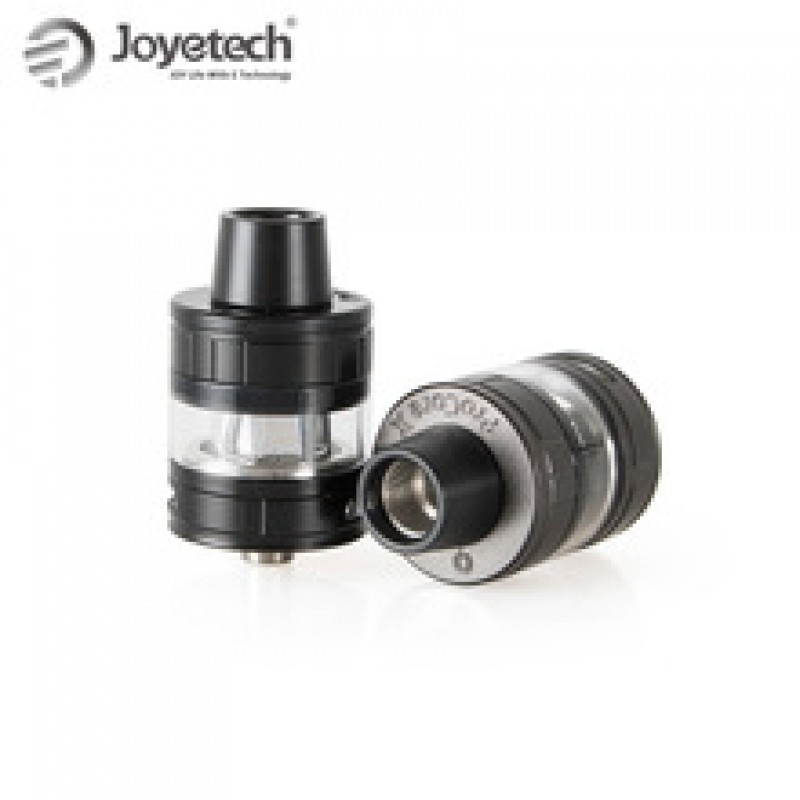
Crisis management is an integral part of an organization's strategy. It can either make or break an organization's performance. Its success depends on how well crisis managers use the lessons from their experience to improve their practices. Crisis managers have several psychological characteristics, including task-oriented leadership behavior and communication plan. This article will discuss these attributes and how to prepare for a crisis. After reading it you will be better equipped for handling a crises.
Psychological characteristics of crisis managers
Critical to their effectiveness, crisis managers must have strong psychological skills. They must be able communicate effectively, think rationally and not react too strongly to crisis situations. Empathy is one of the most important traits of crisis managers. Empathy is the ability of seeing the situation from the perspective of another person. They will not be able to make informed decisions without it. They should also be patient and avoid anxious thoughts.
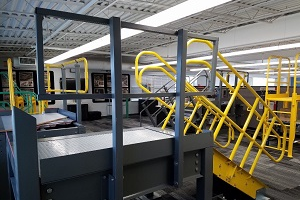
Task-oriented leadership behaviour
Although task-oriented leadership behavior may have its benefits, there are also dangers associated with this type of leadership. Tact-oriented leadership is not only counterproductive, but it can also lead to hostile working environments. In this article, we will look at some of the downsides of task-oriented leadership and how it can be detrimental to crisis managers. These are examples of when task-oriented leadership might not be the best choice for you if you're in a position where it is.
Preparation for crisis
While crises can happen to any organization, they can often be avoided by preparing ahead of time. A thorough assessment of the organization's vulnerabilities and potential points of crises is recommended by crisis management professionals. They also suggest conducting mock drills, and pre-drafting emergency messages. It is important to practice crisis management skills before an actual crisis occurs. This will make it easier for crisis response personnel to make the best decisions. Learn more by reading Crisis in Organizations II, Code Red in the Boardroom and Crisis in Organizations II.
Communication plan
A list of all contacts is an important step in developing a crisis communications plan. It is crucial to arrange the information in a prioritized way so that the most important customers can be reached first. You should also outline procedures for contacting suppliers during a crisis. This way you can communicate with suppliers whenever you need to and not rely on inefficient manual processes.
