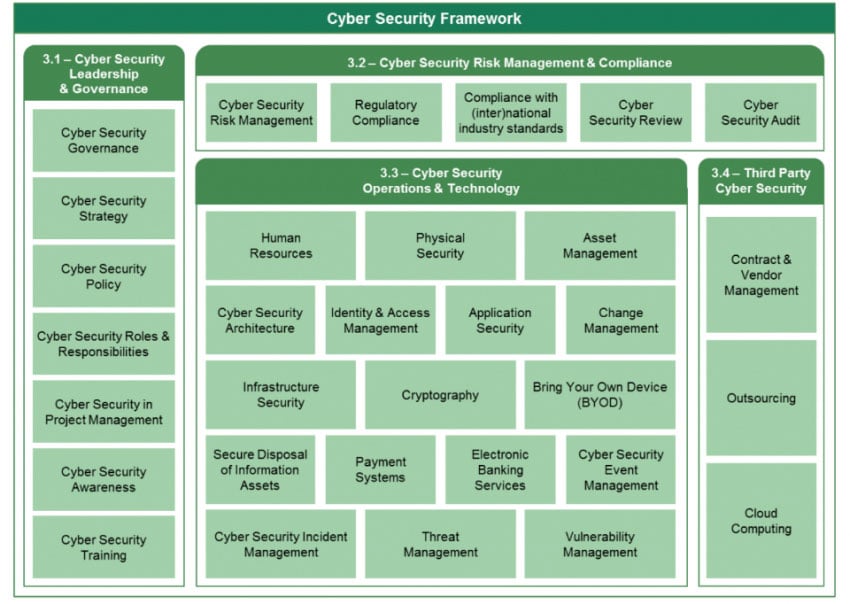
Management of change (MOC), is a concept that many people don't know about. This best practice is a great way to avoid unintended consequences and keep your organization running smoothly. Read on for more information about MOC and its stages. These are the eight key MOC stages. You'll be able successfully manage changes in your company if you follow these steps. So what exactly is MOC, you ask? Why is it important?
MOC refers to a process
MOC is often overlooked within organizations. Changes are a common source of workplace accidents due to unfamiliarity and a lack of process safety information. Organizations tend to rush to implement changes in order to move on, often neglecting the importance of risk management. Accidents can occur if they don't redesign their production processes. This is especially true when dealing with hazardous substances or energy.
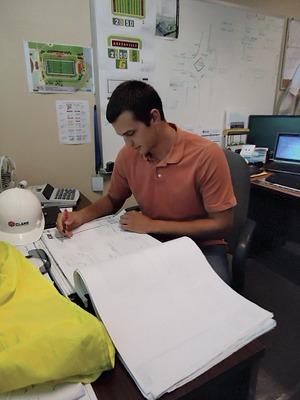
It consists in eight stages
McKinsey’s Change Management Model describes the change process in eight stages. These include preparation, implementation and monitoring. Evaluation, evaluation, sustainability. The first three stages focus on the business side of change, while the last two deal with the emotional aspects. Culture must be considered in the eighth stage. It is important to incorporate new practices into existing work cultures. To ensure that successful change management is possible, the organization's culture should be able adapt to the changes.
It helps avoid unintended consequences
Unintended consequences are caused by people who don't always reflect on their actions before making a choice. People might decide to base their decisions on past performance and not the current situation. Unintended consequences may result, which can be harmful and counterproductive. There are methods to manage change and reduce unintended consequences. One example is implementing a new process that may have positive or negative unintended consequences. For example, if a new technology is introduced, a test group will be established to assess its impact.
It is a great practice
A successful management of change can open up new possibilities for your organization. This best practice can be used to help create an organizational shift. It's important to remember that there are soft elements involved in change management as well, so it's important to take these into consideration. These elements are crucial to any change management project's success. These are important to ensure that the change process is as smooth and seamless as possible.
