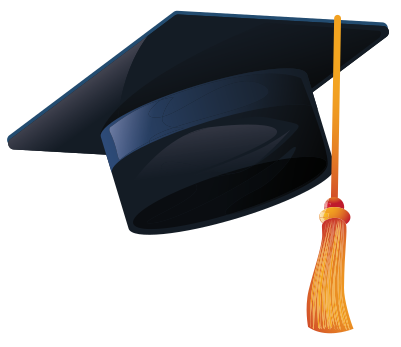
The management of supply chain risk involves various risks. These risks are related to either the demand for a particular product or the supply chain of raw materials. Demand risks can occur when a business underestimates demand for a product. While supply risks can arise when raw material do not arrive on a timely basis. These two risks can impact the product's flow. The supply chain can also be affected by environmental risks, which may result from political, social and environmental issues.
Cybersecurity is a key component of supply chain risk management
Supply chain risk management is about cybersecurity measures to avoid cyber attacks on critical assets. These measures could include the development of a cybersecurity strategy and the establishment of supplier controls. Businesses should also create contracts that outline their security requirements. These contracts should outline what they are expected to do to protect your assets. To ensure sensitive information isn't misused, a supplier should not be able to meet these requirements.
Cyber threats will become increasingly complex as supply chains become more complex. This means that it is essential to carefully assess and mitigate these risks. Cyber threats may occur at any part of the supply chain. The impact they have on a company’s financial and brand reputation, as well as its operational health, can be severe. Cybersecurity issues must be addressed at every step of the supply chains.
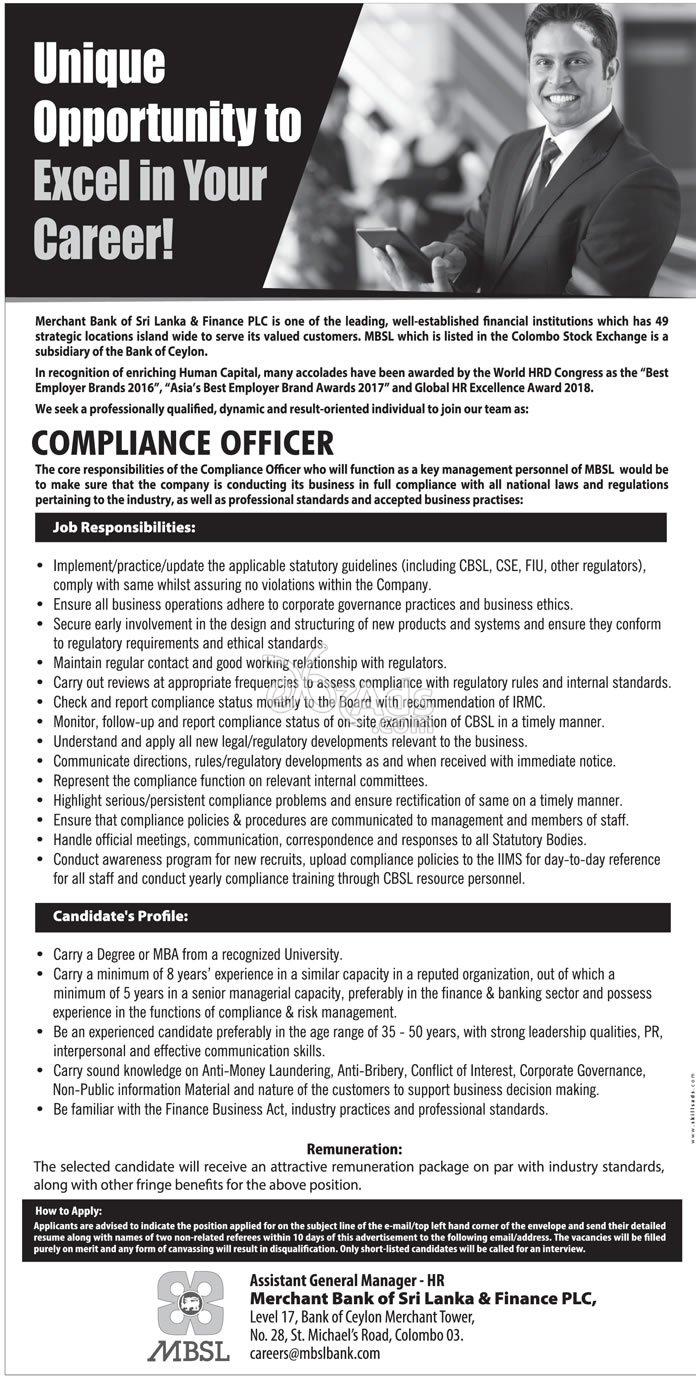
It requires a cross-functional team
Supply chain risk management requires a cross-functional team in order to manage the risks that are associated with the entire supply chains. This strategy should include preparation, response, and recovery. Preparation involves identifying high-risk regions and creating contingency programs to deal with them. The plan should prioritize risk according to their likelihood and severity. Visibility is an essential component of a supply-chain risk management strategy.
