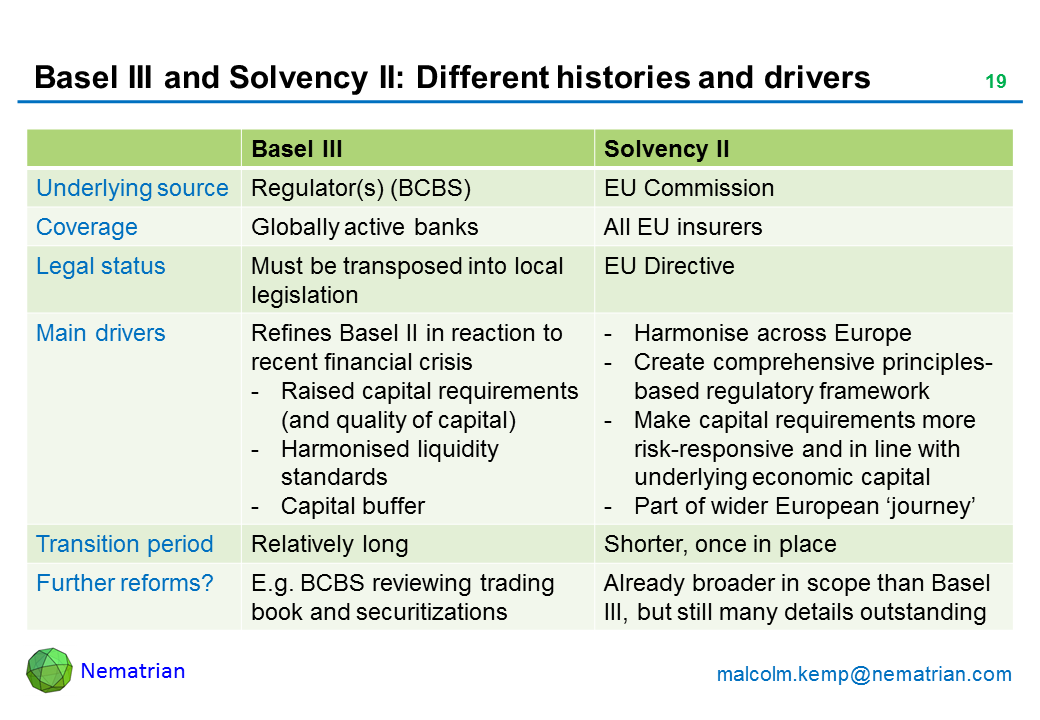
There are many journals that publish regular articles on supply-chain management. The journal and the type of article will determine the number of articles that are published. The majority of articles focus on SMEs and high-demand items. Some articles focus on the agency theory and its effect on supply chain management. The following section will give an overview of articles published by various journals.
Trends in articles about supply chain management
Supply chains are the lifeblood of most businesses. They must be able to fulfill customer expectations, regardless of whether they're online or offline. From COVID-19 pandemic to a labor shortage, a supply chain disruption can disrupt a business's entire operation. Supply chain trends and statistics are useful tools to help businesses plan for potential changes.
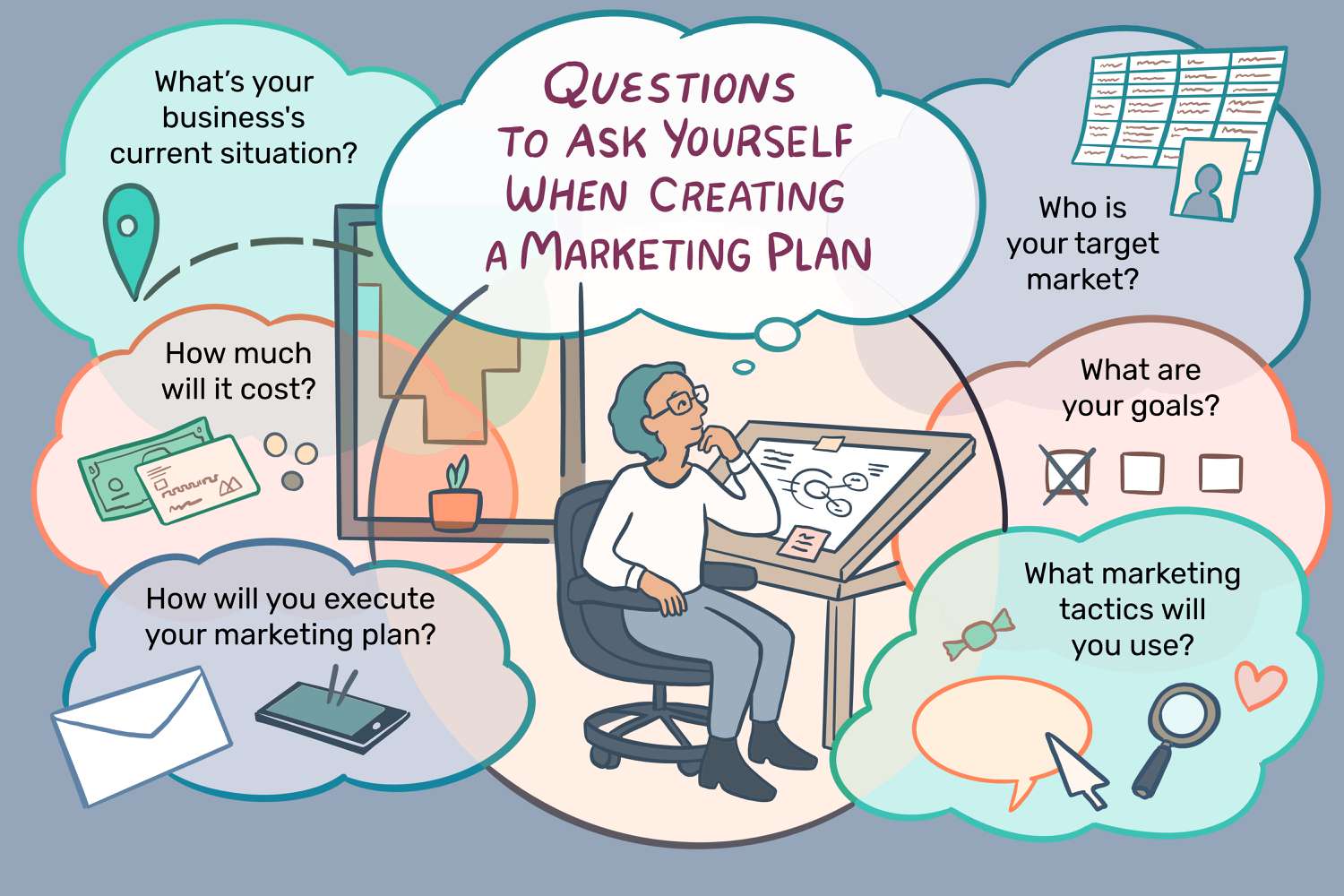
As a result, supply chains are changing due to many factors such as customer expectations and technological developments. Companies must be capable of managing multiple customer channels and fulfilment models as well as payment options and physical systems. To optimize their supply chain, some companies are turning to artificial Intelligence (AI). This technology can not only help save money, it can also speed things up.
Articles on supply chain management are published by affiliated researchers
