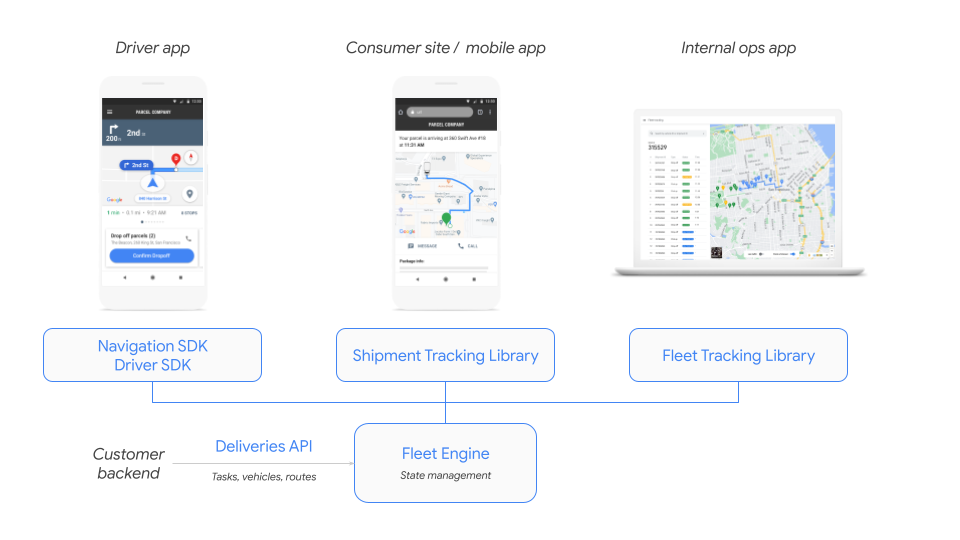
Managers are often used, no matter what your job title is. This term describes someone who influences, leads, controls or directs others. It's also a synonym to the word leader. In today's world of business, managers are valued for their ability to communicate effectively. They need to be able to communicate openly with their staff members. Management is not an all-encompassing solution.
Synonyms
A database of words with similar meanings is necessary in order to manage synonyms. Using synonyms should be used with caution, as using them in excess will lead to unexpected results. These results can cause confusion. Many users mistakenly use synonyms and then attempt to fix it with different settings. If you are one of these users, the following tips can help you to use synonyms correctly.
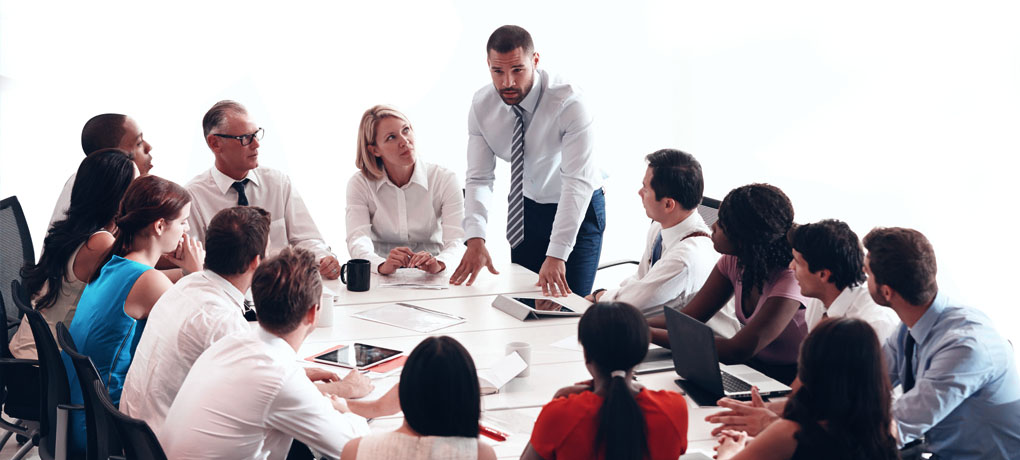
The default behavior of using synonyms is to apply them to all index replicas. This behavior can be avoided by unchecking the checkbox. Similarly, synonyms that are used for plural and singular words should be avoided. They don't guarantee the same results. After making the necessary changes, the synonym can be used to manage to synonym. The system will save a duplicate of the synonym to you database.
