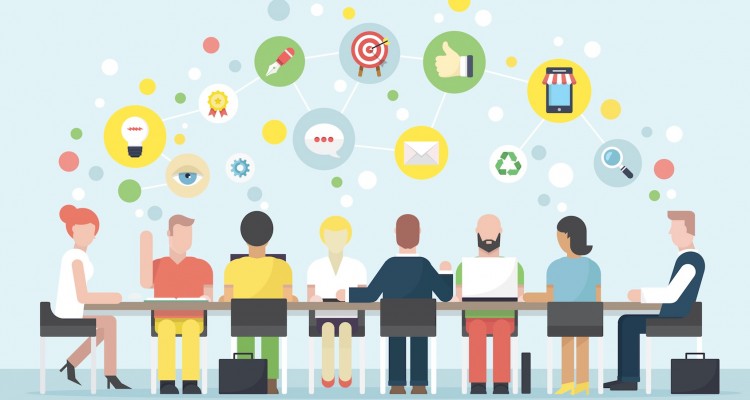
There are many things you need to keep in mind when dealing with construction debris. These include the types of waste, such as hazardous, recyclable, and off-site. There are also many regulations concerning the disposal and recycling of construction waste. This article will focus on hazardous waste, recycling, the importance to seperate hazardous waste from the remainder. When you are familiar with these areas, you will be able to make an informed decision about how to responsibly handle these materials.
Hazardous
Special equipment and experience are required to properly dispose of hazardous construction waste. These wastes can cause harm to the environment and people if they are not properly managed. Incorrect disposal can result in penalties from the government. Junk King, as well as other waste removal companies, are capable of handling hazardous construction waste. Here are some examples of common construction wastes. These are just a few examples. Construction is fraught with hazardous waste. Here are some suggestions for how to manage construction waste.
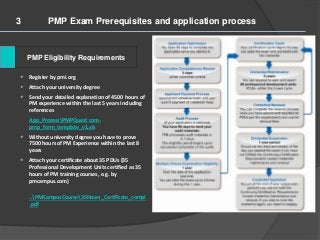
Most construction and demolition waste are transported by truck to diversion sites. The most popular trucks in the United States are medium and light duty trucks. They have modular interoperability, and can be mated together. Facility management plans specify what materials are acceptable for disposal, and refuse haulers may reject a load containing hazardous materials. The four characteristics that make up hazardous waste are corrosivity and ignitability as well as reactivity and toxicity. The Environment Agency and California Department of Environmental Quality are responsible for hazardous waste management.
Recyclable
It's important that you take action to reduce the amount construction waste that ends up in the landfills. California Green Building Standards Code requires that builders prepare a plan for managing construction waste before they can be approved and permitted. There are many materials that you can recycle: wood, vegetation, metals, insulation and ceiling tiles. Some composites such Hardplan siding may also be recyclable.
Recycling construction waste offers many benefits. Recycling construction waste helps conserve energy and reduces the need for natural resources. Recycling all asphalt and concrete waste produced by US construction projects will result in a savings of approximately one billion gallons per year. Additionally, recycling your waste can help protect the environment and reduce the amount of toxic waste that is dumped in landfills.
Off-site
Hong Kong Civil Engineering and Development Department have two off-site CWS facilities. In February 2012, they handled 5.11 million tonnes of construction waste. It is necessary to improve the program in order to get better results. This paper examines Hong Kong's CWS programs and offers practical suggestions for improving them. This will enable construction professionals to reduce their waste production and reduce hauling costs. Contractors should instruct suppliers to use less packaging in order to have a more efficient waste management system.
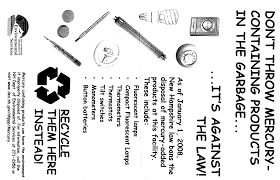
Another advantage of construction waste off-site is the ability to identify the material easily and quickly. CWS on-site must be properly identified to ensure their economic viability. Many contracting firms, subcontractors and project specifications include jobsite waste management protocols. The guidelines and policies that govern construction waste management may be established by building owners. Many service providers can even provide containers for materials. It is important to understand the legal requirements and costs associated with construction waste disposal and recycling.