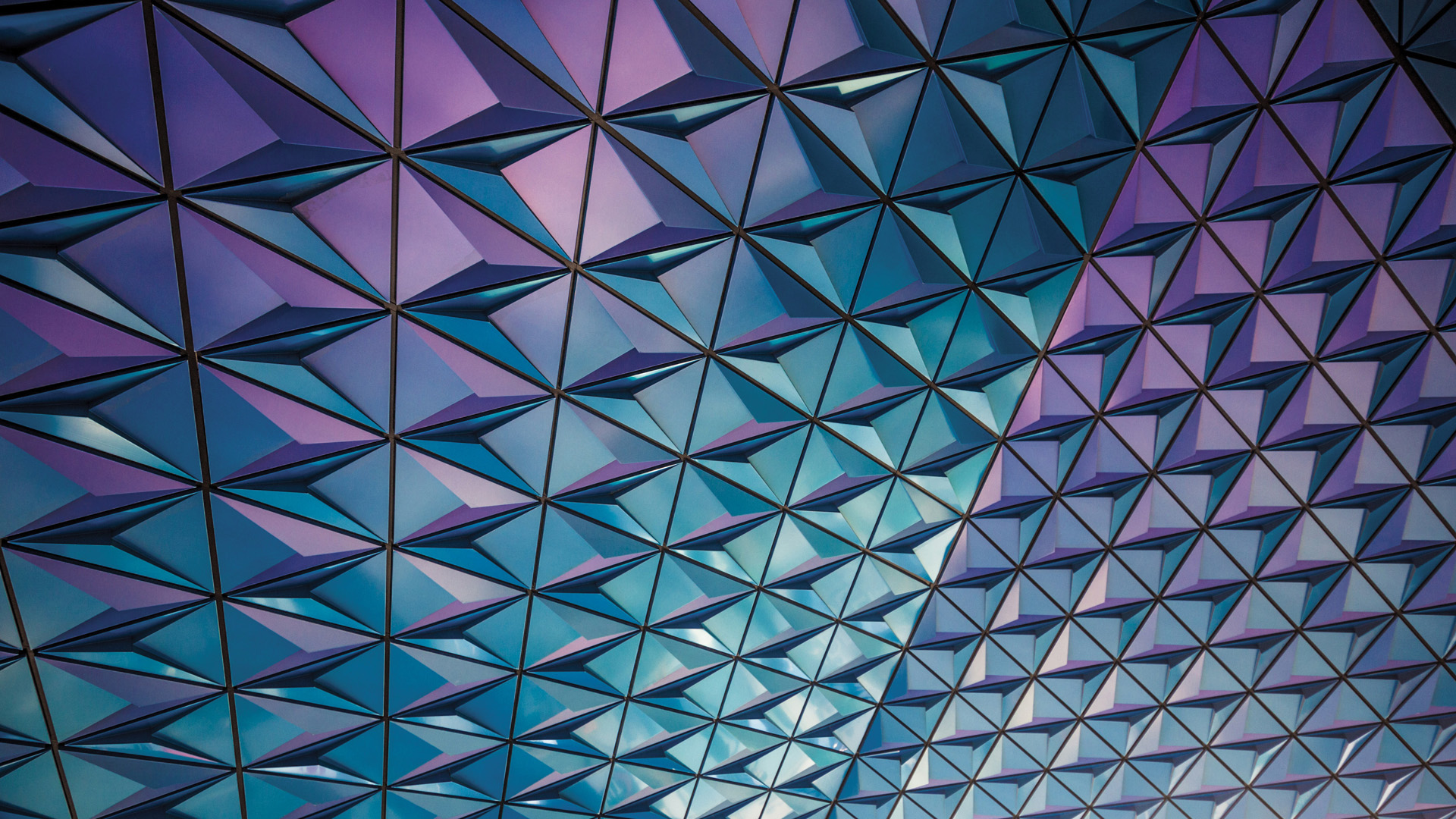
Public relations damage control
Managing PR mistakes is crucial if you want to prevent the situation from getting out of hand. Small businesses might not be able to afford a crisis management company, but they can follow a protocol for handling public relations issues. By tackling issues before they get out of hand, you'll avoid a crisis that could affect your reputation and business. A proactive approach is better than waiting for controversy to end.
