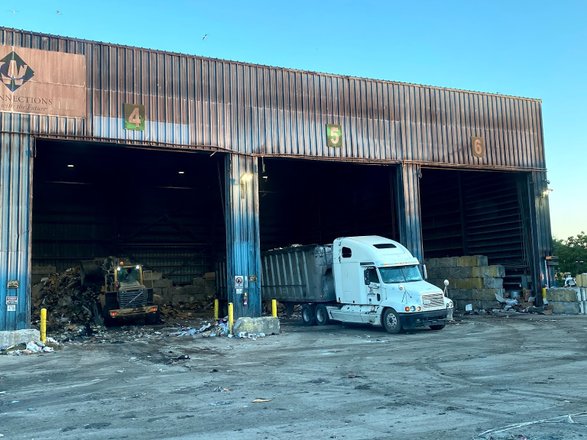
It is vital to have a framework for interprofessional teamwork in order to make a STEM project a success. This allows team members to identify common problems and create strategies to address them. By presenting a succinct report, students can practice oral communication.
Framework for inter-professional collaboration
The framework for interprofessional cooperation is a theoretical approach to improving interprofessional collaboration in primary care. The framework for inter-professional teamwork is based on findings from various research studies. It includes a variety of factors. The framework is composed of six key themes. These themes relate to team structure and synergy between team members, the delineation of roles and responsibilities, team competence to fulfill designated duties, and organisational context for teamwork.
It is essential to define the roles and activities for each member of a PHC team in order to encourage teamwork. The CN and GP roles in team care are often ambiguous, leading to conflict and mutual dissatisfaction. CNs can also be in a limbo, with limited involvement in patient care, and sometimes being over-involved. This often leads to conflict.
Templates
A template is a great tool to facilitate project collaboration. A template serves as a guideline and repository for the entire team. It helps them to know what to do and who to reach. It also helps them stay on track. Here are some tips to help you create a template.
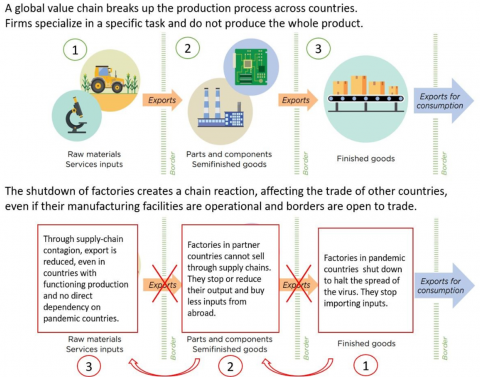
Teamwork project templates can be customized to meet the specific needs of your organization. These templates can be customized to help your team save time and streamline their processes. They can also improve communication within the team, which is essential for planning and execution. Because they are clear and concise, they can help you avoid human mistakes.
Gantt charts
It can be difficult to track teamwork in a project due to the many dependencies among tasks. Gantt charts allow you to see the tasks details and dependencies of your team. The chart will also list the team’s responsibilities and their start and ending dates.
Gantt chart are great for project managers. They allow them to view all tasks in one place. Gantt chart are also a great way to encourage team camaraderie. Gantt chart are a great tool to visualize project goals. They also create an environment where team members can work together in order to achieve them.
Filtering tool
The Filtering Tool for Project on Teamwork allows you to select key data from your team's tasks. This tool is useful for identifying tasks that have been completed or begun. This will save you the time of scrolling through endless amounts of data in order to find the information that you need.
The filtering tool to project on Teamwork can be found in various areas of the site. It includes tasks, projects, time logs, and more. To use this tool, click the filters tab at the top right of any section. You can also view filters from a user account and drag them and drop to arrange them.
