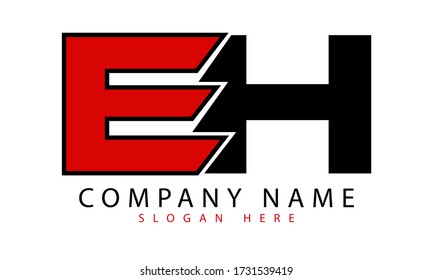
A degree that focuses exclusively on supply chain management is essential if you plan to pursue a career. A degree in Supply Chain Management will enable you to take the lead in a business. It includes strategic, tactical and operational levels. This helps to improve organizational performance. It requires excellent communication skills.
Project management can be considered a type of supply chain administration.
Supply chain management is an important aspect of any business, and project management can help you better manage your supply chain. Project management is a process that allows you to create and implement an organization plan. The primary goal of a project, is to create a project that meets your goals and meets your success criteria. Project managers ensure that your products and services meet your quality standards and are delivered on schedule. Project management can bring many advantages such as increased collaboration, cost-savings, quality controls, and risk mitigation. However, it is not without its drawbacks.
Although tactics and strategy are important, they should not be implemented without proper planning. A strategy that is not well-planned can lead to a project going sour and resulting in failure to meet its goals. For a supply chain project to succeed, project management is vital. Project managers can create solutions and implement new strategies by following best practices.
It can be at strategic, tactical and operational levels.
The three main levels of a supply chain are strategic, tactical and operational. The strategic level is crucial to supply chain success, as it sets the groundwork for all other levels. It involves the collection and analysis of data, the evaluation of the main factors that affect supply chains, and the making of decisions based on those information. While operational decisions can be made to meet customer demands, strategic decisions are essential to the overall success or the supply chain.
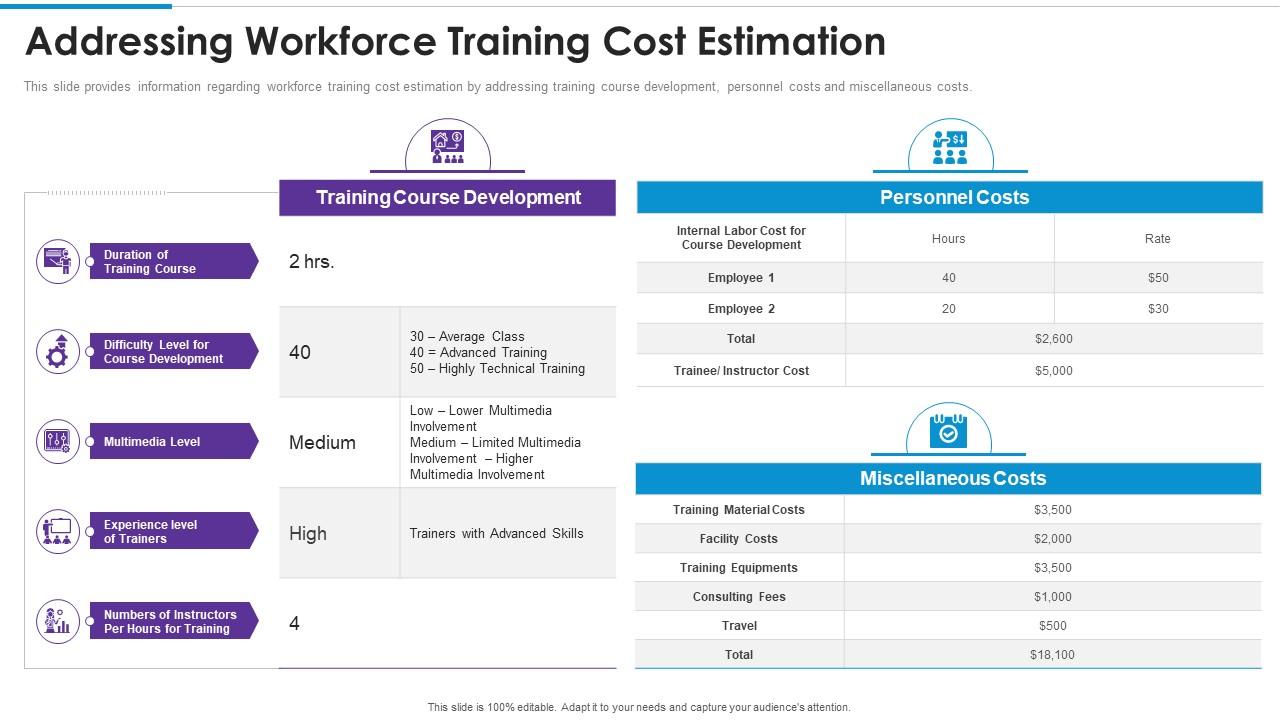
The strategic level describes the company's goals and strengths, as well as identifies weaknesses and formulates a vision for its future. The tactical level is responsible for executing strategies and taking specific steps to achieve them. These plans include planning, inventory management and production scheduling. Shipping and billing are also possible. Some analysts believe that the strategic level is now more important due to the globalization.