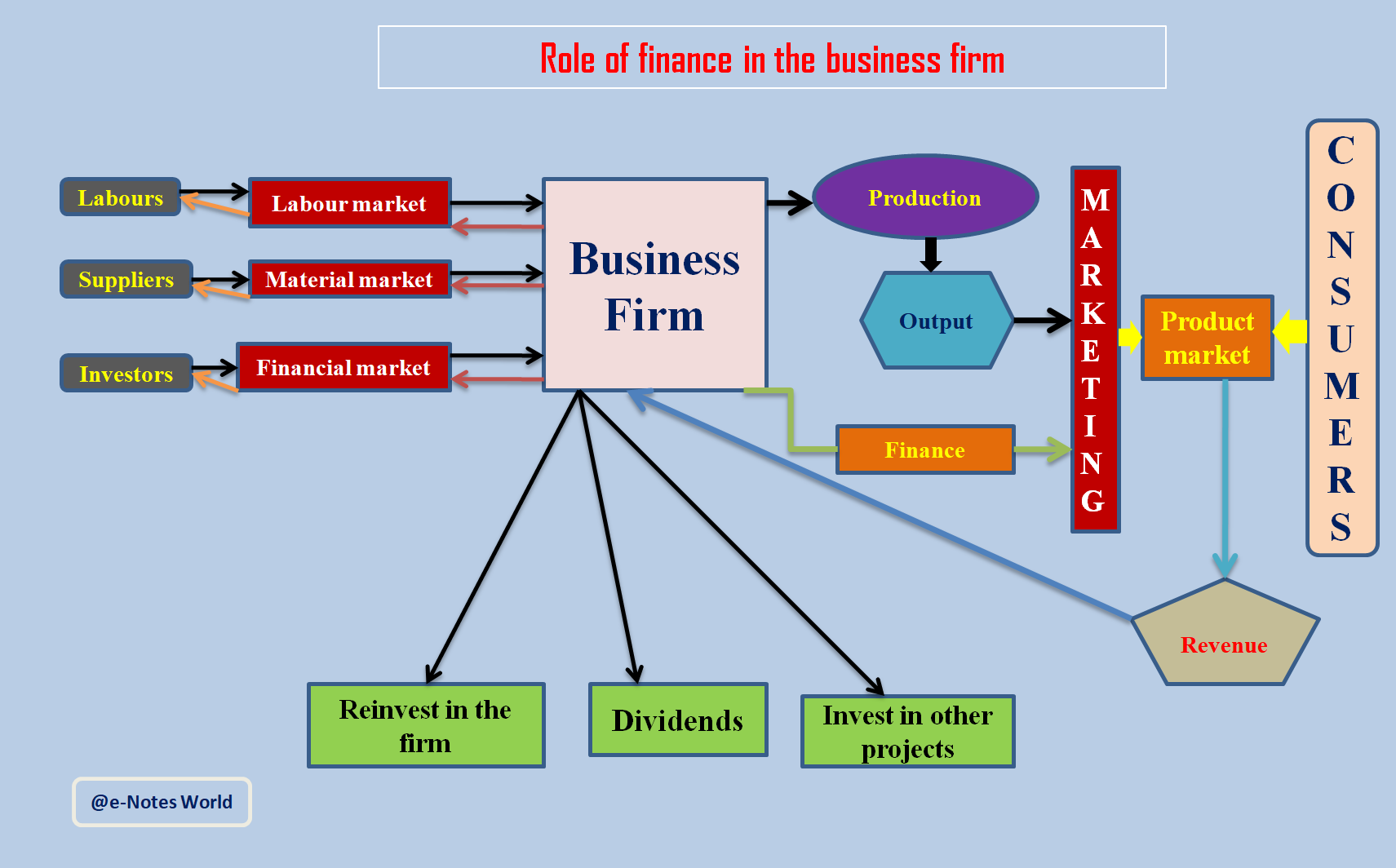
It is essential to maintaining regulatory compliance
Organizations must keep track of metrics and report on their processes in order to comply with regulatory requirements. These metrics are used to measure process adherence, and to identify risk/performance indicators. Metrics are also useful in identifying regulatory changes and their effect on an organisation. Organizations that monitor change can be proactive in anticipating future regulations and demonstrating compliance. This article will cover some of the critical metrics that must monitored and reported.
