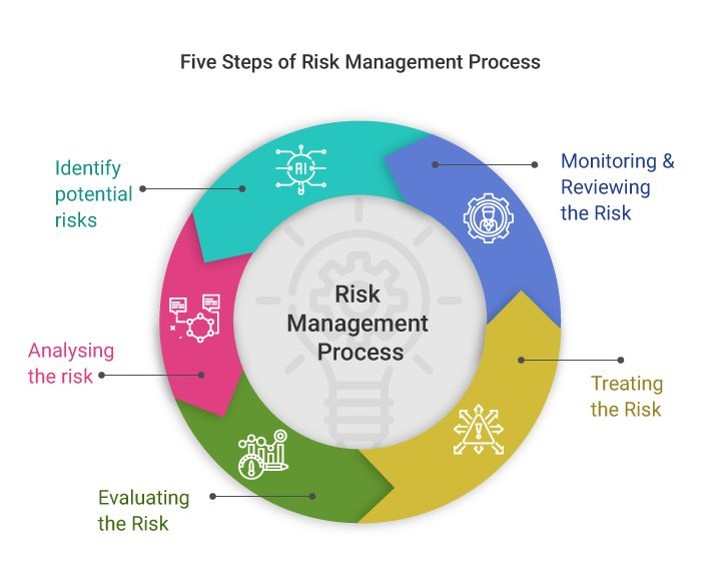
A company must follow 14 elements in order be considered as a PSM program. These elements are Process hazard analysis, Permissible exposure limits and Physical data. These requirements are vital for the effective operation of a PSM program. These elements will ensure that your PSM program is compliant. These elements are described and illustrated in the following sections.
Process hazard analyses
An essential element of any safety management program is the process hazard analysis. It helps identify potential hazards and evaluate the consequences of failure. This analysis must be done by a team of employees who are knowledgeable about the process. It will include human factors and previous incidents and reviews the siting of the facility. The analysis must be reviewed every five years after it is completed. The safety management system must include hazard analysis.
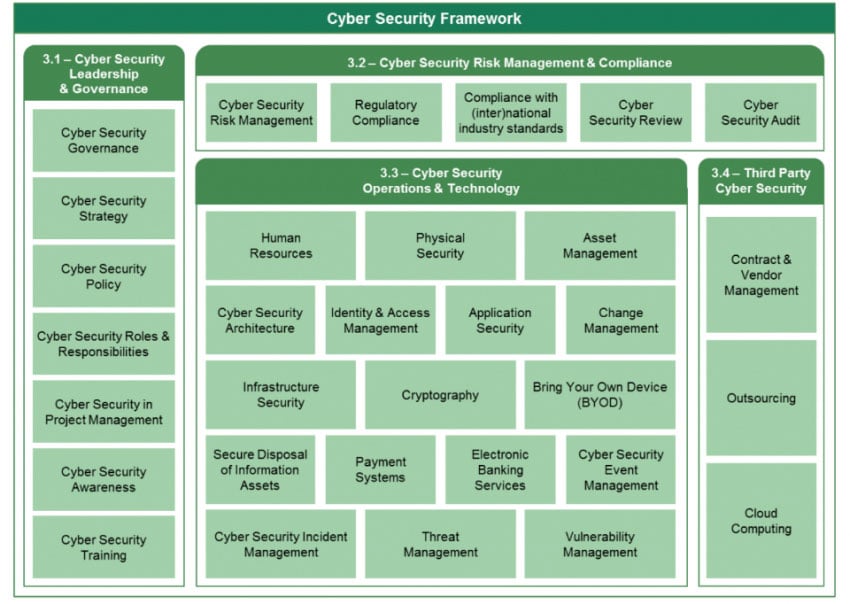
Permissible exposure limits
OSHA Process Safety Management Standard is a set standards that govern processes that involve hazardous chemicals, gases, or fluids. The standard is applicable to businesses who produce or process dangerous chemicals. It does not apply to hydrocarbon fuels used solely for workplace use or to retail or oil and gas well drilling. It does not apply to facilities that are normally vacant or remote.
Physical data
PSM is the process that analyzes and controls the risk associated with hazardous materials and products. This includes knowing how to transport, handle, and store hazardous substances safely. This can result in less product waste, and fewer workplace accidents. It simplifies decision-making and makes organizations safer and more productive. PSM is an essential part of a safe workplace. It also helps organizations avoid health emergencies and reduce costs.