The Association of Affiliated Researchers in Articles on Supply Chain Management (AAF), publishes a ranking of supply-chain management research output. It is based on the number of publications in each of the last five years. Submissions are evaluated on their relevance to supply chain management research topics, methodological rigor, and significant advancement of knowledge.
AAF publishes many reports on a wide range topics. These research findings give insight into trends and developments in the supply chains and procurement industry. Topics covered include supply chain planning, forecasting, big data, inventory management, and sales and operations planning.
Majority of articles focus on SMEs
Although most articles about supply chain management are focused on large corporations with global operations, there are some articles that focus on the role and responsibilities of SMEs. Zowada (2011) argues that linkage is a key factor in gaining competitive advantage. This is because SMEs must be flexible and adaptable.
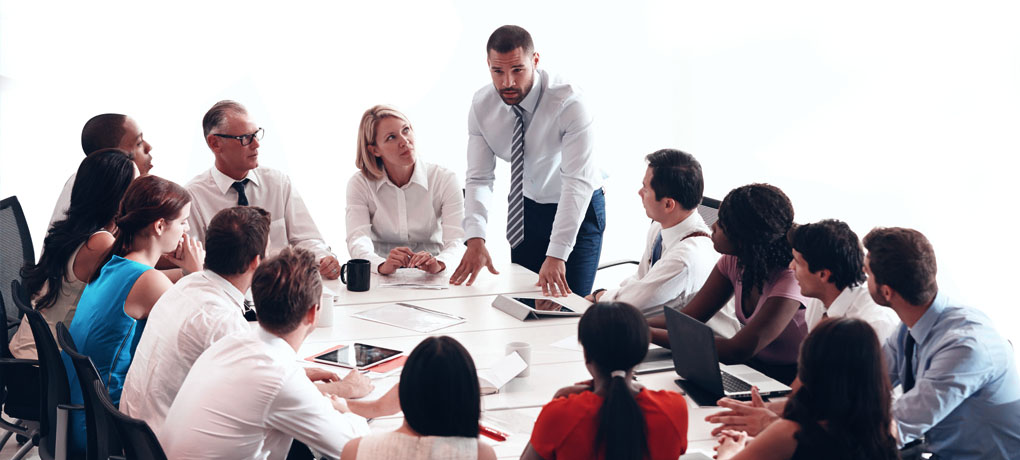
SME's are an integral part of many economies and societies. They make significant contributions to GDP, exports and employment as well as their livelihoods. But they are facing growing threats that could hinder their growth. Fortunately, governments can learn from their past success and develop new programs to support SMEs to thrive in the modern world.
