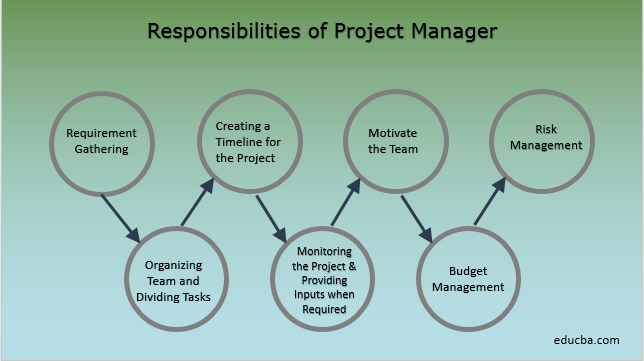
A project manager, or professional responsible for managing projects, is a person who works in the management of those projects. They are responsible to plan, procure, and execute projects. They are responsible for defining the project's scope. These tasks can be quite challenging but project managers have an exceptional skill set which is often highly appreciated in the workplace.
Establishing a company culture
Understanding how to communicate with an organization's culture is key to creating a company culture as project managers. This helps ensure consistency in project management and allows the new employee to be integrated into the company. There are many different corporate cultures to choose from, including some that are strict and others that are more relaxed.
The pace and time taken to complete a project can be affected by the organization's culture. An organization's culture should be able to differentiate itself from the competition and improve communication among its employees. A culture is defined by the values and behaviors shared by employees. These shared values may be influenced in part by the company's past and management.
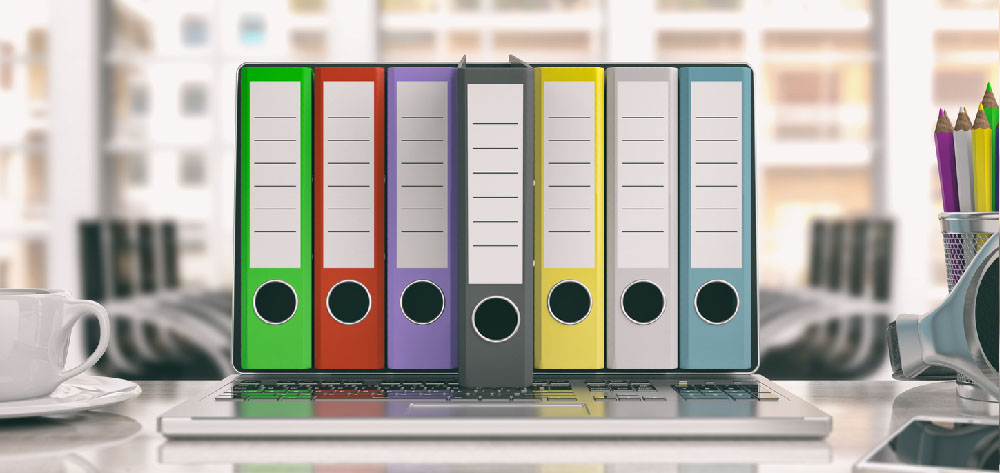
Motivation of team members
Motivation of your team members is a key element in managing a project. Demotivated team members can cause delays in the completion of tasks. It is possible to boost morale, and improve performance by following just a few steps. First, learn about the needs of your team members. This knowledge will allow you and your team to position them for optimal performance.
Once you know the motivational needs your team members have, you can begin to create a positive and supportive environment. This can be done by rewarding team members and giving them recognition. This will enable you to be the champion of your group and give each member a level of recognition. This can be a great way to motivate team members. Don't wait for problems to arise. Motivation requires a lot collaboration and teamwork.
Setting deadlines
To manage time effectively, it is important to set deadlines. There is only so much time in a day. If you don't keep track of it, you might miss important tasks or pile up your to-do lists. Another option is to be flexible and not give deadlines. Here are some guidelines to help you set deadlines efficiently: A. Be realistic
b. Communication is key. You must communicate clearly with all members of your team about the project's deadline and expectations for success. Your team members must communicate clearly with you about their resources and deadlines. You also need to be clear about any problems or obstacles that are coming up during the project. This will help you stay motivated and get the results that you need.