Data on corrosivity
The PSM standard defines requirements for handling and storing chemicals and other substances that may cause damage to buildings and equipment. The PSM requires periodic compliance audits and includes requirements for emergency plans and permit system. PSM-compliant workplaces will provide safety and protection for employees, no matter how hazardous your organization's production processes are.
Thermal stability data
OSHA has developed a standard for collecting and reporting PSM thermal stability data. This program will help researchers be aware of potential hazards and reduce the risk of accidental releases. It will be reviewed frequently and revised to address the tasks of new research projects. It will be made available to all employees. It includes information about toxicity, reactivity and physical properties.
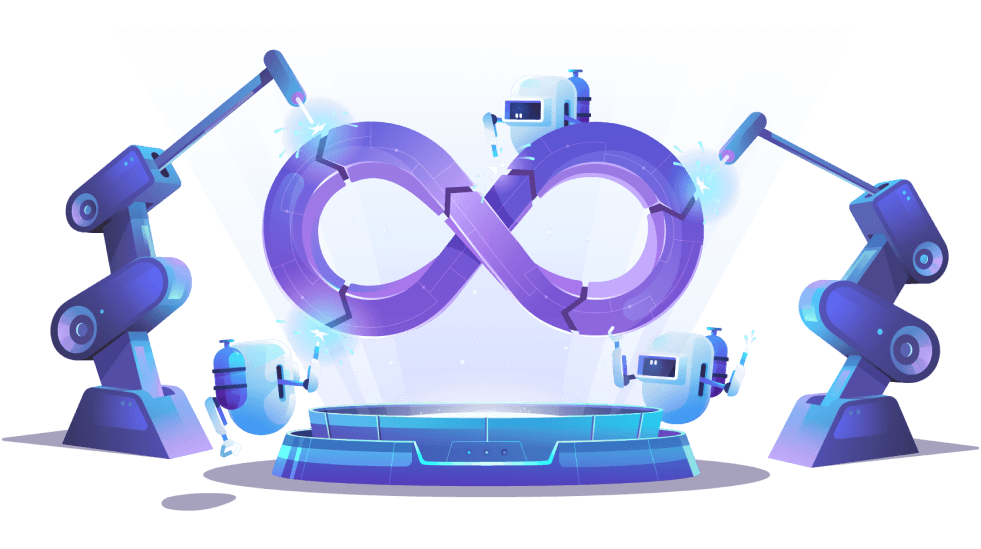
Employee participation clause
Process Safety Management (PSM) is a systematic analytical approach to the prevention of process accidents caused by highly hazardous chemicals (HHC). It is an important step toward improving process safety. It must be implemented at every level of the plant, from maintenance to production. It includes 14 elements, which should all be implemented, as well as employee participation clauses. These elements and their requirements are listed below.
FAQ
What is Kaizen and how can it help you?
Kaizen is a Japanese term meaning "continuous improvement." It is a philosophy that encourages employees to constantly look for ways to improve their work environment.
Kaizen is founded on the belief of everyone being able to do their job well.
How does Six Sigma work
Six Sigma uses statistical analyses to locate problems, measure them, analyze root cause, fix problems and learn from the experience.
The first step to solving the problem is to identify it.
Next, data will be collected and analyzed to determine trends and patterns.
Then, corrective actions can be taken to resolve the problem.
Finally, the data are reanalyzed in order to determine if it has been resolved.
This cycle will continue until the problem is solved.
What are management principles?
Management Concepts are the principles and practices managers use to manage people and resources. They cover topics like job descriptions (job descriptions), performance evaluations, training programmes, employee motivation and compensation systems.
What is the difference between TQM and Six Sigma?
The main difference between these two quality-management tools is that six-sigma concentrates on eliminating defects while total QM (TQM), focuses upon improving processes and reducing expenses.
Six Sigma is an approach for continuous improvement. It emphasizes the elimination or minimization of defects through statistical methods such control charts and p charts.
This method attempts to reduce variations in product output. This is done by identifying and correcting the root causes of problems.
Total Quality Management involves monitoring and measuring every aspect of the organization. It also includes the training of employees to improve performance.
It is often used as a strategy to increase productivity.
Why does it sometimes seem so difficult to make good business decisions?
Complex systems and many moving parts make up businesses. People who manage them have to balance multiple priorities while dealing with complexity and uncertainty.