It improves organization performance
How well an organization can improve its supply chain management will determine how effective it is. Supply chain performance can be measured and evaluated through a variety of methods, including customer relationship management (CRM), internal supply chain management, and information sharing. These methods all help to improve organizational performance.
All supply chains, however, are not created equal. Some organizations have never designed a cohesive supply chain structure. This causes single functions to report to different parent roles, or different points within a parent role. This can cause confusion and slow down response time to urgent matters. As an example: Demand planning processes might report to the supply-chain manager in one country, but not to the sales managers in another. These organizational challenges can cause significant inefficiencies in companies.
Communication skills are required.
To succeed in supply chain management, you need to have strong communication skills. Supply chain leaders need to be able communicate complex ideas and encourage collaboration. Additionally, they should be able to produce accurate reports. These skills can help you improve your career prospects. You can further your education and obtain certifications if you are interested in a career in supply chain management.
As a supply-chain manager, you will have to interact with many people. You will need to be able to listen and empathize with others. Without empathy, your leadership may be rejected, particularly during periods of change. You may make employees feel unappreciated or rejected if they don't understand your concerns. It is important to understand yourself better and improve your skills.
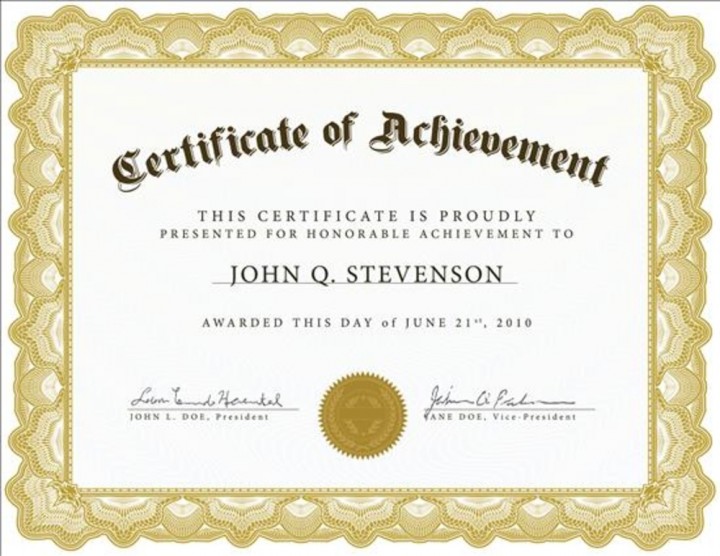
This can lead to a career as a supply chain manager.
A degree is in supply chain management may open the door to many opportunities. Supply chain managers manage a wide variety of processes from the initial forecasting of consumer demand to the finished product on store shelves. The job involves the management of complex networks of people, vendors, transportation systems, and other stakeholders. For this position to succeed, supply chain managers must have a solid understanding of business management and computer sciences.