FAQ
What is Kaizen?
Kaizen is a Japanese term meaning "continuous improvement." It is a philosophy that encourages employees to constantly look for ways to improve their work environment.
Kaizen is built on the belief that everyone should be able do their jobs well.
What is a fundamental management tool for decision-making?
A decision matrix can be a simple, but effective tool to assist managers in making decisions. It allows them to think through all possible options.
A decision matrix represents alternatives in rows and columns. This allows you to easily see how each choice affects others.
This example shows four options, each represented by the boxes on either side of the matrix. Each box represents an alternative. The status quo (the current condition) is shown in the top row, and what would happen if there was no change?
The effect of choosing Option 1 can be seen in column middle. This would result in an increase of sales of $2 million to $3million.
The effects of options 2 and 3 are shown in the next columns. These are positive changes - they increase sales by $1 million and $500 thousand respectively. These changes can also have negative effects. For instance, Option 2 increases cost by $100 thousand while Option 3 reduces profits by $200 thousand.
The last column displays the results of selecting Option 4. This results in a decrease of sales by $1,000,000
The best thing about using a decision matrix is that you don't need to remember which numbers go where. It's easy to see the cells and instantly know if any one of them is better than another.
The matrix already does all the work. It's simply a matter of comparing the numbers in the relevant cells.
Here is an example of how a decision matrix might be used in your business.
It is up to you to decide whether to spend more money on advertising. This will allow you to increase your revenue by $5000 per month. However, this will mean that you'll have additional expenses of $10,000.
The net result of advertising investment can be calculated by looking at the cell below that reads "Advertising." It is 15 thousand. Advertising is worth much more than the investment cost.
Why is it important that companies use project management methods?
Project management techniques are used in order to ensure projects run smoothly, and that deadlines are met.
This is because most businesses rely heavily on project work to produce goods and services.
These projects require companies to be efficient and effective managers.
Companies could lose their time, reputation, and money without effective project management.
What is TQM?
When manufacturing companies realized that price was not enough to compete, the industrial revolution brought about the quality movement. They had to improve efficiency and quality if they were to remain competitive.
To address this need for improvement management created Total Quality Management (TQM) which aimed to improve all aspects of an organization's performance. It included continuous improvement processes, employee involvement, and customer satisfaction.
Statistics
- This field is expected to grow about 7% by 2028, a bit faster than the national average for job growth. (wgu.edu)
- The average salary for financial advisors in 2021 is around $60,000 per year, with the top 10% of the profession making more than $111,000 per year. (wgu.edu)
- The BLS says that financial services jobs like banking are expected to grow 4% by 2030, about as fast as the national average. (wgu.edu)
- Hire the top business lawyers and save up to 60% on legal fees (upcounsel.com)
- As of 2020, personal bankers or tellers make an average of $32,620 per year, according to the BLS. (wgu.edu)
External Links
How To
How can Lean Manufacturing be done?
Lean Manufacturing is a method to reduce waste and increase efficiency using structured methods. They were created in Japan by Toyota Motor Corporation during the 1980s. The goal was to produce quality products at lower cost. Lean manufacturing eliminates unnecessary steps and activities from a production process. It consists of five basic elements: pull systems, continuous improvement, just-in-time, kaizen (continuous change), and 5S. It is a system that produces only the product the customer requests without additional work. Continuous improvement involves constantly improving upon existing processes. Just-in time refers to components and materials being delivered right at the place they are needed. Kaizen means continuous improvement, which is achieved by implementing small changes continuously. Finally, 5S stands for sort, set in order, shine, standardize, and sustain. To achieve the best results, these five elements must be used together.
The Lean Production System
Six key concepts make up the lean manufacturing system.
-
Flow is about moving material and information as near as customers can.
-
Value stream mapping- This allows you to break down each step of a process and create a flowchart detailing the entire process.
-
Five S's – Sort, Put In Order Shine, Standardize and Sustain
-
Kanban – visual signals like colored tape, stickers or other visual cues are used to keep track inventory.
-
Theory of constraints - identify bottlenecks during the process and eliminate them with lean tools like Kanban boards.
-
Just-intime - Order components and materials at your location right on the spot.
-
Continuous improvement - Make incremental improvements rather than overhauling the entire process.