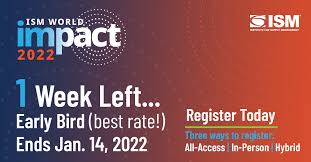
There are many factors that you should consider when determining whether your workplace has OSHA compliance. Paying attention to details and following all rules and standards are just a few of the factors. Other factors include creating a safe work environment and making sure that inspections are conducted. By following these guidelines, you will be on your way to being OSHA compliant.
Attention to detail
One of the most important aspects of creating an OSHA compliant product is attention to detail. Although it may sound like common sense, OSHA regulations are very important. To ensure a safe workplace, you will need to pay attention to details.
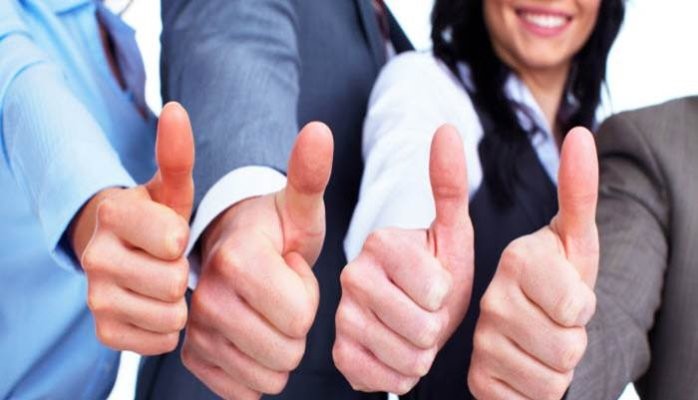
Every rule and every standard must be adhered to
OSHA's rule making process is based on Advance Notices, which solicit information from interested parties about proposed changes. These notices give details of the proposed rule as well as a deadline for public comments. After this period, interested parties can request a public hearing, which is typically scheduled for a specific date.
Creating a safe working environment
A safe working environment is a top priority for any organization. However, even with the best intentions, accidents can still happen. Employers should remind their employees about workplace safety. They should also check their safety manual against the list of recommended practices.
Inspections
OSHA-compliant inspections are conducted by a compliance officer who comes to your workplace with a purpose. These inspections last a few minutes and are designed to help you understand the business. The inspector will evaluate your safety risks, speak to employees privately, and look over records. While the inspector will discuss with you how to reduce or prevent hazards, the inspection will be short and efficient.
Penalties
OSHA compliance penalties are an important part of the process to ensure safety for your employees. There are three types OSHA penalties: repeated violations, willful violations and failure to abate violations. Each offense can lead to a fine of anywhere from $1,036 to $4,502 and the second offense can result in jail time. Repeated violations have more severe penalties. Jail time is possible for repeat offenders.
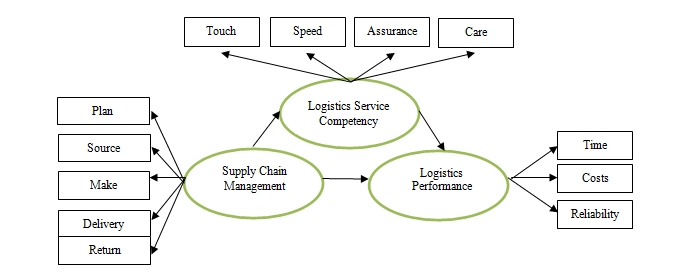
Resources
OSHA is a federal agency that ensures worker safety. Congress passed the OSH Act on December 7, 1970. It establishes federal standards for workplace safety. It also provides resources to small businesses, including training and a process to file reports and raise safety concerns.
FAQ
What is Six Sigma, exactly?
It's a method for quality improvement that focuses on customer service as well as continuous learning. It is a method that eliminates defects using statistical techniques.
Motorola invented Six Sigma in 1986 as part its efforts to improve manufacturing.
The idea spread quickly in the industry. Today many organizations use six-sigma techniques to improve product design.
What are the key management skills?
Managerial skills are crucial for every business owner, regardless of whether they run a small store in their locality or a large corporation. These skills include the ability of managing people, finances, time, space, and other factors.
Managerial skills are required when setting goals and objectives and planning strategies, leading employees, motivating them, solving problems, creating policies, procedures, or managing change.
As you can see there is no end to the number of managerial tasks.
What does it mean to say "project management"
That is the management of all activities associated with a project.
These include planning the scope and identifying the needs, creating the budget, organizing the team, scheduling the work and monitoring progress. Finally, we close down the project.
What is the main difference between Six Sigma Six Sigma TQM and Six Sigma Six Sigma?
The key difference between the two quality management tools is that while six-sigma focuses its efforts on eliminating defects, total quality management (TQM), focuses more on improving processes and reducing cost.
Six Sigma is a method for continuous improvement. This approach emphasizes eliminating defects through statistical methods like control charts, Pareto analysis, and p-charts.
This method has the goal to reduce variation of product output. This is done by identifying and correcting the root causes of problems.
Total quality management involves measuring and monitoring all aspects of the organization. It also includes the training of employees to improve performance.
It is commonly used as a strategy for increasing productivity.
Statistics
- This field is expected to grow about 7% by 2028, a bit faster than the national average for job growth. (wgu.edu)
- Your choice in Step 5 may very likely be the same or similar to the alternative you placed at the top of your list at the end of Step 4. (umassd.edu)
- As of 2020, personal bankers or tellers make an average of $32,620 per year, according to the BLS. (wgu.edu)
- Hire the top business lawyers and save up to 60% on legal fees (upcounsel.com)
- UpCounsel accepts only the top 5 percent of lawyers on its site. (upcounsel.com)
External Links
How To
How can Lean Manufacturing be done?
Lean Manufacturing techniques are used to reduce waste while increasing efficiency by using structured methods. They were created by Toyota Motor Corporation in Japan in the 1980s. The goal was to produce quality products at lower cost. Lean manufacturing seeks to eliminate unnecessary steps and activities in the production process. It is made up of five elements: continuous improvement, continuous improvement, just in-time, continuous change, and 5S. The production of only what the customer needs without extra work is called pull systems. Continuous improvement involves constantly improving upon existing processes. Just-in-time is when components and other materials are delivered at their destination in a timely manner. Kaizen refers to continuous improvement. It is achieved through small changes that are made continuously. The 5S acronym stands for sort in order, shine standardize and maintain. To achieve the best results, these five elements must be used together.
Lean Production System
Six key concepts form the foundation of the lean production system:
-
Flow - The focus is on moving information and material as close as possible to customers.
-
Value stream mapping - Break down each stage in a process into distinct tasks and create an overview of the whole process.
-
Five S's, Sort, Set in Order, Shine. Standardize. and Sustain.
-
Kanban - visual cues such as stickers or colored tape can be used to track inventory.
-
Theory of constraints: identify bottlenecks in your process and eliminate them using lean tools, such as kanban board.
-
Just-in-time - deliver components and materials directly to the point of use;
-
Continuous improvement - incremental improvements are made to the process, not a complete overhaul.