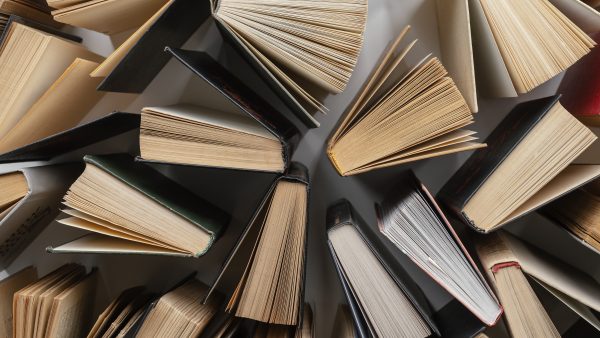
The hierarchy is a way to protect workers from dangers. In practice, it is used in many industries and is widely recognized by many safety organizations. It is taught to industry managers, who then implement it as a standard procedure. However, there are some variations of this system. Check out this guide to the NFPA70E hazard rating system and the ARECC variation. This will allow you to more easily apply the hierarchy to your workplace.
NFPA 70E
NFPA70E consists of a series of standards for workplace safety. New 2018 edition contains Annex Q, which describes human performance as well human error and potential consequences. This section also provides a hierarchy of control, which prioritizes the elimination of hazards. In the case of electrical hazards, eliminating the source of energy or hazard is the first step. Personal protective equipment should be used as a last resort only.
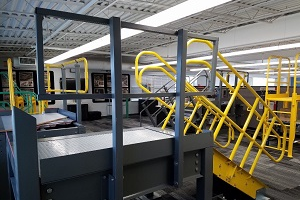
The next step in reducing the severity of risks is to assess the extent of your exposure. While engineering controls can reduce the amount of hazardous substances that are exposed, they cannot eliminate all hazards. The hierarchy is designed to minimize exposure to hazards and reduce their severity. A common example of an engineering control is a vapor or fog machine, a ventilation system or a fire alarm.
Appendices to the NFPA70E standard are also available. These appendices are documents that provide detailed instructions and guidelines on how to perform specific procedures. The appendices include sample forms, PPE guidance, design requirements, and risk assessment guidelines. Annexes can be used to guide you in implementing the standard, just like the main text. They can provide information that may prove helpful in ensuring the safety and security of buildings or workplaces.
ARECC variation
The ARECC variant in the hierarchy is a method to reduce the chance of being exposed to a given hazard. The system was originally used in the United States and Canada. However, it has been modified in other countries. Some countries put isolation before engineering controls while others combine both. The ARECC version includes employee training as well as warnings. But, warnings by themselves cannot eliminate all hazards.
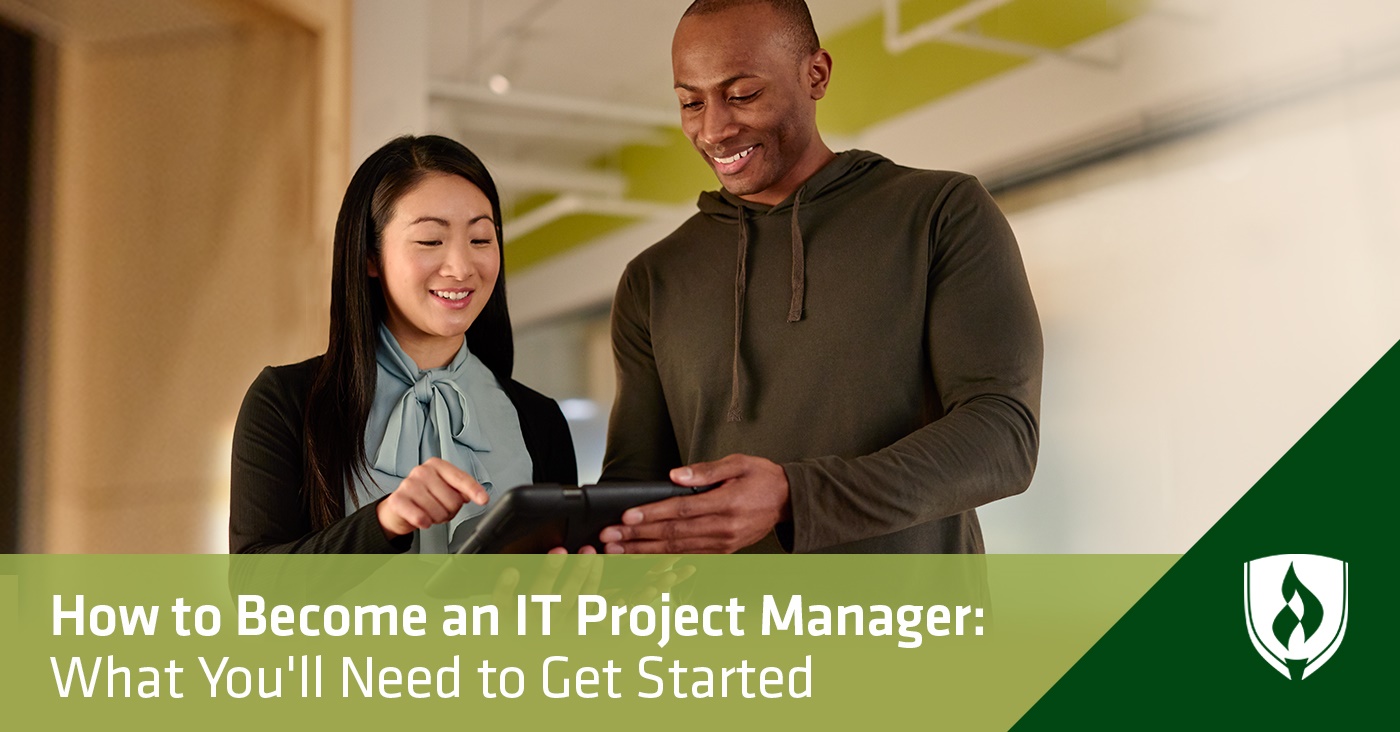