FAQ
What are the main management skills?
Any business owner needs to be able to manage people, finances, resources and time. They are the ability to manage people and finances, space, money, and other factors.
Managerial skills are required when setting goals and objectives and planning strategies, leading employees, motivating them, solving problems, creating policies, procedures, or managing change.
As you can see, there are many managerial responsibilities!
What is Six Sigma and how can it help you?
This is a method of quality improvement that emphasizes customer service, continuous learning, and customer service. This is an approach to quality improvement that uses statistical techniques to eliminate defects.
Motorola developed Six Sigma in 1986 to help improve its manufacturing processes.
The idea spread quickly in the industry. Today many organizations use six-sigma techniques to improve product design.
What are the 4 major functions of management
Management is responsible for planning, organizing, directing, and controlling people and resources. It includes creating policies and procedures, as well setting goals.
Management aids an organization in reaching its goals by providing direction and coordination, control, leadership motivation, supervision, training, evaluation, and leadership.
The four main functions of management are:
Planning – Planning involves deciding what needs to happen.
Organizing - Organizing involves deciding how things should be done.
Directing - Directing means getting people to follow instructions.
Controlling – This refers to ensuring that tasks are carried out according to plan.
What can a manager do to improve his/her management skillset?
Through demonstrating good management skills at every opportunity
Managers must continuously monitor the performance levels of their subordinates.
You must act quickly if you notice that your subordinate isn’t performing to their standards.
You should be able pinpoint what needs to improve and how to fix it.
Statistics
- As of 2020, personal bankers or tellers make an average of $32,620 per year, according to the BLS. (wgu.edu)
- This field is expected to grow about 7% by 2028, a bit faster than the national average for job growth. (wgu.edu)
- Hire the top business lawyers and save up to 60% on legal fees (upcounsel.com)
- 100% of the courses are offered online, and no campus visits are required — a big time-saver for you. (online.uc.edu)
- UpCounsel accepts only the top 5 percent of lawyers on its site. (upcounsel.com)
External Links
How To
How do you apply the Kaizen method to your life?
Kaizen means continuous improvement. This Japanese term refers to the Japanese philosophy of continuous improvement that emphasizes incremental improvements and constant improvement. This is a collaborative process in which people work together to improve their processes continually.
Kaizen is one method that Lean Manufacturing uses to its greatest advantage. The concept involves employees responsible for manufacturing identifying problems and trying to fix them before they become serious issues. This will increase the quality and decrease the cost of the products.
Kaizen is an approach to making every worker aware and alert to what is happening around them. If something is wrong, it should be corrected immediately so that no problem occurs. It is important that employees report any problems they see while on the job to their managers.
Kaizen is based on a few principles. We always start from the end product and move toward the beginning. For example, if we want to improve our factory, we first fix the machines that produce the final product. Then, we fix the machines that produce components and then the ones that produce raw materials. And finally, we fix the workers who work directly with those machines.
This method, called 'kaizen', focuses on improving each and every step of the process. Once we have finished fixing the factory, we return to the beginning and work until perfection.
You need to know how to measure the effectiveness of kaizen within your business. There are many methods to assess if kaizen works well. One way is to examine the amount of defects on the final products. Another way is to see how much productivity has increased since implementing kaizen.
To determine if kaizen is effective, you should ask yourself why you chose to implement kaizen. You were trying to save money or obey the law? Did you really believe that it would be a success factor?
Congratulations! You're ready to start kaizen.