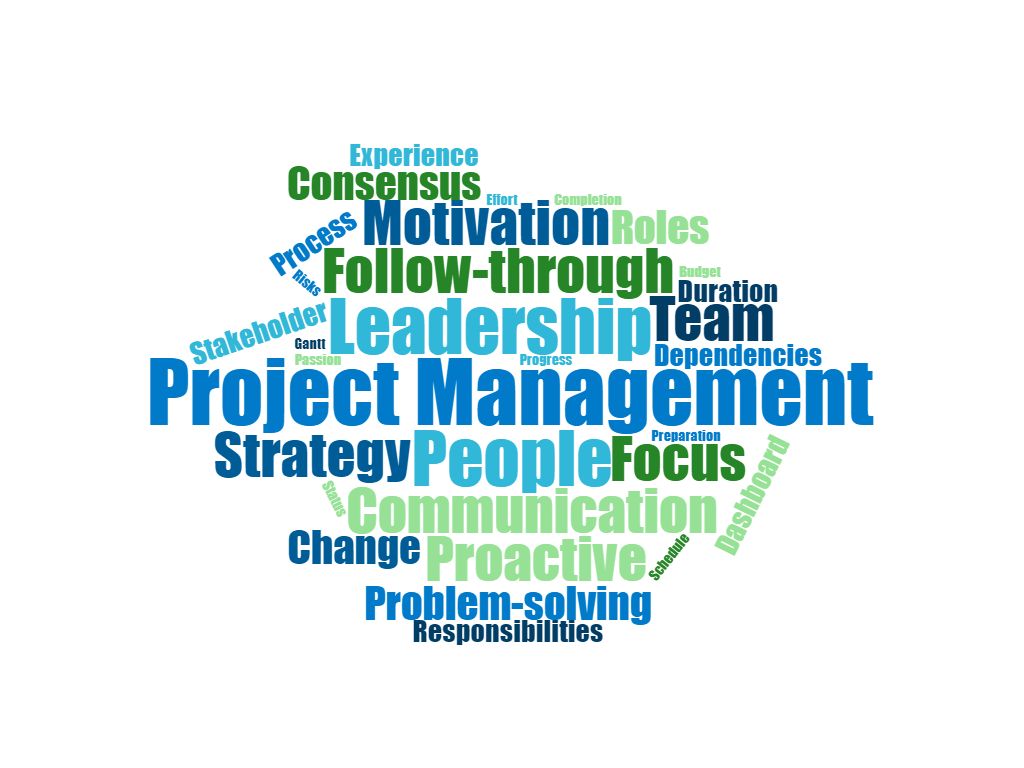
Before deciding whether to get a Human resource management certificate or a degree, you should know about the benefits and disadvantages of each. In this article, you'll learn more about the benefits of a degree in HR and the different certifications available. Learn more about the aPHR, GPHR and other certifications. Both are very beneficial but you should choose the one that suits your career best.
Certificate in human resources management
A certificate in human resources management is a better choice than a degree. It will help you find a career that meets your professional and personal goals. Certificate programs are often subsets of degree programs, and you should check to see if the underlying program meets the SHRM's curriculum guidelines. The certificate program is a quick and convenient way to obtain the training you desire. A certificate can be a great choice if you want to work in human resource management but don’t have the money or time to complete a full-time degree.
Human resource management degree
There are many opportunities to further your education within the HR field. The certificate program can be followed by a degree in human resource management. A certificate program focuses on practical applications instead of theoretical knowledge, and graduates of these programs will be able to apply the skills they learned in the classroom to their job. Certificate programs can be obtained online. Additionally, many of these programs offer flexible scheduling options and are well-suited for working professionals.
