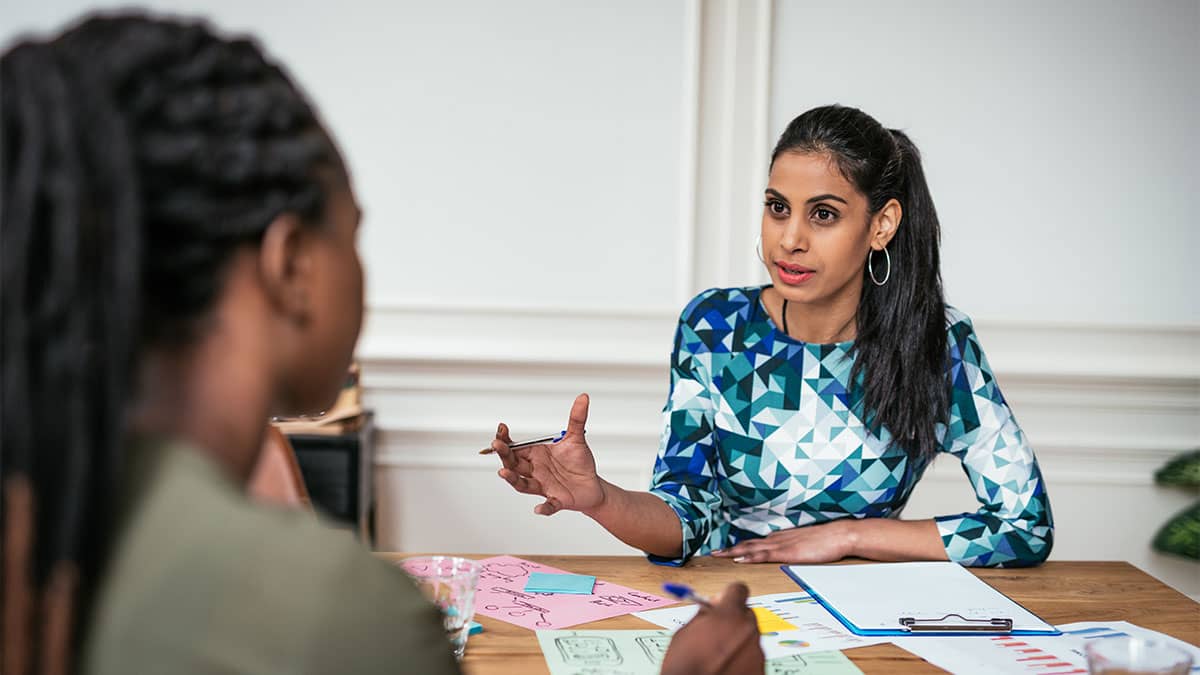
Heber Springs in Arkansas is an excellent choice for summer vacation. The town offers many amenities, such as a community market, golf courses, and a museum. Below, learn more about this charming little community. It is located within the Cleburne County seat. It was home to 7,165 people at the 2010 census. The town was founded in 1848 and is a popular tourist destination.
Heber Springs is an idyllic summer resort
Heber Springs is characterized by a subtropical humid climate. This means that the summers can be hot, but also have periods of winterlike conditions. The city averages just below 50mm of snowfall each year and gets 1234mm of hail or rain per year. August is the second-warmest and July the warmest months. January is the coldest month.