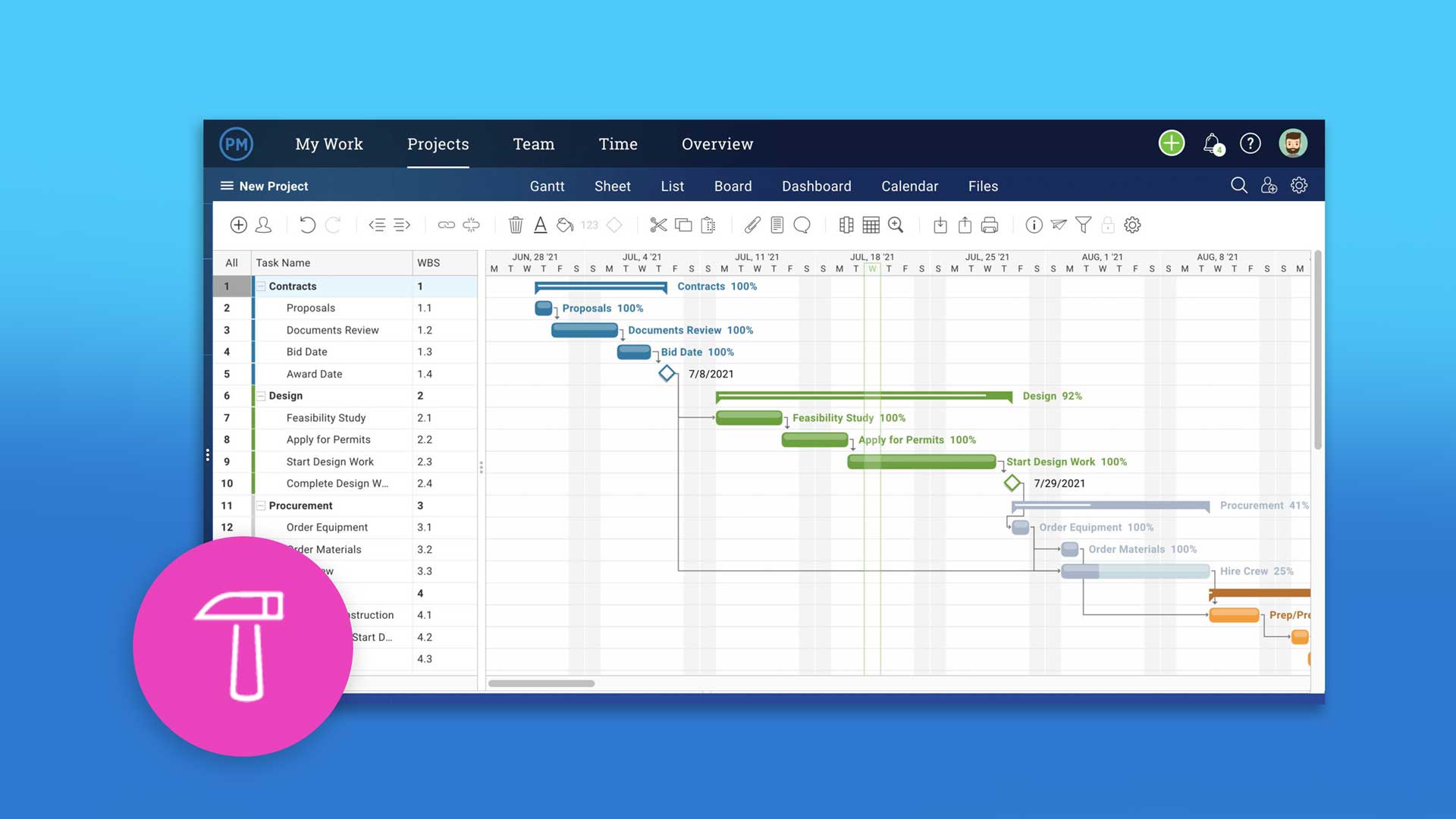
Resources management
Resource management is an important part of project management, and it can help you monitor the availability of team members and predict deadlines. An effective resource management plan is a great way of measuring a team’s capacity and can prevent issues such as burnout or under-using resources. You, your team and your business will all benefit from a good resource management plan.
