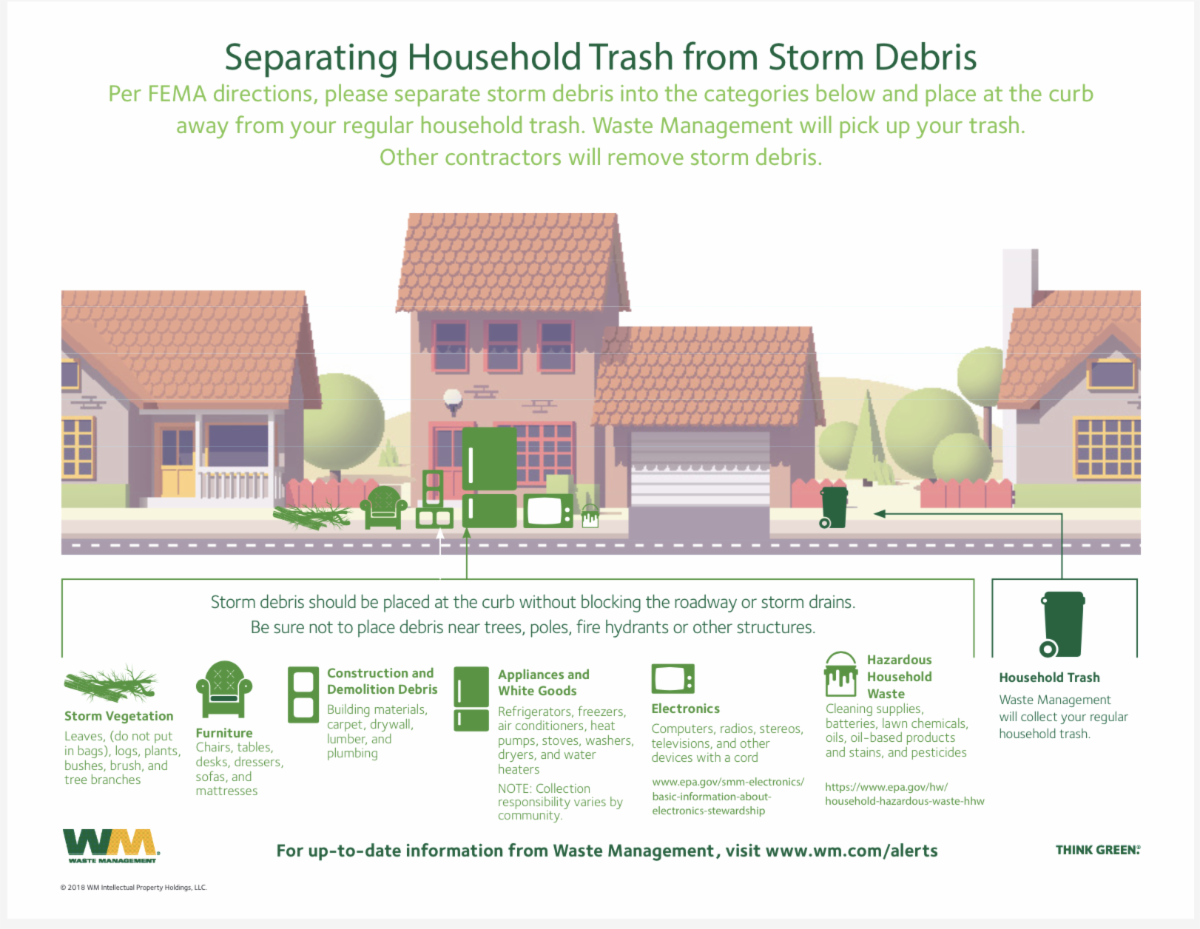
Negative return
Negative return and downside risk are two terms that are sometimes used to describe the same thing. They are basically the same thing. If an investment doesn’t make any money within a set time period, there’s a good chance that it will lose money. Exumor Chanels Inc. might lose 6% if it falls apart.
The study, which is based on high-frequency data and shows that negative return effects are more severe in emerging markets then in developed ones. This doesn't mean that the downside risk in every market is less important. Rather, the study shows that negative returns and downside risks are more of a concern in emerging markets, which is why negative return and downside risk expectations should be evaluated carefully before investing in any type of investment.
Capital loss
A downside risk refers to a risk that a security may lose its value. This risk can be infinite or finite. Roy was the first to study this risk. His theory helped model possible losses in securities. It is crucial to assess the potential risk associated with a security before you decide whether it is worth buying.
