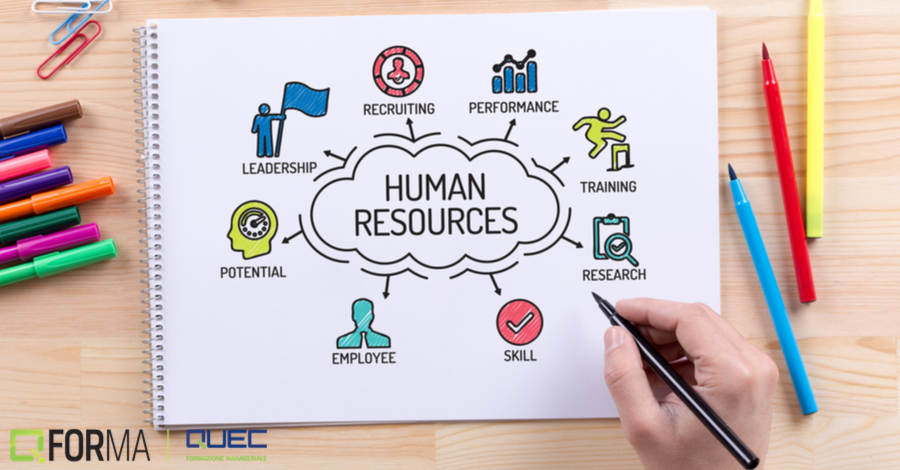
A RAID log is a valuable tool to manage your project. It can help you to identify risks and understand what your assumptions are. It can also help to manage issues and improve your projects.
RAID logs can be used to communicate between project managers with stakeholders. It is a record of decisions made and activities performed during the project. This allows project managers and teams to keep track, make consistent decisions, and keep their team informed. RAID logs can also be used as a reference document. A RAID log allows you to keep track of the progress of your projects, learn from past mistakes and make improvements for your next project.
RAID logs enable project managers identify risks and to assess their impact before making a decision on the course of action. You can use them to prevent potential problems from arising, or to aid you in understanding the implications of any issues. This is an important step to take before your project begins, and should be done early on.
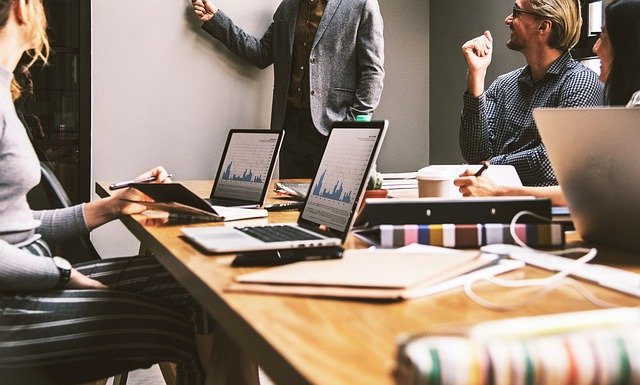
Projects have risks. They can be one of the most challenging aspects of a project. If you fail to take appropriate actions, you could end up with poor delivery and a failed project. You must identify potential risks early in the project to create a plan to minimize them.
Most risks can be divided into High Impact items (which have a very low impact on projects) and Low Impact, which has a significantly negative effect on them. The best way of assessing the risk of an item is to measure its likelihood and severity. Both factors can be reduced to increase the chance of a risk being addressed. Any increase in either factor can lead to a greater risk. It is vital to constantly monitor the severity of these risks.
Another major component of projects are assumptions. Although you might not have any reason to assume something, it is best to document them. There are many ways you can record assumptions. However, the RAID Log is a great place to begin. While some Program/Program Managers prefer that they are the only authors of their RAID logs, others prefer to use other tools like an issues log. While it is important for you to record your assumptions in writing they are often more useful for long-term projects.
RAID logs are an important tool to assess risks. It should be maintained up-to-date during the entire project. It is also useful as a reference document. This is crucial for audits and status reporting. RAID logs should be regularly updated with new issues and risks as they occur, or details about any existing issues. It's also a great way for your team to keep track.