It is important to understand the effects of these factors on the system in order to make informed decisions.
You need to be clear about the roles and responsibilities of each system. Then, you need to think about how these pieces interact with one another.
Also, you should ask yourself if there have been any assumptions in your past behavior. If they don't, you may want to reconsider them.
If you're still stuck after all this, try asking someone else for help. They might see things differently than you and may have some insights that could help find a solution.
What are the five management steps?
The five stages of a business include planning, execution (monitoring), review, evaluation, and review.
Setting goals for the future is part of planning. It involves setting goals and making plans.
Execution is the actual execution of the plans. Everyone involved must follow them.
Monitoring allows you to monitor your progress towards achieving your goals. Regular reviews of performance against budgets and targets should be part of this process.
Every year, there are reviews. They allow for an assessment of whether all went well throughout the year. If not, changes may be made to improve the performance next time around.
After the annual review, evaluation takes place. It helps to determine what worked and what didn’t. It provides feedback about how people perform.
What is a basic management tool used in decision-making?
A decision matrix is a simple but powerful tool for helping managers make decisions. They can think about all options and make informed decisions.
A decision matrix is a way of representing alternatives as rows and columns. It is easy to see how each option affects the other options.
We have four options in this example. They are represented by the boxes to the left of the matrix. Each box represents an option. The status quo (the current condition) is shown in the top row, and what would happen if there was no change?
The effect of choosing Option 1 can be seen in column middle. It would translate into an increase in sales from $2million to $3million.
The results of choosing Option 2 and 3 can be seen in the columns below. These are good changes, they increase sales by $1million or $500,000. However, these also involve negative consequences. Option 2 increases the cost of goods by $100,000. Option 3 decreases profits and makes them less attractive by $200,000.
The final column shows results of choosing Option 4. This results in a decrease of sales by $1,000,000
The best part about using a decision matrix to guide you is that you don’t need to keep track of which numbers go where. You just look at the cells and know immediately whether any given a choice is better than another.
This is because your matrix has already done the hard work. It is as simple a matter of comparing all the numbers in each cell.
Here is an example how you might use the decision matrix in your company.
You need to decide whether to invest in advertising. By doing so, you can increase your revenue by $5 000 per month. But, you will also incur additional expenses of $10 thousand per month.
You can calculate the net result of investing in advertising by looking at the cell directly below the one that says "Advertising." That number is $15 thousand. Advertising is worth more than its cost.
Statistics
- Our program is 100% engineered for your success. (online.uc.edu)
- The BLS says that financial services jobs like banking are expected to grow 4% by 2030, about as fast as the national average. (wgu.edu)
- Hire the top business lawyers and save up to 60% on legal fees (upcounsel.com)
- Your choice in Step 5 may very likely be the same or similar to the alternative you placed at the top of your list at the end of Step 4. (umassd.edu)
- The profession is expected to grow 7% by 2028, a bit faster than the national average. (wgu.edu)
External Links
How To
How can Lean Manufacturing be done?
Lean Manufacturing methods are used to reduce waste through structured processes. They were developed by Toyota Motor Corporation in Japan during the 1980s. The main goal was to produce products at lower costs while maintaining quality. Lean manufacturing is about eliminating redundant steps and activities from the manufacturing process. It is composed of five fundamental elements: continuous improvement; pull systems, continuous improvements, just-in–time, kaizen, continuous change, and 5S. Pull systems involve producing only what the customer wants without any extra work. Continuous improvement is the continuous improvement of existing processes. Just-in-time refers to when components and materials are delivered directly to the point where they are needed. Kaizen refers to continuous improvement. It is achieved through small changes that are made continuously. Last but not least, 5S is for sort. To achieve the best results, these five elements must be used together.
Lean Production System
Six key concepts form the foundation of the lean production system:
-
Flow - The focus is on moving information and material as close as possible to customers.
-
Value stream mapping: This is a way to break down each stage into separate tasks and create a flowchart for the entire process.
-
Five S’s - Sorted, In Order. Shine. Standardize. And Sustain.
-
Kanban: Use visual signals such stickers, colored tape, or any other visual cues, to keep track your inventory.
-
Theory of constraints: identify bottlenecks in your process and eliminate them using lean tools, such as kanban board.
-
Just-intime - Order components and materials at your location right on the spot.
-
Continuous improvement: Make incremental improvements to the process instead of overhauling it completely.