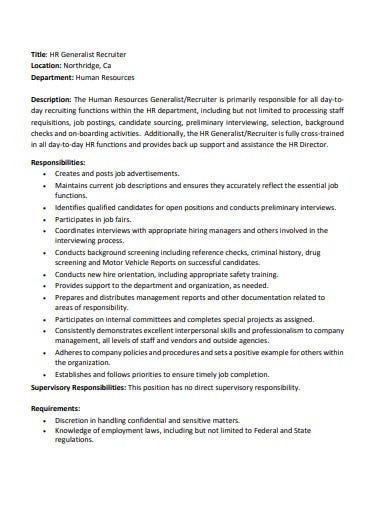
There are many ways to manage a downside risk. Diversification and tactical asset allocation are three of the most common ways to reduce downside risk. These strategies should be tailored to an investor's risk tolerance and time horizon. They must also be consistent with the cost involved.
Inflation
Inflation may drop for the first and only time in more than a decade. The Federal Reserve is unlikely to raise interest rates as high as market expectations. It has only raised interest rate once this year. In fact, communication from the Fed about future hikes has already caused mortgage yields and Treasury yields both to rise. If the Fed raises rates, it will likely do so slowly to keep inflation in check.
The downside to inflation is the possibility of consumer spending being cut, which could be detrimental to economic growth. Consumers may have less money to spend fun items if their everyday staples cost rise. This could cause the economy to slow down, and the stock market to suffer.
Volatility
In investing, volatility and downside risks are important concepts. When investing, one wants the downside risk to be minimized while maximizing the upside risk. The volatility of the market simply means that a security's risk level is measured. This is commonly referred to by the term "the risk of losing your money". Volatility refers to the degree of risk that an investment has before it is fully realised.
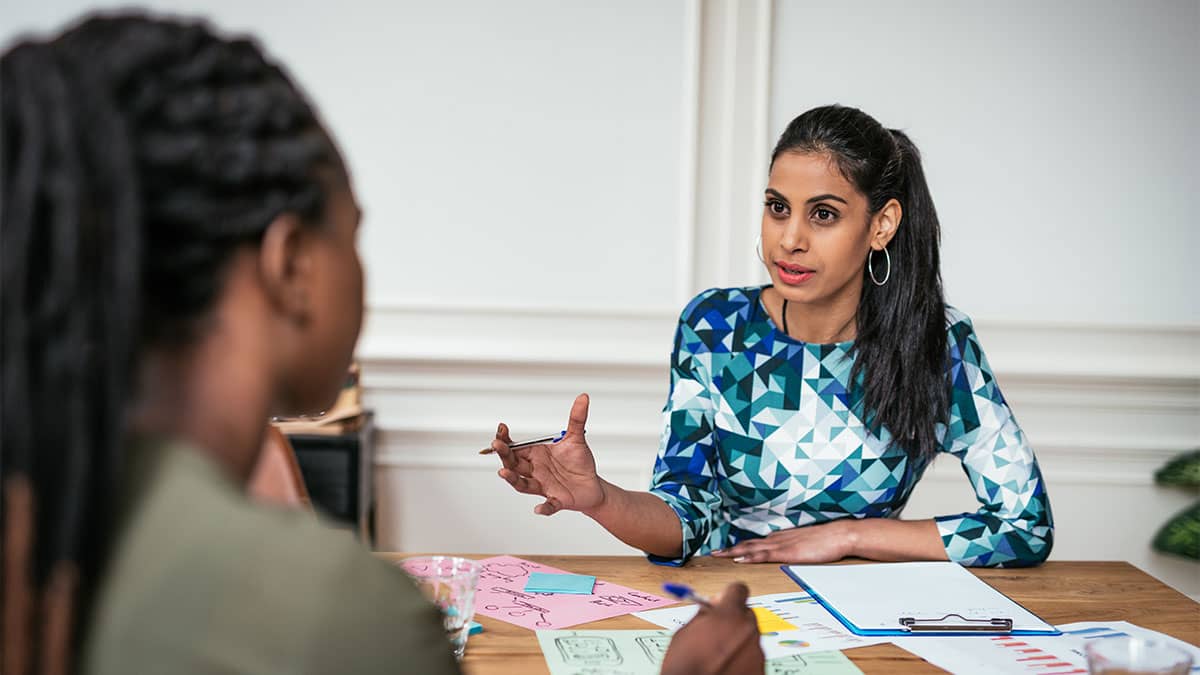
Downside risk is the risk that an investor might lose money in an investment if the value goes down. This risk can easily be calculated in several ways. The most common is by comparing the upside potential of a security to its downside risk. Upside potential is the chance that the value of a security will increase over time.