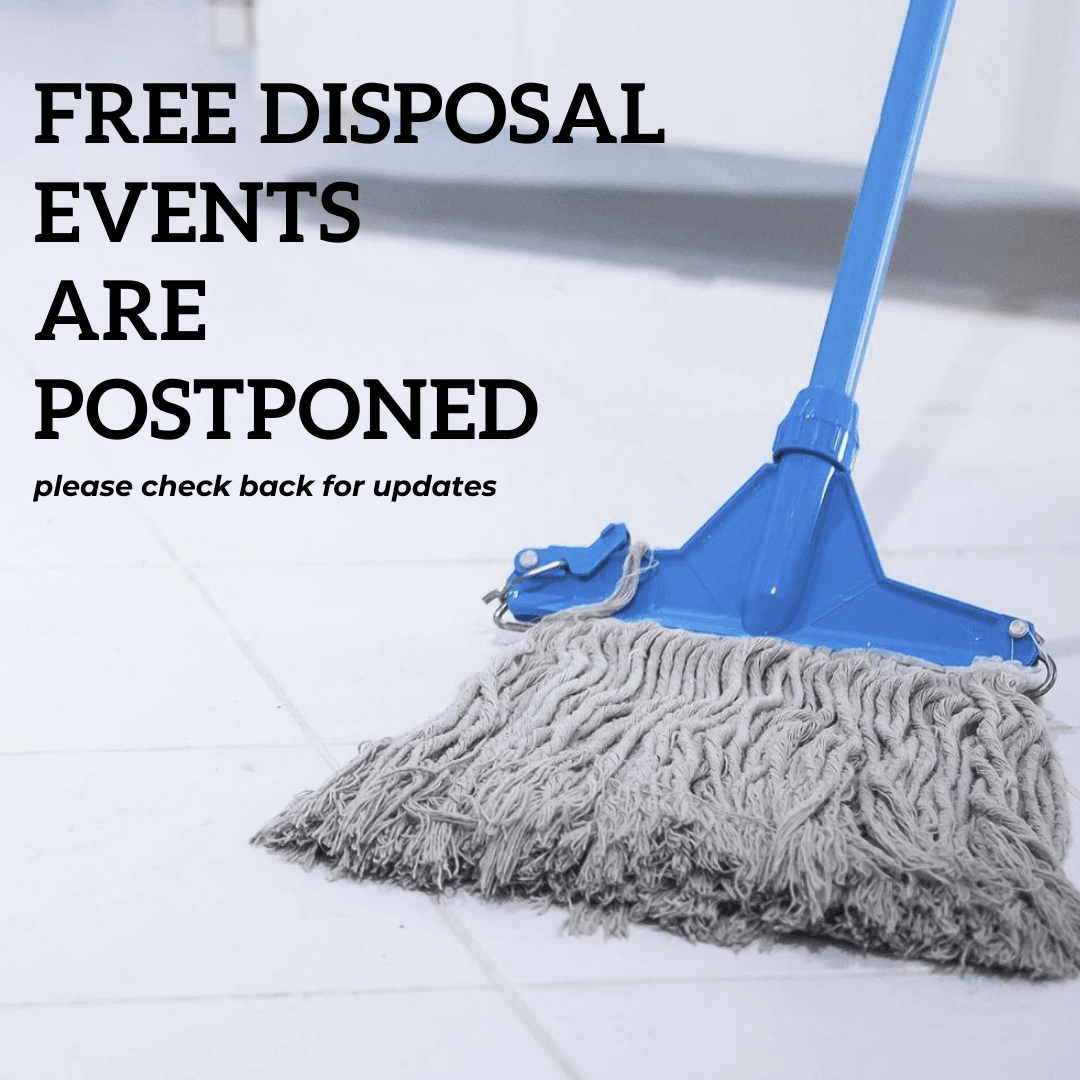
A RAID log is useful for project managers, especially in the early stages of the project. It will help you stay organized and have all the necessary information at one place. It can also be used to gather data, track assumptions, and communicate project issues to stakeholders.
FAQ
What is the difference of leadership and management?
Leadership is about being a leader. Management is about controlling others.
Leaders inspire others, managers direct them.