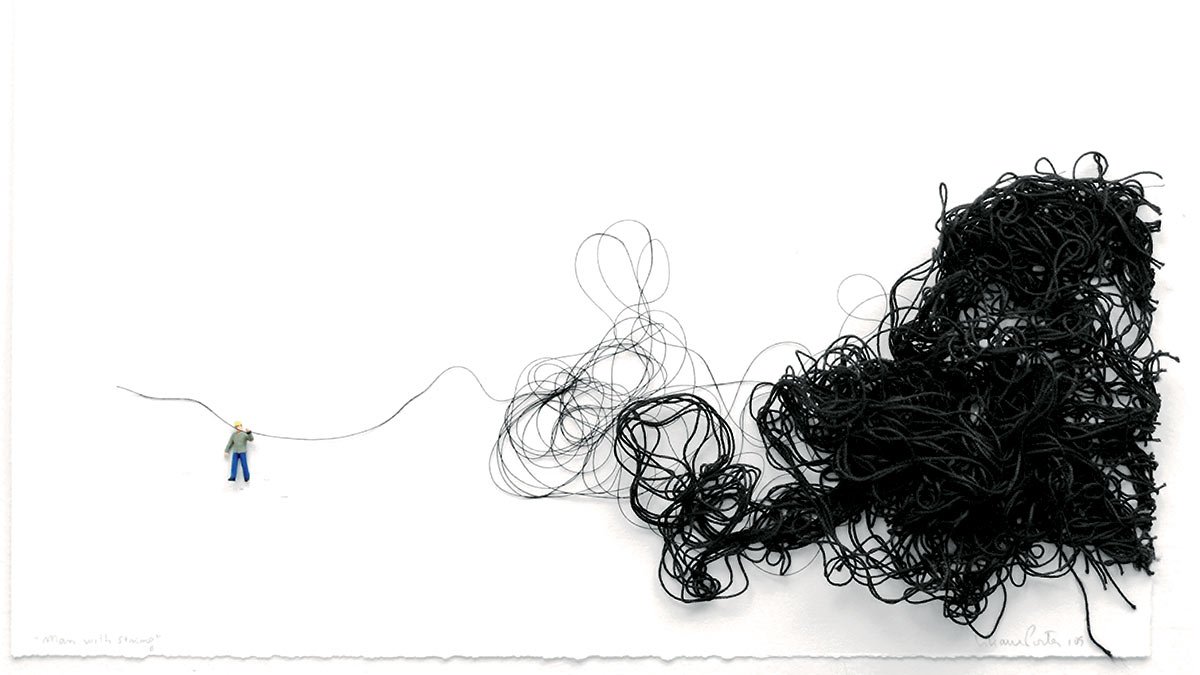
There is a golf course.
Heber Springs offers a variety of excellent courses for golf fans. The Lost Creek Golf Club is a semi-private course that plays over 6239 yards from the back tees and has an average slope rating of 113. Stan Lee designed the course, which opened in 1990. There are many public courses available in the city. Here are some of the best.
It has a community market
For fresh, locally-grown organic produce and other artisan foods, the town of Heber Springs has a community market. This market can be found on the Heber Springs courthouse lawn. The market features produce grown in an aquaponics greenhouse and eggs sourced from surrounding farms. Amish-made products, including flowers, seeds and pellet grills are all available.
It even has a museum
Cleburne County Museum can be found in the old Heber Springs Post Office. It was established in 1937. The museum occupies a larger space than the Post Office, and is home to an evocative panorama painted by H. Louis Freund in 1939. Max Frauenthal, who dubbed the town Sugar Loaf Springs in honor of the curative mineral water found there, founded the city in 1883.
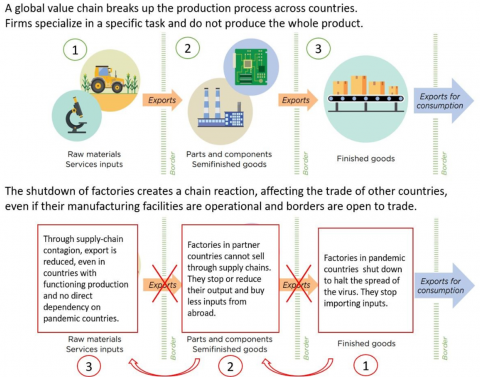
It has its own hatchery
Hatchery Creek Hatchery began production in 1965. The hatchery stocks rainbow and brook trout into the tailwaters of federally owned dams. The hatchery offers great recreational fishing opportunities as well as a huge economic benefit to the surrounding community. Many hatchery fish can be sold to local restaurants and then released into the rivers during the warmer months. This allows local businesses to reap the benefits of increased tourism.
FAQ
What are the five management process?
Each business has five stages: planning, execution and monitoring.
Planning is about setting goals for your future. It includes defining what you want to achieve and how you plan to do it.
Execution happens when you actually do the plan. It is important to ensure that everyone follows the plans.
Monitoring is checking on progress towards achieving your objectives. Regular reviews of performance against budgets and targets should be part of this process.