Liquidity
There are two types of risks to consider when trading. Market liquidity risk is the first. This risk is caused by market withdrawals. The downside risk is another type. While an asset's price may drop to zero, it could also rise above its listing price when the market recovers. Both of these risks can negatively impact your profits and losses.
Funding liquidity risk is a risk that a firm may not be able to meet its future cash flow requirements, or its current cash needs. This risk can materially impact the operation of a firm. This is especially true for financial institutions. This risk can be addressed by implementing debt maturity transition.
FAQ
What are the main styles of management?
There are three main management styles: participative, laissez-faire and authoritarian. Each style is unique and has its strengths as well as weaknesses. Which style do YOU prefer? Why?
Autoritarian - The leader sets direction and expects everyone else to follow it. This style works best in large organizations that are stable and well-organized.
Laissez-faire - The leader allows each individual to decide for him/herself. This style is best when the organization has a small but dynamic group.
Participative - The leader listens to ideas and suggestions from everyone. This is a great style for smaller organizations that value everyone.
How can we create a successful company culture?
A culture of respect and value within a company is key to a productive culture.
It's based on three main principles:
-
Everybody can contribute something valuable
-
Fair treatment of people is the goal
-
There is mutual respect between individuals and groups
These values reflect in how people behave. They will treat others with respect and kindness.
They will respect other people's opinions.
They can also be a source of inspiration for others.
Additionally, the company culture encourages open communication as well as collaboration.
People feel free to express their views openly without fear of reprisal.
They know that they will not be judged if they make mistakes, as long as the matter is dealt with honestly.
Finally, the company culture promotes integrity and honesty.
Everyone is aware that truth must be told.
Everyone understands that there are rules and regulations which apply to them.
No one is entitled to any special treatment or favors.
Why is it so important for companies that they use project management techniques
Project management techniques are used in order to ensure projects run smoothly, and that deadlines are met.
This is because many businesses depend heavily upon project work to produce products and services.
These projects are essential for companies.
Companies could lose their time, reputation, and money without effective project management.
What does the term "project management” mean?
Management is the act of managing activities in order to complete a project.
We include defining the scope of the project, identifying the requirements, preparing the budget, organizing the project team, scheduling the work, monitoring progress, evaluating results, and closing down the project.
What is Six Sigma?
This is a method of quality improvement that emphasizes customer service, continuous learning, and customer service. It is a method that eliminates defects using statistical techniques.
Motorola's 1986 efforts to improve manufacturing process efficiency led to the creation of Six Sigma.
This idea quickly spread throughout the industry. Today, many organizations use six sigma methods for product design, production and delivery.
Statistics
- As of 2020, personal bankers or tellers make an average of $32,620 per year, according to the BLS. (wgu.edu)
- The BLS says that financial services jobs like banking are expected to grow 4% by 2030, about as fast as the national average. (wgu.edu)
- The average salary for financial advisors in 2021 is around $60,000 per year, with the top 10% of the profession making more than $111,000 per year. (wgu.edu)
- 100% of the courses are offered online, and no campus visits are required — a big time-saver for you. (online.uc.edu)
- This field is expected to grow about 7% by 2028, a bit faster than the national average for job growth. (wgu.edu)
External Links
How To
How can Lean Manufacturing be done?
Lean Manufacturing is a method to reduce waste and increase efficiency using structured methods. They were developed by Toyota Motor Corporation in Japan during the 1980s. The primary goal was to make products with lower costs and maintain high quality. Lean manufacturing seeks to eliminate unnecessary steps and activities in the production process. It includes five main elements: pull systems (continuous improvement), continuous improvement (just-in-time), kaizen (5S), and continuous change (continuous changes). Pull systems involve producing only what the customer wants without any extra work. Continuous improvement is the continuous improvement of existing processes. Just-in-time is when components and other materials are delivered at their destination in a timely manner. Kaizen means continuous improvement, which is achieved by implementing small changes continuously. Five-S stands for sort. It is also the acronym for shine, standardize (standardize), and sustain. These five elements are used together to ensure the best possible results.
Lean Production System
Six key concepts underlie the lean production system.
-
Flow is about moving material and information as near as customers can.
-
Value stream mapping is the ability to divide a process into smaller tasks, and then create a flowchart that shows the entire process.
-
Five S's, Sort, Set in Order, Shine. Standardize. and Sustain.
-
Kanban is a visual system that uses visual cues like stickers, colored tape or stickers to keep track and monitor inventory.
-
Theory of constraints - identify bottlenecks during the process and eliminate them with lean tools like Kanban boards.
-
Just-in-time delivery - Deliver components and materials right to your point of use.
-
Continuous improvement is making incremental improvements to your process, rather than trying to overhaul it all at once.