Meaning of manage
Management is defined by the dictionary as "to control, supervise or direct an activity." This broad definition could include everything from goldfish to college finance management. Managers in business can manage others' work or deal with stress. A manager is someone who can manage people and make sure they achieve the goals they set for their team.
There are several synonyms to the word manage. These include direct and conduct. Manage refers to manipulating people or groups in order achieve a certain goal. Control refers to the regulation and restriction of group behavior. These terms are often used together. These synonyms can help you understand the relationship between these words. These examples can help you to understand the meaning of a word if you aren't sure how to use it.
Management as a distinct process
Management can be used to refer to a wide range of functions, processes, strategies, and purposes. It is a complex process that focuses on planning, organizing, and controlling a set of resources. This involves various methods to achieve a specified purpose. Terry's definitions of management include the activities required to achieve company goals. It emphasizes the role of the person, which gives the company its unique character as social processes.
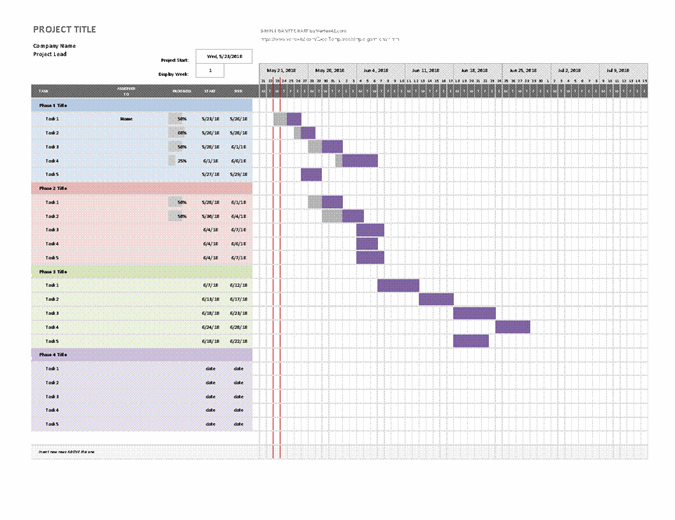
Management is a social process responsible for organizing, planning, ordering, co-ordinating and controlling others. In contrast, the contribution of a non-manager to the organization's goals can be direct and self-directed. This definition of management demonstrates how difficult it is for people to be managed. As such, management involves the planning, organizing, staffing, and leading efforts of the individuals involved in an organization.
FAQ
What is a management tool to help with decision-making?
A decision matrix is a simple but powerful tool for helping managers make decisions. They can think about all options and make informed decisions.
A decision matrix can be used to show alternative options as rows or columns. This allows one to see how each alternative impacts other options.
In this example, there are four possible options represented by boxes on the left-hand side of the matrix. Each box represents a different option. The top row displays the current situation, and the bottom row shows what might happen if nothing is done.
The effect of choosing Option 1 can be seen in column middle. This would result in an increase of sales of $2 million to $3million.
The next two columns show the effects of choosing Options 2 and 3. These are good changes, they increase sales by $1million or $500,000. They also have negative consequences. Option 2, for example, increases the cost by $100 000 while Option 3 decreases profits by $200 000.
The last column displays the results of selecting Option 4. This means that sales will decrease by $1 million.
A decision matrix has the advantage that you don’t have to remember where numbers belong. Simply look at the cells to instantly determine if one choice is better than the other.
This is because the matrix has already taken care of the hard work for you. It's simply a matter of comparing the numbers in the relevant cells.
Here's an example showing how you might use a Decision Matrix in your business.
Advertising is a decision that you make. You'll be able increase your monthly revenue by $5000 if you do. You will still have to pay $10000 per month in additional expenses.
If you look at the cell that says "Advertising", you can see the number $15,000. Advertising is more valuable than its costs.