Each year, reviews are held at the end. They allow for an assessment of whether all went well throughout the year. If not, then it may be possible to make adjustments in order to improve performance next time.
Evaluation takes place after the annual review. It helps to identify what went well and what didn’t. It also provides feedback on the performance of people.
What do we mean when we say "project management"?
This refers to managing all activities that are involved in a project's execution.
We help you define the scope of your project, identify the requirements, prepare the budget, organize the team, plan the work, monitor progress and evaluate the results before closing down the project.
What are the main four functions of management
Management is responsible for organizing, managing, directing and controlling people, resources, and other activities. This includes setting goals, developing policies and procedures, and creating procedures.
Organizations can achieve their goals through management. This includes leadership, coordination, control and motivation.
The following are the four core functions of management
Planning - Planning is about determining what must be done.
Organizing: Organizing refers to deciding how things should work.
Directing - This refers to getting people follow instructions.
Controlling – Controlling is the process of ensuring that tasks are completed according to plan.
What are the steps to take in order to make a management decision?
Managers face complex and multifaceted decision-making challenges. It involves many elements, including analysis, strategy. planning. implementation. measurement. evaluation. feedback.
Remember that people are humans just like you, and will make mistakes. This is the key to managing them. You can always improve your performance, provided you are willing to make the effort.
This video shows you how management makes decisions. We'll discuss the different types and reasons they are important. Managers should also know how to navigate them. The following topics will be covered:
Why is project management important for companies?
Project management techniques are used in order to ensure projects run smoothly, and that deadlines are met.
This is because most businesses rely heavily on project work to produce goods and services.
These projects are essential for companies.
Companies that do not manage their projects effectively risk losing time, money, or reputation.
Why is it so hard to make smart business decisions?
Businesses are complex systems, and they have many moving parts. The people who run them must juggle multiple priorities at once while also dealing with uncertainty and complexity.
Understanding how these factors impact the whole system is key to making informed decisions.
To do this, you must think carefully about what each part of the system does and why. Next, consider how each piece interacts with the others.
You need to ask yourself if your previous actions have led you to make unfounded assumptions. If so, it might be worth reexamining them.
You can always ask someone for help if you still have questions after all of this. You might find their perspective is different from yours and they may have insight that can help you find the solution.
Statistics
- The average salary for financial advisors in 2021 is around $60,000 per year, with the top 10% of the profession making more than $111,000 per year. (wgu.edu)
- This field is expected to grow about 7% by 2028, a bit faster than the national average for job growth. (wgu.edu)
- The BLS says that financial services jobs like banking are expected to grow 4% by 2030, about as fast as the national average. (wgu.edu)
- Our program is 100% engineered for your success. (online.uc.edu)
- UpCounsel accepts only the top 5 percent of lawyers on its site. (upcounsel.com)
External Links
How To
What is Lean Manufacturing?
Lean Manufacturing processes are used to reduce waste and improve efficiency through structured methods. They were created by Toyota Motor Corporation in Japan in the 1980s. The aim was to produce better quality products at lower costs. Lean manufacturing eliminates unnecessary steps and activities from a production process. It has five components: continuous improvement and pull systems; just-in time; continuous change; and kaizen (continuous innovation). It is a system that produces only the product the customer requests without additional work. Continuous improvement refers to continuously improving existing processes. Just-in–time refers when components or materials are delivered immediately to their intended destination. Kaizen means continuous improvement, which is achieved by implementing small changes continuously. Five-S stands for sort. It is also the acronym for shine, standardize (standardize), and sustain. These five elements can be combined to achieve the best possible results.
Lean Production System
Six key concepts form the foundation of the lean production system:
-
Flow - focuses on moving information and materials as close to customers as possible.
-
Value stream mapping: This is a way to break down each stage into separate tasks and create a flowchart for the entire process.
-
Five S's - Sort, Set In Order, Shine, Standardize, and Sustain;
-
Kanban – visual signals like colored tape, stickers or other visual cues are used to keep track inventory.
-
Theory of Constraints - Identify bottlenecks in the process, and eliminate them using lean tools such kanban boards.
-
Just-in-time delivery - Deliver components and materials right to your point of use.
-
Continuous improvement - Make incremental improvements rather than overhauling the entire process.