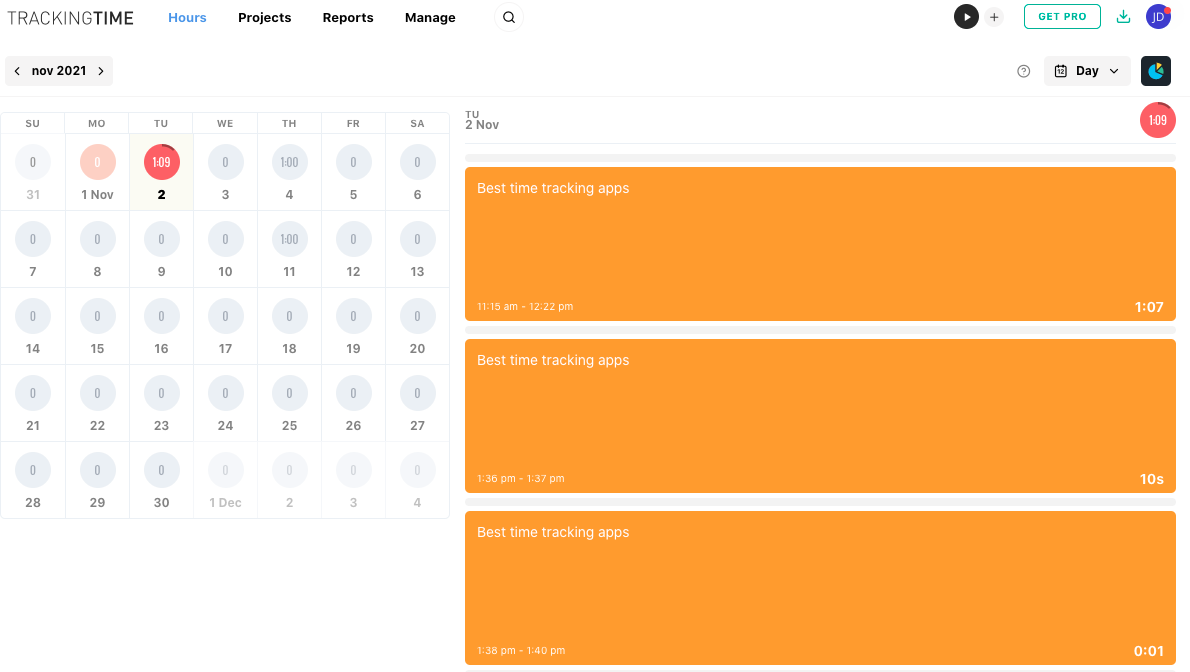
A risk matrix is a simple but powerful tool that helps you reduce the probability of risks and minimize their impact on operations. It shows how exposed a company is to particular risks and the effort required for managing them. It helps to make the situation more clear and offers valuable insights for future decisions. Here are some benefits to risk matrix analysis.
nTask
Project management is not complete without a risk assessment matrix. It allows you categorize risk by severity and probability. The risk matrix allows you to prioritize risks and decide which risks to reduce. The built-in risk matrix of nTask populates all required fields automatically.
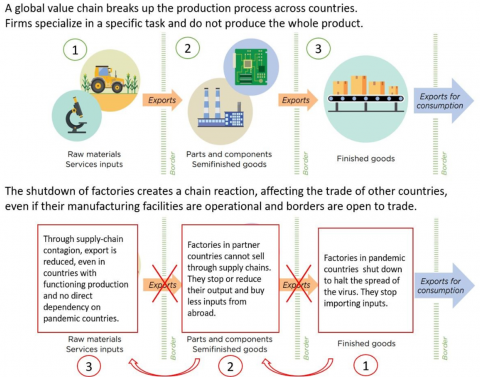
Each component of a risk matrix represents a possible risk. The risk component's probability is measured by a numerical value, from one to five. The nTask matrix considers severity. Critical risks indicate the possibility of financial loss, serious injuries, or damage.
Excel
Excel's risk matrix can be a powerful tool for analyzing risks and formulating the right risk response strategy. These matrices incorporate a variety risk assessment criteria including severity and likelihood. These criteria combine to determine the risk impact. For example, a risk that has a severity level of 5 and a probability of 25 would be classified as a medium-risk. You can either use the default risk assessment matrix, or modify the template to fit your needs.
Once you have created a template you can start filling in details. You can use the basic risk assessment methods to assign different colours labels to different risks based on their likelihood, extent, or damage. While you don't have to measure all risk, it is helpful to have a color-coding system. The matrix can be modified by selecting the cells and clicking on Fill tab.
Wrike
A Wrike project risk matrix template is an excellent tool for tracking and capturing risks. You can quickly and easily capture and track risks with the help of pre-built RAID entries and request forms. A quick view of the risk matrix will give you an overview of all risks.