Leaders motivate people to succeed; managers keep workers on track.
A leader develops people; a manager manages people.
How do you define Six Sigma?
Six-sigma will be well-known to anyone who has worked in operations research or statistics. Anyone involved in business can benefit.
This requires a lot of dedication, so only people with great leadership skills can make the effort to implement it.
Six Sigma is so well-known.
Six Sigma is easy to use and can lead to significant improvements. It can also be used to help companies identify and focus on the most important aspects of their business.
What does it mean to say "project management"
Management is the act of managing activities in order to complete a project.
This includes defining the scope, identifying the requirements and preparing the budget. We also organize the project team, schedule the work, monitor progress, evaluate results, and close the project.
What are the five management steps?
Each business has five stages: planning, execution and monitoring.
Planning is about setting goals for your future. It includes defining what you want to achieve and how you plan to do it.
Execution occurs when you actually carry out the plans. These plans must be adhered to by everyone.
Monitoring is the act of monitoring your progress towards achieving your targets. This should involve regular reviews of performance against targets and budgets.
Every year, there are reviews. They give you an opportunity to review the year and assess how it went. If not then, you can make changes to improve your performance next year.
After each year's review, evaluation occurs. It helps identify what worked well and what didn't. It also provides feedback regarding how people performed.
How to effectively manage employees
Effectively managing employees means making sure they are productive and happy.
This also involves setting clear expectations and monitoring their performance.
Managers need clear goals to be able to accomplish this.
They should communicate clearly to staff members. They should also ensure that they both reward high performers and discipline those who are not performing to their standards.
They should also keep records of all activities within their team. These include:
-
What was accomplished?
-
How much work was put in?
-
Who did it, anyway?
-
Was it done?
-
Why did it happen?
This information can be used to monitor performance and evaluate results.
Why is project management important for companies?
To ensure projects run smoothly and meet deadlines, project management techniques are employed.
This is due to the fact that most businesses rely heavily upon project work in order to produce goods, and services.
Companies need to manage these projects efficiently and effectively.
Without effective project management, companies may lose money, time, and reputation.
Statistics
- The average salary for financial advisors in 2021 is around $60,000 per year, with the top 10% of the profession making more than $111,000 per year. (wgu.edu)
- Your choice in Step 5 may very likely be the same or similar to the alternative you placed at the top of your list at the end of Step 4. (umassd.edu)
- Our program is 100% engineered for your success. (online.uc.edu)
- This field is expected to grow about 7% by 2028, a bit faster than the national average for job growth. (wgu.edu)
- 100% of the courses are offered online, and no campus visits are required — a big time-saver for you. (online.uc.edu)
External Links
How To
How can Lean Manufacturing be done?
Lean Manufacturing uses structured methods to reduce waste, increase efficiency and reduce waste. They were created by Toyota Motor Corporation in Japan in the 1980s. The primary goal was to make products with lower costs and maintain high quality. Lean manufacturing seeks to eliminate unnecessary steps and activities in the production process. It consists of five basic elements: pull systems, continuous improvement, just-in-time, kaizen (continuous change), and 5S. Pull systems are able to produce exactly what the customer requires without extra work. Continuous improvement is the continuous improvement of existing processes. Just-in-time refers to when components and materials are delivered directly to the point where they are needed. Kaizen is continuous improvement. This can be achieved by making small, incremental changes every day. The 5S acronym stands for sort in order, shine standardize and maintain. These five elements are used together to ensure the best possible results.
Lean Production System
Six key concepts are the basis of lean production:
-
Flow: The goal is to move material and information as close as possible from customers.
-
Value stream mapping is the ability to divide a process into smaller tasks, and then create a flowchart that shows the entire process.
-
Five S's, Sort, Set in Order, Shine. Standardize. and Sustain.
-
Kanban - use visual signals such as colored tape, stickers, or other visual cues to keep track of inventory;
-
Theory of constraints - identify bottlenecks during the process and eliminate them with lean tools like Kanban boards.
-
Just-in-time delivery - Deliver components and materials right to your point of use.
-
Continuous improvement: Make incremental improvements to the process instead of overhauling it completely.