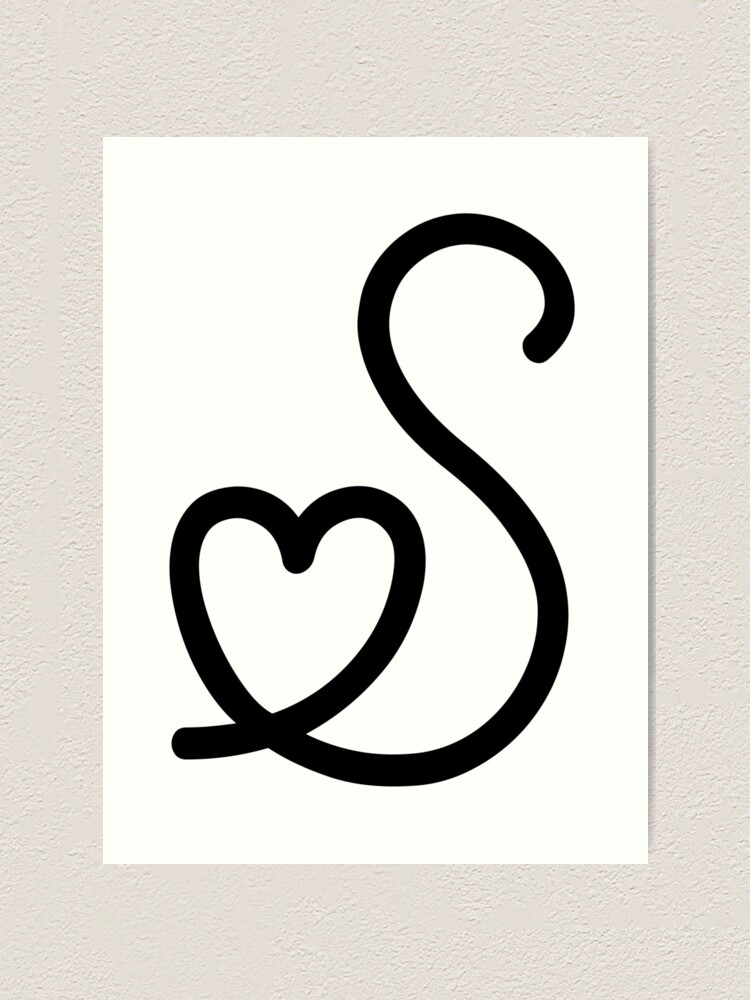
Program management refers to the process of managing multiple projects simultaneously. It requires a clear definition of the goals and timelines for the projects, so that everyone involved knows their roles and responsibilities. This ensures that projects are completed on time. More information about program management can be found here. This article will discuss program management's goals, process, as well as the tools and methods used.
Multitasking is possible
Multitasking is difficult. These are some tips that can help you plan intelligently and efficiently switch between projects. Be honest with your clients and teammates. This will help you prevent the mismatch of resources and expectations. It is important to have good organizational skills. Keep separate activity logs for each project. Also, assign tasks to your team members and give them deadlines.
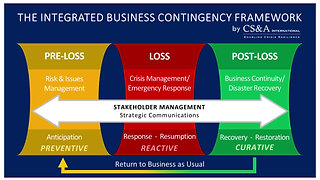
Multi-project management requires more organizational and attention to detail than managing just one project. This requires excellent communication skills. A strong project management program will help you avoid making mistakes and keep strong business relationships.
Goals of program management
Program management aims to help organizations achieve their strategy by translating it into concrete goals and minimizing the risk. The program manager sets objectives, measures progress, and communicates them to all levels of an organization. The goals of the program should align with the metrics. These objectives define the purpose of the projects.
The OGC’s Best Practice Guide discusses the goals and methods of program management. Initial steps include confirming business need, securing support from stakeholders, setting up project management arrangements and defining the project scope and goals.