Although supply chain risk management is vital, executives have not been able to tackle it effectively. Surveying 639 executives across multiple industries and regions, 71% said that their companies were more susceptible to supply chain disruptions now than two years ago. 72 percent also predicted that the risks will continue to rise. While the government has set up several agencies to address supply chain risk, the private sector is still seeking a proven methodology that will help minimize business disruption.
Supply chain boards that work effectively review and mitigate the risks of the supply chain are efficient. During the review, each participant takes ownership of the mitigation action. One example is a procurement representative who determines the qualifications and onboarding of a new supplier.
Technology is required
As organizations strive to reduce costs, increase resilience, many are rethinking their supply chain risk management strategies. They are turning towards technology to increase visibility and control risks. Companies can create stronger global networks and resilient supply chains with the right technology. To fully reap the benefits of technology, businesses need access to accurate data and visibility platforms. Companies without this information will be forced to deal with supply chain risks reactively.
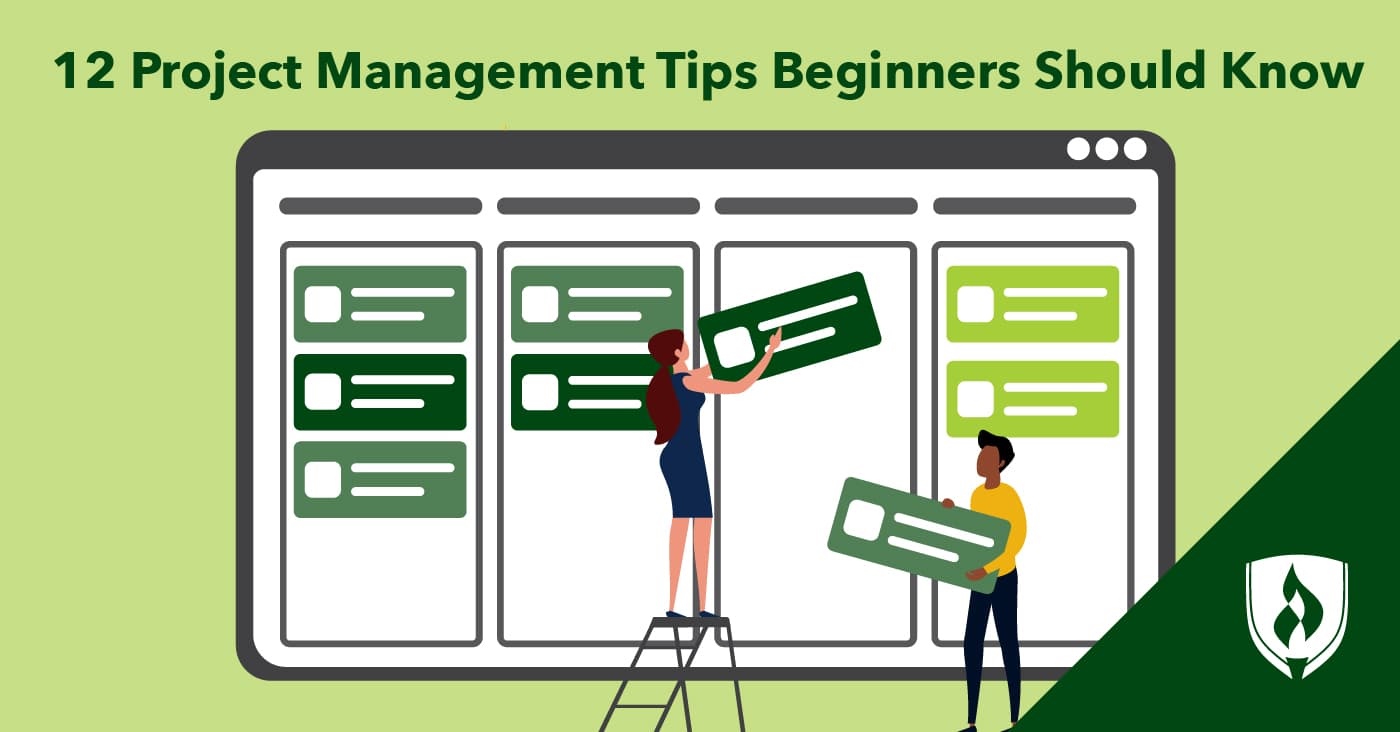
Supply chain management is a multifaceted and complex topic. Recent research of 639 industry executives revealed that 71% believed that their supply chains are more susceptible to disruption than they were in the past, and that this risk is expected to rise. The United States government launched several agencies to address supply-chain risk. This includes the Protecting Critical Technology Task Force of the Department of Defense. Private companies are looking for proven ways to minimize the effects of supply chain risks on business.