FAQ
Why is it so hard to make smart business decisions?
Complex systems and many moving parts make up businesses. People who manage them have to balance multiple priorities while dealing with complexity and uncertainty.
Understanding the impact of these factors on the system is crucial to making sound decisions.
You need to be clear about the roles and responsibilities of each system. You then need to consider how those individual pieces interact with each other.
You should also ask yourself if there are any hidden assumptions behind how you've been doing things. If not, you might want to revisit them.
Try asking for help from another person if you're still stuck. They might have different perspectives than you, and could offer insight that could help you solve your problem.
How does a manager motivate his/her employees?
Motivation refers to the desire to perform well.
It is possible to be motivated by doing something you enjoy.
You can also feel motivated by making a positive contribution to the success in the organization.
For example: If you want to be a doctor, you might find it more motivating seeing patients than reading medical books all day.
Another type of motivation comes from within.
You may feel strongly that you are responsible to help others.
You may even find it enjoyable to work hard.
If you don’t feel motivated, find out why.
Then think about how you can make your life more motivating.
What are the five management steps?
Planning, execution, monitoring and review are the five stages of any business.
Setting goals for the future requires planning. Planning involves defining your goals and how to get there.
Execution takes place when you actually implement the plans. You need to make sure they're followed by everyone involved.
Monitoring is the act of monitoring your progress towards achieving your targets. This should involve regular reviews of performance against targets and budgets.
Reviews take place at the end of each year. They allow for an assessment of whether all went well throughout the year. If not there are changes that can be made to improve the performance next year.
After the annual review is complete, evaluations are conducted. It helps identify which aspects worked well and which didn't. It provides feedback about how people perform.
What's the difference between leadership & management?
Leadership is about influencing others. Management is all about controlling others.
A leader inspires his followers while a manager directs the workers.
A leader motivates people and keeps them on task.
A leader develops people; a manager manages people.
What is Six Sigma?
Six Sigma employs statistical analysis to identify problems, measure them and analyze root causes. Six Sigma also uses experience to correct problems.
The first step in solving a problem is to identify it.
Next, data is collected and analyzed to identify trends and patterns.
Then corrective actions are taken to solve the problem.
The data are then reanalyzed to see if the problem is solved.
This cycle continues until there is a solution.
How can a manager improve his/her managerial skills?
It is important to have good management skills.
Managers must constantly monitor the performance of their subordinates.
If you notice your subordinate isn't performing up to par, you must take action quickly.
You should be able to identify what needs improvement and how to improve things.
Statistics
- As of 2020, personal bankers or tellers make an average of $32,620 per year, according to the BLS. (wgu.edu)
- UpCounsel accepts only the top 5 percent of lawyers on its site. (upcounsel.com)
- Our program is 100% engineered for your success. (online.uc.edu)
- Hire the top business lawyers and save up to 60% on legal fees (upcounsel.com)
- Your choice in Step 5 may very likely be the same or similar to the alternative you placed at the top of your list at the end of Step 4. (umassd.edu)
External Links
How To
How can you use the Kaizen method?
Kaizen means continuous improvement. The term was coined in the 1950s at Toyota Motor Corporation and refers to the Japanese philosophy emphasizing constant improvement through small incremental changes. It's a team effort to continuously improve processes.
Kaizen is one of the most effective methods used in Lean Manufacturing. In this concept, employees who are responsible for the production line must identify problems that exist during the manufacturing process and try to solve them before they become big issues. This is how you can improve the quality and lower the cost.
The main idea behind kaizen is to make every worker aware of what happens around him/her. It is important to correct any problems immediately if they are discovered. So, if someone notices a problem while working, he/she should report it to his/her manager.
There are some basic principles that we follow when doing kaizen. Always start with the end product in mind and work our way back to the beginning. In order to improve our factory's production, we must first fix the machines producing the final product. Next, we fix the machines which produce components. And finally, we fix the workers who work directly with those machines.
This method is known as kaizen because it focuses upon improving every aspect of the process step by step. When we are done fixing the whole factory, we go back to the beginning and continue until we reach perfection.
How to measure kaizen's effectiveness in your business is essential to implement it. There are many ways you can determine if kaizen has been implemented well. Another method is to see how many defects are found on the products. Another way to find out how productive your company has been since you implemented kaizen is to measure the increase in productivity.
A good way to determine whether kaizen has been implemented is to ask why. It was because of the law, or simply because you wanted to save some money. Did you really believe that it would be a success factor?
Congratulations if you answered "yes" to any of the questions. You're ready to start kaizen.