important consulting firms in the country.
The Xoomworks Group was established in 2000 and currently operates two businesses: Xoomworks Procurement, and Xoomworks Technology. The company's procurement division offers digital procurement solutions and sourcing options for clients from across the industry. Xoomworks Procurement is home to more than 250 employees in the UK and France. Accenture says the acquisition will strengthen its Closed Loop Spend Management capabilities, which enable clients to achieve significant, sustainable cost savings.
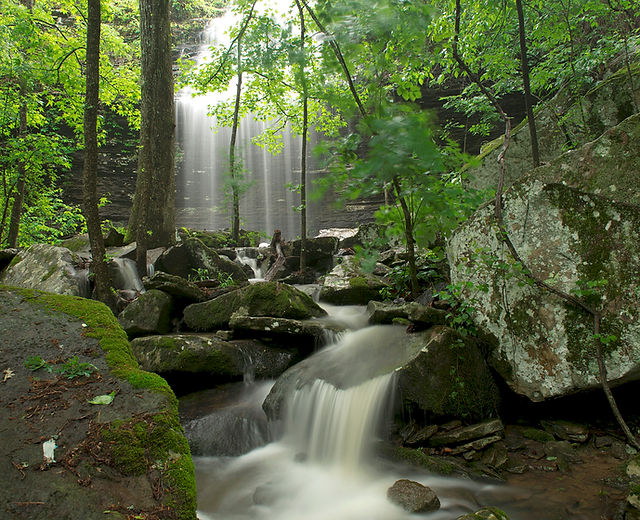
Accenture acquires Blue Horseshoe
Accenture recently announced its acquisition of Blue Horseshoe. Blue Horseshoe is a supply chain strategy integration company. Founded in 2001, Blue Horseshoe helps clients in a variety of industries define their enterprise strategies, connect applications, and optimize their supply chain operations. The new company will have offices in North Carolina, Ohio and Estonia. It will provide a wide range of supply-chain solutions. Continue reading to learn more about this acquisition.
Accenture is continuing a string recent acquisitions. Accenture, which is a consulting firm, has been increasingly active within the M&A market. It acquires numerous companies each year. Accenture had previously purchased data analytics companies as well as ad agencies. Recently, however, the company bought LEXTA, a strategic IT consultant. It is the third largest transaction in the company’s history.
FAQ
What is the difference between leadership and management?
Leadership is about influence. Management is about controlling others.
A leader inspires followers while a manager directs workers.
A leader motivates people and keeps them on task.
A leader develops people; a manager manages people.
How to manage employees effectively?
Managing employees effectively means ensuring that they are happy and productive.
It means setting clear expectations for them and keeping an eye on their performance.
To do this successfully, managers need to set clear goals for themselves and for their teams.
They need to communicate clearly and openly with staff members. They should also ensure that they both reward high performers and discipline those who are not performing to their standards.
They must also keep track of the activities of their team. These include:
-
What was the result?
-
How much work were you able to accomplish?
-
Who did it all?
-
What was the moment it was completed?
-
Why it was done?
This information can be used for monitoring performance and evaluating results.
What are some common mistakes managers make when managing people?
Managers can make their jobs more difficult than necessary.
They may not delegate enough responsibilities to staff and fail to give them adequate support.
A majority of managers lack the communication skills needed to motivate their team and lead them.
Managers can set unrealistic expectations for their employees.
Managers might try to solve every problem by themselves rather than delegating the responsibility.
How does Six Sigma function?
Six Sigma employs statistical analysis to identify problems, measure them and analyze root causes. Six Sigma also uses experience to correct problems.
The first step is identifying the problem.
The data is then analyzed and collected to identify trends.
Next, corrective steps are taken to fix the problem.
Final analysis of data is done to determine if the problem has been solved.
This cycle continues until there is a solution.
What do we mean when we say "project management"?
That is the management of all activities associated with a project.
These include planning the scope and identifying the needs, creating the budget, organizing the team, scheduling the work and monitoring progress. Finally, we close down the project.
Why is it important for companies to use project management techniques?
Project management techniques can be used to ensure smooth project execution and meeting deadlines.
This is because most businesses rely on project work for their products and services.
Companies must manage these projects effectively and efficiently.
Companies may lose their reputation, time and money if they do not have effective project management.
Statistics
- As of 2020, personal bankers or tellers make an average of $32,620 per year, according to the BLS. (wgu.edu)
- 100% of the courses are offered online, and no campus visits are required — a big time-saver for you. (online.uc.edu)
- Our program is 100% engineered for your success. (online.uc.edu)
- The profession is expected to grow 7% by 2028, a bit faster than the national average. (wgu.edu)
- The average salary for financial advisors in 2021 is around $60,000 per year, with the top 10% of the profession making more than $111,000 per year. (wgu.edu)
External Links
How To
How do I do the Kaizen Method?
Kaizen means continuous improvement. This term was first used by Toyota Motor Corporation in the 1950s. It refers to the Japanese philosophy that emphasizes continuous improvement through small incremental changes. It's a process where people work together to improve their processes continuously.
Kaizen, a Lean Manufacturing method, is one of its most powerful. This concept requires employees to identify and solve problems during manufacturing before they become major issues. This increases the quality of products and reduces the cost.
Kaizen is the idea that every worker should be aware of what is going on around them. To prevent problems from happening, any problem should be addressed immediately. It is important that employees report any problems they see while on the job to their managers.
Kaizen follows a set of principles. Start with the end product, and then move to the beginning. To improve our factory, for example, we need to fix the machines that produce the final product. Then, we fix the machines that produce components and then the ones that produce raw materials. We then fix the workers that work with those machines.
This method, called 'kaizen', focuses on improving each and every step of the process. When we are done fixing the whole factory, we go back to the beginning and continue until we reach perfection.
Before you can implement kaizen into your business, it is necessary to learn how to measure its effectiveness. There are many ways you can determine if kaizen has been implemented well. One way is to examine the amount of defects on the final products. Another way is to see how much productivity has increased since implementing kaizen.
If you want to find out if your kaizen is actually working, ask yourself why. You were trying to save money or obey the law? Did you really believe it would lead to success?
Suppose you answered yes to any of these questions, congratulations! You're now ready to get started with kaizen.