FAQ
What does Six Sigma mean?
Six Sigma uses statistical analysis to find problems, measure them, analyze root causes, correct problems, and learn from experience.
The first step is to identify the problem.
Next, data is collected and analyzed to identify trends and patterns.
The problem is then rectified.
Finally, data is reanalyzed to determine whether the problem has been eliminated.
This continues until the problem has been solved.
What are the four main functions of management?
Management is responsible of planning, organizing, leading, and controlling people as well as resources. It also includes developing policies and procedures and setting goals.
Management is the ability to direct, coordinate, control, motivate, supervise, train, and evaluate an organization's efforts towards achieving its goals.
Management has four primary functions:
Planning - Planning involves determining what needs to be done.
Organizing - Organizing involves deciding how things should be done.
Directing - Directing means getting people to follow instructions.
Controlling - Controlling means ensuring that people carry out tasks according to plan.
Why does it sometimes seem so hard to make good business decisions
Businesses are complex systems, and they have many moving parts. It is difficult for people in charge of businesses to manage multiple priorities simultaneously and also deal with uncertainty.
Understanding the impact of these factors on the system is crucial to making sound decisions.
It is important to consider the functions and reasons for each part of the system. You then need to consider how those individual pieces interact with each other.
You need to ask yourself if your previous actions have led you to make unfounded assumptions. You might consider revisiting them if they are not.
For help, ask someone else if you're still stumped after all the above. You may be able to see things from a different perspective than you are and gain insight that can help you find a solution.
What kind of people use Six Sigma
Six Sigma is well-known to those who have worked in operations research and statistics. Anybody involved in any aspect or business can benefit.
It requires high levels of commitment and leadership skills to be successful.
What are the steps that management takes to reach a decision?
The decision-making process of managers is complicated and multifaceted. This involves many factors including analysis, strategy and planning, implementation, measurement and evaluation, feedback, feedback, and others.
When managing people, the most important thing to remember is that they are just human beings like you and make mistakes. As such, there is always room for improvement, especially if you're willing to put forth the effort to improve yourself first.
This video explains the process of decision-making in Management. We discuss different types of decisions as well as why they are important and how managers can navigate them. You'll learn about the following topics:
Statistics
- Your choice in Step 5 may very likely be the same or similar to the alternative you placed at the top of your list at the end of Step 4. (umassd.edu)
- The profession is expected to grow 7% by 2028, a bit faster than the national average. (wgu.edu)
- The average salary for financial advisors in 2021 is around $60,000 per year, with the top 10% of the profession making more than $111,000 per year. (wgu.edu)
- The BLS says that financial services jobs like banking are expected to grow 4% by 2030, about as fast as the national average. (wgu.edu)
- As of 2020, personal bankers or tellers make an average of $32,620 per year, according to the BLS. (wgu.edu)
External Links
How To
How do you apply the Kaizen method to your life?
Kaizen means continuous improvement. The Japanese philosophy emphasizes small, incremental improvements to achieve continuous improvement. This term was created by Toyota Motor Corporation in 1950. It is a process where people come together to improve their processes.
Kaizen is one the most important methods of Lean Manufacturing. In this concept, employees who are responsible for the production line must identify problems that exist during the manufacturing process and try to solve them before they become big issues. This improves the quality of products, while reducing the cost.
Kaizen is an approach to making every worker aware and alert to what is happening around them. So that there is no problem, you should immediately correct it if something goes wrong. So, if someone notices a problem while working, he/she should report it to his/her manager.
Kaizen has a set of basic principles that we all follow. Start with the end product, and then move to the beginning. For example, if we want to improve our factory, we first fix the machines that produce the final product. Next, we repair the machines that make components. Then, the machines that make raw materials. And finally, we fix the workers who work directly with those machines.
This method, called 'kaizen', focuses on improving each and every step of the process. After we're done with the factory, it's time to go back and fix the problem.
It is important to understand how to measure the effectiveness and implementation of kaizen in your company. There are many ways you can determine if kaizen has been implemented well. One way is to examine the amount of defects on the final products. Another way to find out how productive your company has been since you implemented kaizen is to measure the increase in productivity.
If you want to find out if your kaizen is actually working, ask yourself why. Did you do it because it was legal or to save money? Did you really believe that it would be a success factor?
Congratulations if you answered "yes" to any of the questions. You are ready to start kaizen.