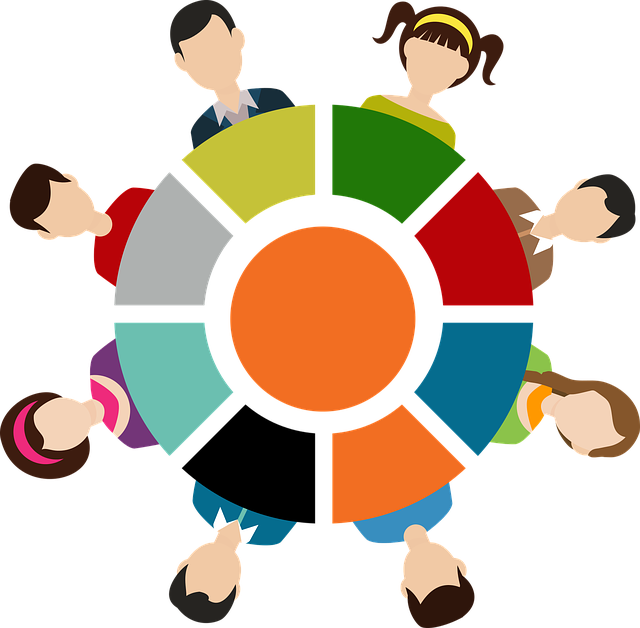
GPHR certificate
You can advance your career by obtaining a Human resource management certificate/degree. Both programs provide a range of benefits such as higher starting salaries and career advancement. A degree program will not only teach the basics of HR but also give you the ability to apply theoretical knowledge in real-world situations. Many employers prefer graduates with a graduate degree. Furthermore, HR professionals who obtain a bachelor’s degree often receive financial aid to continue their education, such a grant.
APHR certification
A certificate program is a good option for those looking to work in human resources. A certificate program is more affordable than a degree, even though it may be more specific. A certificate program will provide students with the skills necessary to land a top-level HR job. A certificate program is also much more flexible than a degree program. You can start in the fall, spring or summer, depending on how you work. These programs emphasize flexibility as well as leadership.
aPHR program
It is important to take into account several things when choosing a Human Resource Management certification program over a degree. A certificate program can be highly beneficial for those seeking new skills or a more advanced education. These programs can be accessed online and provide the knowledge and skills that students need to succeed in the chosen field. In addition, certificate programs typically offer more flexibility than a degree program. You can, for example, choose to obtain a certificate on human resources if you are already working in that field.
Online certificate programs
The career goals of each person will dictate which certificate program they choose. Whether you want to be a recruitment specialist or a strategist, you can choose from one of the many HR certifications offered. A bachelor's degree is required for most HR managers, but there are graduate and postgraduate certificate programs. While the certificate programs are usually shorter than a degree they will teach you a lot more about the field.
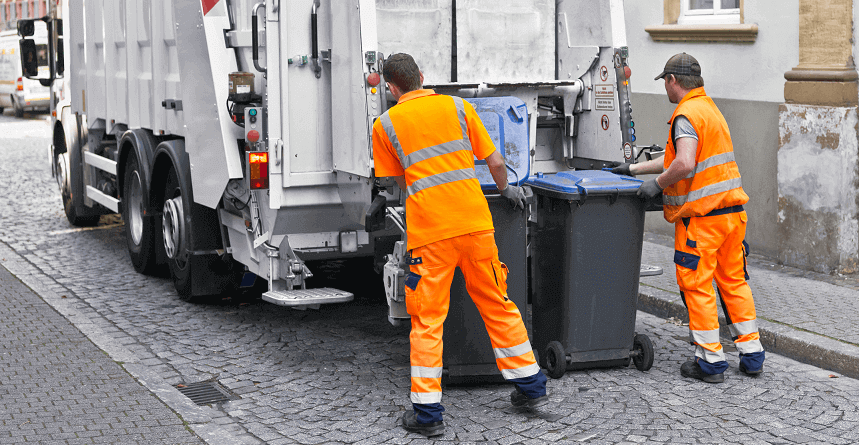
Transfer credits
A certificate or degree in human resources may be right for you if you're interested in a career. The field of human resources requires a variety of skills and knowledge. While some employers will consider people's experience when promoting them, others will look at their educational and training history. A bachelor's degree will get you started but further education will improve your prospects of advancement.