The ARECC hierarchy of controls is a framework for occupational safety and health. It determines possible solutions and prioritizes them according the effectiveness. In the hierarchy are five categories of controls: administrative, engineering, personal protective equipment and administrative. Each category has its strengths and weaknesses and is essential for a particular situation. Some controls within the ARECC hierarchy have greater effectiveness than others.
FAQ
How can we make our company culture successful?
A company culture that values and respects its employees is a successful one.
It's built on three fundamental principles:
-
Everybody can contribute something valuable
-
People are treated fairly
-
There is mutual respect between individuals and groups
These values can be seen in the behavior of people. They will show consideration and courtesy to others.
They will listen to other people's opinions respectfully.
These people will inspire others to share thoughts and feelings.
In addition, the company culture encourages open communication and collaboration.
People feel safe to voice their opinions without fear of reprisal.
They know that they will not be judged if they make mistakes, as long as the matter is dealt with honestly.
Finally, the company culture promotes integrity and honesty.
Everyone understands that the truth is always best.
Everyone understands that there are rules and regulations which apply to them.
Everyone does not expect to receive special treatment.
What is the difference of leadership and management?
Leadership is about influencing others. Management is about controlling others.
A leader inspires others while a manager directs them.
A leader motivates people to achieve success; a manager keeps workers on task.
A leader develops people; a manager manages people.
What is the difference between project and program?
A project is temporary; a program is permanent.
A project typically has a defined goal and deadline.
It is often done in a team that reports to another.
A program often has a set goals and objectives.
It is often implemented by one person.
What are management concepts, you ask?
Management concepts are the fundamental principles and practices that managers use when managing people and their resources. These include topics such as human resource policies and job descriptions, performance assessments, training programs and employee motivation.