You can either complete your degree in supply-chain management online or in the traditional classroom setting. Either way, you'll find your training to be comparable to a four-year program. Although online programs offer fewer opportunities for networking, the quality of training is equal to traditional schools. Strong analytical skills and a passion to work with data and forecasts are essential. A degree online will prepare you to teach others the technical aspects in supply chain management.
FAQ
What are the 3 main management styles?
There are three types of management: participative, laissez faire, and authoritarian. Each style is unique and has its strengths as well as weaknesses. What style do you prefer? Why?
Autoritarian – The leader sets the direction for everyone and expects them to follow. This style works well if an organization is large and stable.
Laissez faire - Each individual can decide for himself/herself. This approach works best in small, dynamic organizations.
Participative - The leader listens to ideas and suggestions from everyone. This approach works best in small organizations where everyone feels valued.
What are the four major functions of Management?
Management is responsible for planning, organizing, directing, and controlling people and resources. This includes setting goals, developing policies and procedures, and creating procedures.
Management aids an organization in reaching its goals by providing direction and coordination, control, leadership motivation, supervision, training, evaluation, and leadership.
The four main functions of management are:
Planning – Planning involves deciding what needs to happen.
Organizing: Organizing refers to deciding how things should work.
Directing - Directing means getting people to follow instructions.
Controlling - This is the ability to control people and ensure that they do their jobs according to plan.
What does Six Sigma mean?
Six Sigma uses statistical analysis for problems to be found, measured, analyzed root causes, corrected, and learned from.
The first step is to identify the problem.
The data is then analyzed and collected to identify trends.
The problem is then rectified.
Finally, the data are reanalyzed in order to determine if it has been resolved.
This continues until the problem has been solved.
What is TQM exactly?
The industrial revolution was when companies realized that they couldn't compete on price alone. This is what sparked the quality movement. They needed to improve quality and efficiency if they were going to remain competitive.
In response to this need for improvement, management developed Total Quality Management (TQM), which focused on improving all aspects of an organization's performance. It included continuous improvement, employee involvement and customer satisfaction.
What are management concepts?
Management concepts are the practices and principles managers use to manage people or resources. They cover topics such as job descriptions and performance evaluations, human resource policies, training programs, employee motivation, compens systems, organizational structure, among others.
Statistics
- The profession is expected to grow 7% by 2028, a bit faster than the national average. (wgu.edu)
- This field is expected to grow about 7% by 2028, a bit faster than the national average for job growth. (wgu.edu)
- Hire the top business lawyers and save up to 60% on legal fees (upcounsel.com)
- UpCounsel accepts only the top 5 percent of lawyers on its site. (upcounsel.com)
- 100% of the courses are offered online, and no campus visits are required — a big time-saver for you. (online.uc.edu)
External Links
How To
How is Lean Manufacturing done?
Lean Manufacturing uses structured methods to reduce waste, increase efficiency and reduce waste. They were developed by Toyota Motor Corporation in Japan during the 1980s. It was designed to produce high-quality products at lower prices while maintaining their quality. Lean manufacturing emphasizes removing unnecessary steps from the production process. It has five components: continuous improvement and pull systems; just-in time; continuous change; and kaizen (continuous innovation). Pull systems allow customers to get exactly what they want without having to do extra work. Continuous improvement refers to continuously improving existing processes. Just-in–time refers when components or materials are delivered immediately to their intended destination. Kaizen stands for continuous improvement. Kaizen can be described as a process of making small improvements continuously. Last but not least, 5S is for sort. To achieve the best results, these five elements must be used together.
Lean Production System
Six key concepts form the foundation of the lean production system:
-
Flow is about moving material and information as near as customers can.
-
Value stream mapping- This allows you to break down each step of a process and create a flowchart detailing the entire process.
-
Five S's: Sort, Shine Standardize, Sustain, Set In Order, Shine and Shine
-
Kanban - use visual signals such as colored tape, stickers, or other visual cues to keep track of inventory;
-
Theory of constraints - identify bottlenecks during the process and eliminate them with lean tools like Kanban boards.
-
Just-in-time delivery - Deliver components and materials right to your point of use.
-
Continuous improvement - make incremental improvements to the process rather than overhauling it all at once.