How do you effectively manage employees?
Effectively managing employees requires that you ensure their happiness and productivity.
It means setting clear expectations for them and keeping an eye on their performance.
Managers must set clear goals for their employees and themselves to achieve this goal.
They need to communicate clearly and openly with staff members. They need to communicate clearly with their staff.
They also need to keep records of their team's activities. These include:
-
What did we accomplish?
-
How much work did you put in?
-
Who did it?
-
How did it get done?
-
Why?
This data can be used to evaluate and monitor performance.
How does a manager motivate his/her employees?
Motivation is the desire for success.
Doing something that is enjoyable can help you get motivated.
Or you can get motivated by seeing yourself making a contribution to the success of the organization.
For example: If you want to be a doctor, you might find it more motivating seeing patients than reading medical books all day.
A different type of motivation comes directly from the inside.
One example is a strong sense that you are responsible for helping others.
Perhaps you enjoy working hard.
If you don't feel motivated, ask yourself why.
You can then think of ways to improve your motivation.
What is TQM exactly?
The industrial revolution led to the birth and growth of the quality movement. Manufacturing companies realized they couldn't compete solely on price. To remain competitive, they had to improve quality as well as efficiency.
Management developed Total Quality Management to address the need for improvement. It focused on all aspects of an organisation's performance. It involved continuous improvement, employee participation, and customer satisfaction.
What is Six Sigma?
Six Sigma uses statistical analyses to locate problems, measure them, analyze root cause, fix problems and learn from the experience.
The first step is to identify the problem.
The next step is to collect data and analyze it in order to identify trends or patterns.
Then corrective actions are taken to solve the problem.
Finally, data will be reanalyzed to determine if there is an issue.
This cycle continues until there is a solution.
Why is it so important for companies that they use project management techniques
Project management techniques can be used to ensure smooth project execution and meeting deadlines.
This is due to the fact that most businesses rely heavily upon project work in order to produce goods, and services.
These projects must be managed efficiently and effectively by companies.
Companies could lose their time, reputation, and money without effective project management.
Statistics
- Our program is 100% engineered for your success. (online.uc.edu)
- The profession is expected to grow 7% by 2028, a bit faster than the national average. (wgu.edu)
- Your choice in Step 5 may very likely be the same or similar to the alternative you placed at the top of your list at the end of Step 4. (umassd.edu)
- 100% of the courses are offered online, and no campus visits are required — a big time-saver for you. (online.uc.edu)
- The average salary for financial advisors in 2021 is around $60,000 per year, with the top 10% of the profession making more than $111,000 per year. (wgu.edu)
External Links
How To
How does Lean Manufacturing work?
Lean Manufacturing processes are used to reduce waste and improve efficiency through structured methods. They were developed in Japan by Toyota Motor Corporation (in the 1980s). The goal was to produce quality products at lower cost. Lean manufacturing is about eliminating redundant steps and activities from the manufacturing process. It has five components: continuous improvement and pull systems; just-in time; continuous change; and kaizen (continuous innovation). Pull systems are able to produce exactly what the customer requires without extra work. Continuous improvement involves constantly improving upon existing processes. Just-in-time refers to when components and materials are delivered directly to the point where they are needed. Kaizen stands for continuous improvement. Kaizen can be described as a process of making small improvements continuously. The 5S acronym stands for sort in order, shine standardize and maintain. These five elements are combined to give you the best possible results.
Lean Production System
The lean production system is based on six key concepts:
-
Flow - focuses on moving information and materials as close to customers as possible.
-
Value stream mapping - Break down each stage in a process into distinct tasks and create an overview of the whole process.
-
Five S's – Sort, Put In Order Shine, Standardize and Sustain
-
Kanban: Use visual signals such stickers, colored tape, or any other visual cues, to keep track your inventory.
-
Theory of constraints - identify bottlenecks during the process and eliminate them with lean tools like Kanban boards.
-
Just-in time - Get components and materials delivered right at the point of usage;
-
Continuous improvement - incremental improvements are made to the process, not a complete overhaul.