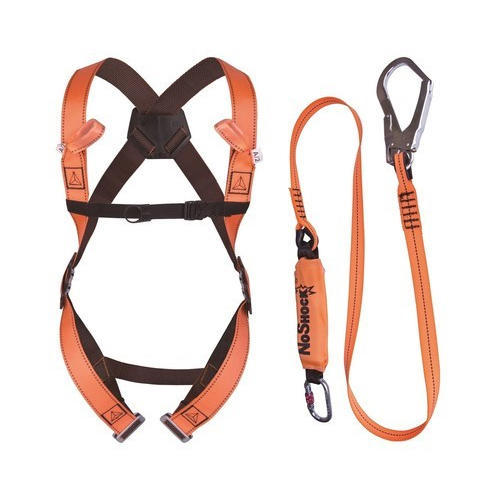
When creating a Wrike risk matrix, you should specify the severity and probability of risks for each category. Then, you can use Wrike to automatically update and adjust the risk matrix. This will eliminate the need for manual calculations using Excel. The results of the risk matrix will then be used to develop a risk response plan. High-risk threats should be addressed immediately. Low risk risks may require additional time.
FAQ
How does Six Sigma work
Six Sigma employs statistical analysis to identify problems, measure them and analyze root causes. Six Sigma also uses experience to correct problems.
The first step is to identify the problem.
The data is then analyzed and collected to identify trends.
The problem is then rectified.
The data are then reanalyzed to see if the problem is solved.
This cycle continues until there is a solution.
What is Kaizen?
Kaizen refers to a Japanese term that stands for "continuous improvements." It is a philosophy which encourages employees in continuously improving their work environment.
Kaizen is founded on the belief of everyone being able to do their job well.
What is a basic management tool used in decision-making?
A decision matrix is an easy but powerful tool to aid managers in making informed decisions. It helps them think systematically about all the options available to them.
A decision matrix is a way of representing alternatives as rows and columns. It is easy to see how each option affects the other options.
In this example, we have four possible alternatives represented by the boxes on the left side of the matrix. Each box represents an alternative. The status quo (the current condition) is shown in the top row, and what would happen if there was no change?
The middle column displays the impact of selecting Option 1. In this example, it would lead to an increase in sales of between $2 million and $3 million.
The following columns illustrate the impact of Options 2 and 3. These are good changes, they increase sales by $1million or $500,000. However, these also involve negative consequences. For instance, Option 2 increases cost by $100 thousand while Option 3 reduces profits by $200 thousand.
Finally, the last column shows the results of choosing Option 4. This would result in a reduction of sales of $1 million.
The best thing about a decision matrix is the fact that you don't have to remember which numbers go with what. You just look at the cells and know immediately whether any given a choice is better than another.
This is because the matrix has already taken care of the hard work for you. It's as easy as comparing numbers in the appropriate cells.
Here's an example showing how you might use a Decision Matrix in your business.
You want to decide whether or not to invest more money into advertising. You'll be able increase your monthly revenue by $5000 if you do. You'll also have additional expenses up to $10,000.
By looking at the cell just below "Advertising", the net result can be calculated as $15 thousand. Advertising is worth more than its cost.
Statistics
- Hire the top business lawyers and save up to 60% on legal fees (upcounsel.com)
- The average salary for financial advisors in 2021 is around $60,000 per year, with the top 10% of the profession making more than $111,000 per year. (wgu.edu)
- Our program is 100% engineered for your success. (online.uc.edu)
- The BLS says that financial services jobs like banking are expected to grow 4% by 2030, about as fast as the national average. (wgu.edu)
- This field is expected to grow about 7% by 2028, a bit faster than the national average for job growth. (wgu.edu)
External Links
How To
How is Lean Manufacturing done?
Lean Manufacturing techniques are used to reduce waste while increasing efficiency by using structured methods. These processes were created by Toyota Motor Corporation, Japan in the 1980s. The main goal was to produce products at lower costs while maintaining quality. Lean manufacturing eliminates unnecessary steps and activities from a production process. It is made up of five elements: continuous improvement, continuous improvement, just in-time, continuous change, and 5S. Pull systems involve producing only what the customer wants without any extra work. Continuous improvement means continuously improving on existing processes. Just-in–time refers when components or materials are delivered immediately to their intended destination. Kaizen is continuous improvement. This can be achieved by making small, incremental changes every day. Finally, 5S stands for sort, set in order, shine, standardize, and sustain. These five elements are used together to ensure the best possible results.
Lean Production System
Six key concepts make up the lean manufacturing system.
-
Flow - focus on moving material and information as close to customers as possible;
-
Value stream mapping is the ability to divide a process into smaller tasks, and then create a flowchart that shows the entire process.
-
Five S’s - Sorted, In Order. Shine. Standardize. And Sustain.
-
Kanban is a visual system that uses visual cues like stickers, colored tape or stickers to keep track and monitor inventory.
-
Theory of Constraints - Identify bottlenecks in the process, and eliminate them using lean tools such kanban boards.
-
Just-in Time - Send components and material directly to the point-of-use;
-
Continuous improvement - make incremental improvements to the process rather than overhauling it all at once.