FAQ
How do you define Six Sigma?
Six-sigma will be well-known to anyone who has worked in operations research or statistics. However, anyone involved in any aspect of business can benefit from using it.
Because it requires a high level of commitment, only those with strong leadership skills will make an effort necessary to implement it successfully.
How does a manager learn to manage?
Good management skills are essential for success.
Managers need to monitor their subordinates' performance.
If you notice your subordinate isn't performing up to par, you must take action quickly.
It is important to be able identify areas that need improvement and what can be done to improve them.
What is the difference in Six Sigma and TQM?
The main difference between these two quality management tools is that six sigma focuses on eliminating defects while total quality management (TQM) focuses on improving processes and reducing costs.
Six Sigma is an approach for continuous improvement. It emphasizes the elimination and improvement of defects using statistical methods, such as control charts, P-charts and Pareto analysis.
This method seeks to decrease variation in product output. This is done by identifying root causes and rectifying them.
Total quality management refers to the monitoring and measurement of all aspects in an organization. It also involves training employees to improve performance.
It is commonly used as a strategy for increasing productivity.
What is Six Sigma, exactly?
This is a method of quality improvement that emphasizes customer service, continuous learning, and customer service. The objective is to eliminate all defects through statistical methods.
Motorola developed Six Sigma in 1986 to help improve its manufacturing processes.
The idea spread quickly in the industry. Today many organizations use six-sigma techniques to improve product design.
What does the term "project management” mean?
This refers to managing all activities that are involved in a project's execution.
This includes defining the scope, identifying the requirements and preparing the budget. We also organize the project team, schedule the work, monitor progress, evaluate results, and close the project.
What are some of the common mistakes made by managers?
Sometimes, managers make their job more difficult than it is.
They might not give enough support and delegate the right responsibilities to their staff.
Many managers lack the communication skills to motivate and lead their employees.
Some managers set unrealistic expectations for their staff.
Managers may prefer to solve every problem for themselves than to delegate responsibility.
Statistics
- UpCounsel accepts only the top 5 percent of lawyers on its site. (upcounsel.com)
- The average salary for financial advisors in 2021 is around $60,000 per year, with the top 10% of the profession making more than $111,000 per year. (wgu.edu)
- 100% of the courses are offered online, and no campus visits are required — a big time-saver for you. (online.uc.edu)
- Hire the top business lawyers and save up to 60% on legal fees (upcounsel.com)
- The profession is expected to grow 7% by 2028, a bit faster than the national average. (wgu.edu)
External Links
How To
How can you use the Kaizen method?
Kaizen means continuous improvement. This term was first used by Toyota Motor Corporation in the 1950s. It refers to the Japanese philosophy that emphasizes continuous improvement through small incremental changes. It's a process where people work together to improve their processes continuously.
Kaizen, a Lean Manufacturing method, is one of its most powerful. Kaizen is a concept where employees in charge of the production line are required to spot problems during the manufacturing process before they become major issues. This increases the quality of products and reduces the cost.
The main idea behind kaizen is to make every worker aware of what happens around him/her. So that there is no problem, you should immediately correct it if something goes wrong. So, if someone notices a problem while working, he/she should report it to his/her manager.
Kaizen follows a set of principles. We always start from the end product and move toward the beginning. In order to improve our factory's production, we must first fix the machines producing the final product. We then fix the machines producing components, and the machines producing raw materials. Then, we fix those who work directly with the machines.
This is known as "kaizen", because it emphasizes improving each step. We finish fixing the factory and then go back to the beginning. This continues until we achieve perfection.
How to measure kaizen's effectiveness in your business is essential to implement it. There are many methods to assess if kaizen works well. Another way to determine if kaizen is working well is to look at the quality of the products. Another way is to check how much productivity has grown since kaizen was implemented.
You can also find out if kaizen works by asking yourself why you decided to implement it. Was it just because it was the law or because you wanted to save money? Did you really believe it would lead to success?
Let's say you answered yes or all of these questions. Congratulations! You're ready to start kaizen.