FAQ
What kind of people use Six Sigma?
Six-sigma will be well-known to anyone who has worked in operations research or statistics. But anyone can benefit from it.
This requires a lot of dedication, so only people with great leadership skills can make the effort to implement it.
What are the main styles of management?
The three basic management styles are: authoritarian, laissez-faire, and participative. Each style is unique and has its strengths as well as weaknesses. What style do you prefer? Why?
Autoritarian - The leader sets direction and expects everyone else to follow it. This style works well if an organization is large and stable.
Laissez-faire: The leader lets each person decide for themselves. This style is best when the organization has a small but dynamic group.
Participative: The leader listens to everyone's ideas and suggestions. This is a great style for smaller organizations that value everyone.
What is the main difference between Six Sigma Six Sigma TQM and Six Sigma Six Sigma?
The key difference between the two quality management tools is that while six-sigma focuses its efforts on eliminating defects, total quality management (TQM), focuses more on improving processes and reducing cost.
Six Sigma is a method for continuous improvement. It emphasizes the elimination and improvement of defects using statistical methods, such as control charts, P-charts and Pareto analysis.
This method attempts to reduce variations in product output. This is done by identifying root causes and rectifying them.
Total quality management refers to the monitoring and measurement of all aspects in an organization. Training employees is also part of total quality management.
It is used to increase productivity.
What is Six Sigma?
It is a way to improve quality that places emphasis on customer service and continuous learning. The goal is to eradicate defects through statistical techniques.
Motorola's 1986 efforts to improve manufacturing process efficiency led to the creation of Six Sigma.
This idea quickly spread throughout the industry. Today, many organizations use six sigma methods for product design, production and delivery.
Statistics
- The average salary for financial advisors in 2021 is around $60,000 per year, with the top 10% of the profession making more than $111,000 per year. (wgu.edu)
- Hire the top business lawyers and save up to 60% on legal fees (upcounsel.com)
- Your choice in Step 5 may very likely be the same or similar to the alternative you placed at the top of your list at the end of Step 4. (umassd.edu)
- Our program is 100% engineered for your success. (online.uc.edu)
- The BLS says that financial services jobs like banking are expected to grow 4% by 2030, about as fast as the national average. (wgu.edu)
External Links
How To
What is Lean Manufacturing?
Lean Manufacturing processes are used to reduce waste and improve efficiency through structured methods. They were developed in Japan by Toyota Motor Corporation (in the 1980s). The goal was to produce quality products at lower cost. Lean manufacturing emphasizes removing unnecessary steps from the production process. It consists of five basic elements: pull systems, continuous improvement, just-in-time, kaizen (continuous change), and 5S. Pull systems are able to produce exactly what the customer requires without extra work. Continuous improvement means continuously improving on existing processes. Just-intime refers the time components and materials arrive at the exact place where they are needed. Kaizen is continuous improvement. This can be achieved by making small, incremental changes every day. Five-S stands for sort. It is also the acronym for shine, standardize (standardize), and sustain. These five elements are combined to give you the best possible results.
The Lean Production System
Six key concepts form the foundation of the lean production system:
-
Flow - focuses on moving information and materials as close to customers as possible.
-
Value stream mapping is the ability to divide a process into smaller tasks, and then create a flowchart that shows the entire process.
-
Five S's - Sort, Set In Order, Shine, Standardize, and Sustain;
-
Kanban: Use visual signals such stickers, colored tape, or any other visual cues, to keep track your inventory.
-
Theory of constraints - identify bottlenecks in the process and eliminate them using lean tools like kanban boards;
-
Just-in time - Get components and materials delivered right at the point of usage;
-
Continuous improvement - Make incremental improvements rather than overhauling the entire process.