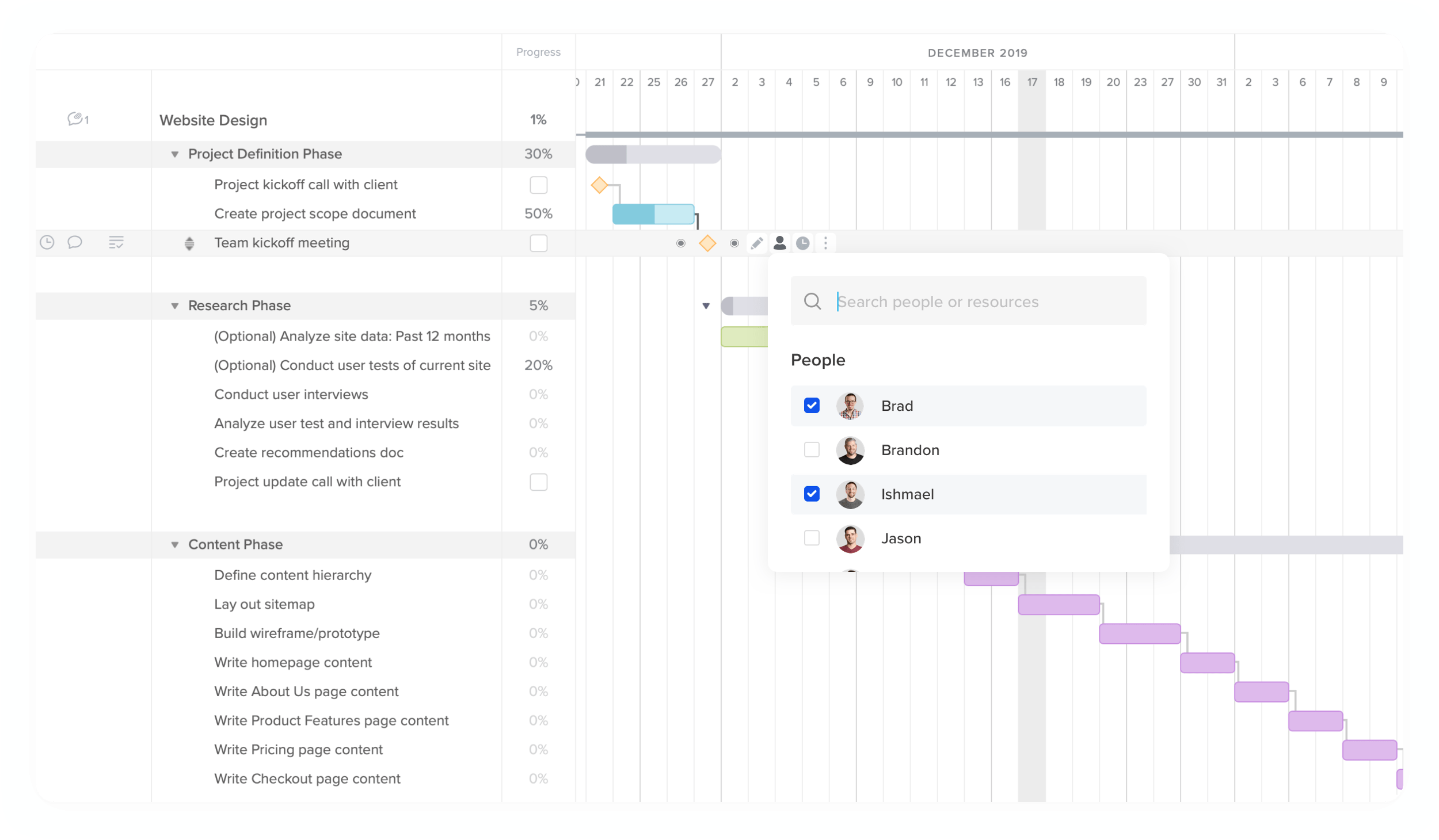
Task list
A task list is a way of grouping all the tasks in a project. Task lists can be made by adding tasks to the list, as well assigning them individuals, groups or companies. You can either assign due dates to tasks, or you can leave them unassigned. To add tasks to a project’s task list, give them a title as well as a due date.
To create a new task list in Teamwork, simply click the Add Task List button. Once you have created your task list, you can name it, add notes, set a start date, and even set a due date. You can also choose to make the list public, private, or both.
FAQ
What is the difference between TQM and Six Sigma?
The main difference in these two quality management tools lies in the fact that six sigma is focused on eliminating defects and total quality management (TQM), emphasizes improving processes and reducing costs.
Six Sigma can be described as a strategy for continuous improvement. This method emphasizes eliminating defects using statistical methods such p-charts, control charts, and Pareto analysis.
This method has the goal to reduce variation of product output. This is done by identifying and correcting the root causes of problems.