How does Six Sigma work
Six Sigma uses statistical analysis to find problems, measure them, analyze root causes, correct problems, and learn from experience.
The first step to solving the problem is to identify it.
Next, data are collected and analyzed in order to identify patterns and trends.
Next, corrective steps are taken to fix the problem.
Final analysis of data is done to determine if the problem has been solved.
This cycle will continue until the problem is solved.
What is the difference between TQM and Six Sigma?
The key difference between the two quality management tools is that while six-sigma focuses its efforts on eliminating defects, total quality management (TQM), focuses more on improving processes and reducing cost.
Six Sigma can be described as a strategy for continuous improvement. It emphasizes the elimination of defects by using statistical methods such as control charts, p-charts, and Pareto analysis.
The goal of this method is to reduce variation in product output. This is done by identifying and correcting the root causes of problems.
Total quality management involves measuring and monitoring all aspects of the organization. It also involves training employees to improve performance.
It is used to increase productivity.
Statistics
- Your choice in Step 5 may very likely be the same or similar to the alternative you placed at the top of your list at the end of Step 4. (umassd.edu)
- The profession is expected to grow 7% by 2028, a bit faster than the national average. (wgu.edu)
- As of 2020, personal bankers or tellers make an average of $32,620 per year, according to the BLS. (wgu.edu)
- The BLS says that financial services jobs like banking are expected to grow 4% by 2030, about as fast as the national average. (wgu.edu)
- UpCounsel accepts only the top 5 percent of lawyers on its site. (upcounsel.com)
External Links
How To
How can you implement a Quality Management Plan?
The Quality Management Plan (QMP) was established in ISO 9001. It is a systematic way to improve processes, products and services. It focuses on the ability to measure, analyze and control processes and customer satisfaction.
QMP is a standard way to improve business performance. QMP helps improve production, service delivery and customer relationships. QMPs should address all three dimensions: Products, Services, and processes. A "Process" QMP is one that only includes one aspect. QMPs that focus on a Product/Service are known as "Product" QMPs. QMP is also used to refer to QMPs that focus on customer relations.
When implementing a QMP, there are two main elements: Scope and Strategy. They can be described as follows:
Scope: This describes the scope and duration for the QMP. This will be used to define activities that are performed in the first six months of a QMP.
Strategy: This describes the steps taken towards achieving the goals set forth in the scope.
A typical QMP comprises five phases: Planning and Design, Development, Construction, Implementation, Maintenance. The following describes each phase.
Planning: This stage determines the QMP goals and prioritizes them. To understand the expectations and requirements of all stakeholders, the project is consulted. Once the objectives and priorities have been identified, it is time to plan the strategy to achieve them.
Design: The design stage involves the development of vision, mission strategies, tactics, and strategies that will allow for successful implementation. These strategies are implemented by the development of detailed plans and procedures.
Development: The development team is responsible for building the resources and capabilities necessary to implement the QMP effectively.
Implementation: This involves the actual implementation of the QMP using the planned strategies.
Maintenance: This is an ongoing procedure to keep the QMP in good condition over time.
Additionally, the QMP should include additional items:
Participation by Stakeholders is essential for the QMP's continued success. They should be involved in planning, design, development and implementation of the QMP.
Project Initiation: The initiation of any project requires a clear understanding of the problem statement and the solution. In other words, they must understand the motivation for initiating the project and the expectations of the outcome.
Time Frame: The time frame of the QMP is very critical. A simple version is fine if you only plan to use the QMP for a brief period. If you are looking for a longer-term commitment, however, you might need more complex versions.
Cost Estimation - Cost estimation is an important part of the QMP. Without knowing how much you will spend, planning is impossible. It is therefore important to calculate the cost before you start the QMP.
The most important thing about a QMP is that it is not just a document but also a living document. It changes with the company. It should therefore be reviewed frequently to ensure that the organization's needs are met.