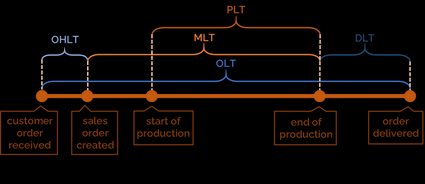
Lack of transparency is a common failing in managing risk. This was evident in the scandal involving coronavirus deaths. Data silos and a lack of data are other issues. Processes were not created with risk in mind. Risk managers often settle for the data they have easy access to and fail to properly identify risks that could lead to negative consequences. This is a common problem and one that can be difficult to fix.
Negative risks
Managers can employ five fundamental risk response strategies to manage negative risks and threats. The type of risk and the level of exposure will determine which strategies are best. They also consider the likelihood of occurrence, and the impact on project objectives. These strategies, which are the most effective, are used when risk is considered critical. The risk is not as severe when the transfer-and-accept strategy is used.
People, processes, technology and resources are all affected by negative and positive risk. If managed well, positive risk can bring about positive results. If managed correctly, positive risks could lead to project completion sooner than expected and a greater return on investment. Negative risks can occur in any situation, and a negative risk may be avoided by implementing the right risk management practices. These risks pose problems and can cause delays and impact on project schedules, budgets, and schedules.
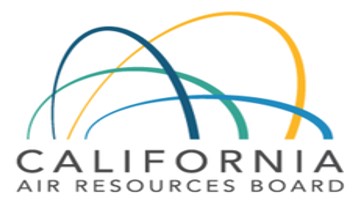
Communication
Communication of risks is an important part of risk management. Whether it is through a formal document or a social media post, a professional's communication must be open and honest. There is a risk that the risk will be misunderstood, but communication professionals can mitigate that risk by keeping it open and honest. A simple example of communicating a risk is Hurricane Harvey. In 2017, Hurricane Harvey was a devastating hurricane that threatened Houston. Officials used social media, local and national media to inform residents of the danger to evacuate. The professionals need to direct people to reliable sources of information.
Poor communication is one of the greatest risks when managing a project. If there is poor communication, it can make or break a project. Communicating effectively can increase employee engagement and reduce the risk of miscommunication. Activities that enhance communication should be part of a project's management risk assessment. Once the risk assessment has been completed, project managers are able to take steps to reduce it. Stakeholders can be involved in the communication risk assessment process.
Consultation
As part of the risk management process, an organisation must involve all stakeholders in the project. There are many stakeholders to consider, including internal and external partners, as well as stakeholders that aren't directly involved in the project. It is important to engage key stakeholders in the risk management process so that all parties can understand the risks and expectations involved. To ensure the appropriate level of consultation, project teams should involve all stakeholders during the risk assessment and management process. Here are some tips to ensure all stakeholders are involved in the consultation process.
In addition to assessing risks, a risk management consultant will help prioritize risks. This is essential because high-risk issues require immediate attention. A lower-risk issue will require a modest remediation strategy. Consulting can help organizations identify and prioritize risks, as well as create a customized risk management plan. The consultants can also help companies develop an action plan to reduce risks and improve their overall risk management.
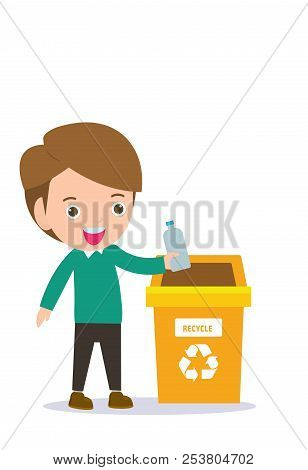
Top-down
There are clear advantages and disadvantages to top down risk management. To set up, it takes time, effort and expert knowledge. It can be very individualized, so what one manager may have learned in one industry may not work for another. However, it is an excellent risk management tool. Although not widely accepted, it is becoming more common. Here are some more reasons.
When a project is in its initial stages, top-down risks management techniques can be most useful. Risk management techniques are most effective in this early phase. You can draw on the experience from previous projects. Top-down management accountability can be enhanced by top-down models and methods from previous projects that are evidence-based. If implemented correctly, top-down risk management techniques can greatly reduce project risk. In addition, they can help managers and teams meet their financial obligations to stakeholders.
FAQ
What's the difference between Six Sigma and TQM?
The main difference between these two quality-management tools is that six-sigma concentrates on eliminating defects while total QM (TQM), focuses upon improving processes and reducing expenses.
Six Sigma stands for continuous improvement. It emphasizes the elimination of defects by using statistical methods such as control charts, p-charts, and Pareto analysis.
This method attempts to reduce variations in product output. This is done by identifying and correcting the root causes of problems.