Total quality management refers to the monitoring and measurement of all aspects in an organization. This includes training employees to improve their performance.
It is frequently used as an approach to increasing productivity.
What are management principles?
Management concepts are the principles and practices used by managers to manage people, resources. They cover topics like job descriptions (job descriptions), performance evaluations, training programmes, employee motivation and compensation systems.
What is the difference of leadership and management?
Leadership is about influencing others. Management is about controlling others.
A leader inspires others while a manager directs them.
A leader motivates people and keeps them on task.
A leader develops people; a manager manages people.
What are the three basic management styles?
These are the three most common management styles: participative (authoritarian), laissez-faire (leavez-faire), and authoritarian. Each style is unique and has its strengths as well as weaknesses. Which style do your prefer? Why?
Authoritarian – The leader sets a direction and expects everyone follows it. This style works well if an organization is large and stable.
Laissez faire - Each individual can decide for himself/herself. This style is best when the organization has a small but dynamic group.
Participative – Leaders are open to suggestions and ideas from everyone. This is a great style for smaller organizations that value everyone.
What are the main four functions of management
Management is responsible to plan, organize, direct, and control people and resources. It includes the development of policies and procedures as well as setting goals.
Management assists an organization in achieving its goals by providing direction, coordination and control, leadership, motivation, supervision and training, as well as evaluation.
Management's four main functions are:
Planning - Planning is about determining what must be done.
Organizing - Organization involves deciding what should be done.
Directing - This refers to getting people follow instructions.
Controlling: Controlling refers to making sure that people do what they are supposed to.
What are the most important management skills?
Any business owner needs to be able to manage people, finances, resources and time. They are the ability to manage people and finances, space, money, and other factors.
Managerial skills are required when setting goals and objectives and planning strategies, leading employees, motivating them, solving problems, creating policies, procedures, or managing change.
You can see that there are many managerial duties.
How does Six Sigma work
Six Sigma uses statistical analyses to locate problems, measure them, analyze root cause, fix problems and learn from the experience.
The first step is identifying the problem.
Next, data are collected and analyzed in order to identify patterns and trends.
Then, corrective actions can be taken to resolve the problem.
Final analysis of data is done to determine if the problem has been solved.
This continues until the problem has been solved.
Statistics
- The average salary for financial advisors in 2021 is around $60,000 per year, with the top 10% of the profession making more than $111,000 per year. (wgu.edu)
- This field is expected to grow about 7% by 2028, a bit faster than the national average for job growth. (wgu.edu)
- Your choice in Step 5 may very likely be the same or similar to the alternative you placed at the top of your list at the end of Step 4. (umassd.edu)
- Hire the top business lawyers and save up to 60% on legal fees (upcounsel.com)
- The profession is expected to grow 7% by 2028, a bit faster than the national average. (wgu.edu)
External Links
How To
How can you implement the Kaizen technique?
Kaizen means continuous improvement. The term was coined in the 1950s at Toyota Motor Corporation and refers to the Japanese philosophy emphasizing constant improvement through small incremental changes. It's a team effort to continuously improve processes.
Kaizen is one of the most effective methods used in Lean Manufacturing. In this concept, employees who are responsible for the production line must identify problems that exist during the manufacturing process and try to solve them before they become big issues. This will increase the quality and decrease the cost of the products.
Kaizen is an approach to making every worker aware and alert to what is happening around them. To prevent problems from happening, any problem should be addressed immediately. It is important that employees report any problems they see while on the job to their managers.
Kaizen has a set of basic principles that we all follow. We always start from the end product and move toward the beginning. We can improve the factory by first fixing the machines that make it. Then, we fix the machines that produce components and then the ones that produce raw materials. Finally, we repair the workers who are directly involved with these machines.
This is why it's called "kaizen" because it works step-by-step to improve everything. We finish fixing the factory and then go back to the beginning. This continues until we achieve perfection.
You need to know how to measure the effectiveness of kaizen within your business. There are several ways that you can tell if your kaizen system is working. One method is to inspect the finished products for defects. Another way is to check how much productivity has grown since kaizen was implemented.
A good way to determine whether kaizen has been implemented is to ask why. You were trying to save money or obey the law? It was a way to save money or help you succeed.
Congratulations if you answered "yes" to any of the questions. You're ready to start kaizen.