Resource management is vital to a successful project. It also helps you improve team performance, engagement, and productivity. It is also crucial to understand how to allocate project budget and resources. The best resource management strategies also ensure that you're using billable resources efficiently and effectively.
FAQ
Why is project management so important?
Project management techniques ensure that projects run smoothly while meeting deadlines.
Because most businesses depend heavily on project work to produce goods or services,
These projects must be managed efficiently and effectively by companies.
Companies could lose their time, reputation, and money without effective project management.
What is the difference between Six Sigma Six Sigma and TQM?
The main difference between these two quality management tools is that six sigma focuses on eliminating defects while total quality management (TQM) focuses on improving processes and reducing costs.
Six Sigma can be described as a strategy for continuous improvement. It emphasizes the elimination of defects by using statistical methods such as control charts, p-charts, and Pareto analysis.
The goal of this method is to reduce variation in product output. This is done by identifying and correcting the root causes of problems.
Total quality management refers to the monitoring and measurement of all aspects in an organization. This includes training employees to improve their performance.
It is commonly used as a strategy for increasing productivity.
What are the steps that management takes to reach a decision?
Managers are faced with complex and multifaceted decisions. It involves many elements, including analysis, strategy. planning. implementation. measurement. evaluation. feedback.
It is important to remember that people are human beings, just like you. They make mistakes. As such, there are always opportunities for improvement, especially when you put in the effort to improve yourself.
This video will explain how decision-making works in Management. We'll discuss the different types and reasons they are important. Managers should also know how to navigate them. Here are some topics you'll be learning about:
How can a manager motivate employees?
Motivation is the desire for success.
Engaging in something fun can be a great way to get motivated.
You can also get motivated by seeing your contribution to the success or the improvement of the organization.
You might find it more rewarding to treat patients than to study medical books if you plan to become a doctor.
A different type of motivation comes directly from the inside.
Perhaps you have a strong sense to give back, for example.
Perhaps you enjoy working hard.
If you don’t feel motivated, find out why.
Next, think of ways you can improve your motivation.
Statistics
- The profession is expected to grow 7% by 2028, a bit faster than the national average. (wgu.edu)
- Our program is 100% engineered for your success. (online.uc.edu)
- The BLS says that financial services jobs like banking are expected to grow 4% by 2030, about as fast as the national average. (wgu.edu)
- Your choice in Step 5 may very likely be the same or similar to the alternative you placed at the top of your list at the end of Step 4. (umassd.edu)
- UpCounsel accepts only the top 5 percent of lawyers on its site. (upcounsel.com)
External Links
How To
How is Lean Manufacturing done?
Lean Manufacturing techniques are used to reduce waste while increasing efficiency by using structured methods. They were created by Toyota Motor Corporation in Japan in the 1980s. The aim was to produce better quality products at lower costs. Lean manufacturing emphasizes removing unnecessary steps from the production process. It has five components: continuous improvement and pull systems; just-in time; continuous change; and kaizen (continuous innovation). The production of only what the customer needs without extra work is called pull systems. Continuous improvement involves constantly improving upon existing processes. Just-intime refers the time components and materials arrive at the exact place where they are needed. Kaizen refers to continuous improvement. It is achieved through small changes that are made continuously. Finally, 5S stands for sort, set in order, shine, standardize, and sustain. These five elements work together to produce the best results.
The Lean Production System
Six key concepts make up the lean manufacturing system.
-
Flow: The goal is to move material and information as close as possible from customers.
-
Value stream mapping- This allows you to break down each step of a process and create a flowchart detailing the entire process.
-
Five S's - Sort, Set In Order, Shine, Standardize, and Sustain;
-
Kanban – visual signals like colored tape, stickers or other visual cues are used to keep track inventory.
-
Theory of constraints: identify bottlenecks in your process and eliminate them using lean tools, such as kanban board.
-
Just-in time - Get components and materials delivered right at the point of usage;
-
Continuous improvement - make incremental improvements to the process rather than overhauling it all at once.