Total quality management includes monitoring and measuring all aspects of an organization's performance. It also includes training employees to improve performance.
It is often used to increase productivity.
How does Six Sigma work?
Six Sigma uses statistical analysis to find problems, measure them, analyze root causes, correct problems, and learn from experience.
The first step is to identify the problem.
Next, data is collected and analyzed to identify trends and patterns.
The problem is then rectified.
Finally, data is reanalyzed to determine whether the problem has been eliminated.
This continues until you solve the problem.
What is the difference in leadership and management?
Leadership is about influence. Management is about controlling others.
A leader inspires others while a manager directs them.
A leader motivates people and keeps them on task.
A leader develops people; a manager manages people.
What is TQM?
When manufacturing companies realized that price was not enough to compete, the industrial revolution brought about the quality movement. To remain competitive, they had to improve quality as well as efficiency.
To address this need for improvement management created Total Quality Management (TQM) which aimed to improve all aspects of an organization's performance. It included continuous improvement, employee involvement and customer satisfaction.
What is a basic management tool used in decision-making?
A decision matrix, a simple yet powerful tool for managers to make decisions, is the best. It allows them to consider all possible solutions.
A decision matrix can be used to show alternative options as rows or columns. This allows one to see how each alternative impacts other options.
In this example, there are four possible options represented by boxes on the left-hand side of the matrix. Each box represents one option. The status quo (the current condition) is shown in the top row, and what would happen if there was no change?
The effect of Option 1 can be seen in the middle column. It would increase sales by $2 million to 3 million in this instance.
These are the results of selecting Options 2 or 3. These are good changes, they increase sales by $1million or $500,000. They also have negative consequences. Option 2 can increase costs by $100 million, while Option 3 can reduce profits by $200,000.
The final column shows the results for Option 4. This results in a decrease of sales by $1,000,000
The best part about using a decision matrix to guide you is that you don’t need to keep track of which numbers go where. The best thing about a decision matrix is that you can simply look at the cells, and immediately know whether one option is better or not.
This is because the matrix has already taken care of the hard work for you. It's as easy as comparing numbers in the appropriate cells.
Here's a sample of how you might use decision matrixes in your business.
Decide whether you want to invest more in advertising. You'll be able increase your monthly revenue by $5000 if you do. But, you will also incur additional expenses of $10 thousand per month.
If you look at the cell that says "Advertising", you can see the number $15,000. Advertising is worth much more than the investment cost.
What role should a manager play within a company
The role of a manager varies from one industry to another.
Managers generally oversee the day-today operations of a business.
He/she makes sure that the company meets its financial obligations, and that it produces goods or services that customers desire.
He/she will ensure that employees follow all rules and regulations, and adhere to quality standards.
He/she plans new products and services and oversees marketing campaigns.
Statistics
- Your choice in Step 5 may very likely be the same or similar to the alternative you placed at the top of your list at the end of Step 4. (umassd.edu)
- Hire the top business lawyers and save up to 60% on legal fees (upcounsel.com)
- 100% of the courses are offered online, and no campus visits are required — a big time-saver for you. (online.uc.edu)
- This field is expected to grow about 7% by 2028, a bit faster than the national average for job growth. (wgu.edu)
- Our program is 100% engineered for your success. (online.uc.edu)
External Links
How To
What is Lean Manufacturing?
Lean Manufacturing techniques are used to reduce waste while increasing efficiency by using structured methods. These processes were created by Toyota Motor Corporation, Japan in the 1980s. The main goal was to produce products at lower costs while maintaining quality. Lean manufacturing seeks to eliminate unnecessary steps and activities in the production process. It consists of five basic elements: pull systems, continuous improvement, just-in-time, kaizen (continuous change), and 5S. It is a system that produces only the product the customer requests without additional work. Continuous improvement refers to continuously improving existing processes. Just-in time refers to components and materials being delivered right at the place they are needed. Kaizen means continuous improvement. Kaizen involves making small changes and improving continuously. Five-S stands for sort. It is also the acronym for shine, standardize (standardize), and sustain. These five elements can be combined to achieve the best possible results.
Lean Production System
Six key concepts form the foundation of the lean production system:
-
Flow - focuses on moving information and materials as close to customers as possible.
-
Value stream mapping is the ability to divide a process into smaller tasks, and then create a flowchart that shows the entire process.
-
Five S's, Sort, Set in Order, Shine. Standardize. and Sustain.
-
Kanban is a visual system that uses visual cues like stickers, colored tape or stickers to keep track and monitor inventory.
-
Theory of constraints - identify bottlenecks during the process and eliminate them with lean tools like Kanban boards.
-
Just-in-time - deliver components and materials directly to the point of use;
-
Continuous improvement - incremental improvements are made to the process, not a complete overhaul.