The process of program management
Program management determines the success of projects. A project is a product or service that provides a specific capability, while a programme provides multiple capabilities. A program's outcomes can be measured and verified. Programm management also includes allocating resources.
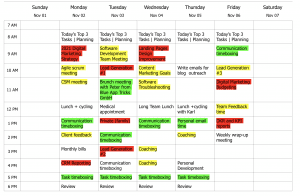
You can break down the program management process into five distinct stages. Each stage focuses specifically on a different aspect. Each stage requires a different set of activities to reach the desired outcome.
FAQ
What is Six Sigma?
It's a method for quality improvement that focuses on customer service as well as continuous learning. It is a method that eliminates defects using statistical techniques.
Motorola's 1986 efforts to improve manufacturing process efficiency led to the creation of Six Sigma.
This idea quickly spread throughout the industry. Today, many organizations use six sigma methods for product design, production and delivery.
What are the 4 main functions of management?
Management is responsible for organizing, managing, directing and controlling people, resources, and other activities. It includes creating policies and procedures, as well setting goals.
Management assists an organization in achieving its goals by providing direction, coordination and control, leadership, motivation, supervision and training, as well as evaluation.
The following are the four core functions of management
Planning - This is the process of deciding what should be done.
Organizing: Organizing refers to deciding how things should work.
Directing - Directing means getting people to follow instructions.
Controlling: Controlling refers to making sure that people do what they are supposed to.
What are the steps of the management decision-making process?
The decision-making process of managers is complicated and multifaceted. It involves many factors, such as analysis and strategy, planning, execution, measurement, evaluation, feedback etc.
The key thing to remember when managing people is that they are human beings just as you are and therefore make mistakes. There is always room to improve, especially if your first priority is to yourself.
We explain in this video how the Management decision-making process works. We discuss different types of decisions as well as why they are important and how managers can navigate them. You'll learn about the following topics:
Statistics
- Your choice in Step 5 may very likely be the same or similar to the alternative you placed at the top of your list at the end of Step 4. (umassd.edu)
- Hire the top business lawyers and save up to 60% on legal fees (upcounsel.com)
- UpCounsel accepts only the top 5 percent of lawyers on its site. (upcounsel.com)
- This field is expected to grow about 7% by 2028, a bit faster than the national average for job growth. (wgu.edu)
- The profession is expected to grow 7% by 2028, a bit faster than the national average. (wgu.edu)
External Links
How To
How can you use the Kaizen method?
Kaizen means continuous improvement. This term was first used by Toyota Motor Corporation in the 1950s. It refers to the Japanese philosophy that emphasizes continuous improvement through small incremental changes. It's where people work together in order to improve their processes constantly.
Kaizen is one the most important methods of Lean Manufacturing. The concept involves employees responsible for manufacturing identifying problems and trying to fix them before they become serious issues. This increases the quality of products and reduces the cost.
The main idea behind kaizen is to make every worker aware of what happens around him/her. Correct any errors immediately to avoid future problems. If someone spots a problem while at work, they should immediately report it to their manager.
There are some basic principles that we follow when doing kaizen. The end product is always our starting point and we work toward the beginning. In order to improve our factory's production, we must first fix the machines producing the final product. First, we fix machines that produce components. Next, we fix machines that produce raw material. Finally, we repair the workers who are directly involved with these machines.
This method, called 'kaizen', focuses on improving each and every step of the process. After we're done with the factory, it's time to go back and fix the problem.
You need to know how to measure the effectiveness of kaizen within your business. There are many ways to tell if kaizen is effective. Another way to determine if kaizen is working well is to look at the quality of the products. Another way is determining how much productivity increased after implementing kaizen.
To determine if kaizen is effective, you should ask yourself why you chose to implement kaizen. Is it because the law required it or because you want to save money. Did you really believe it would lead to success?
Congratulations if you answered "yes" to any of the questions. You are ready to start kaizen.