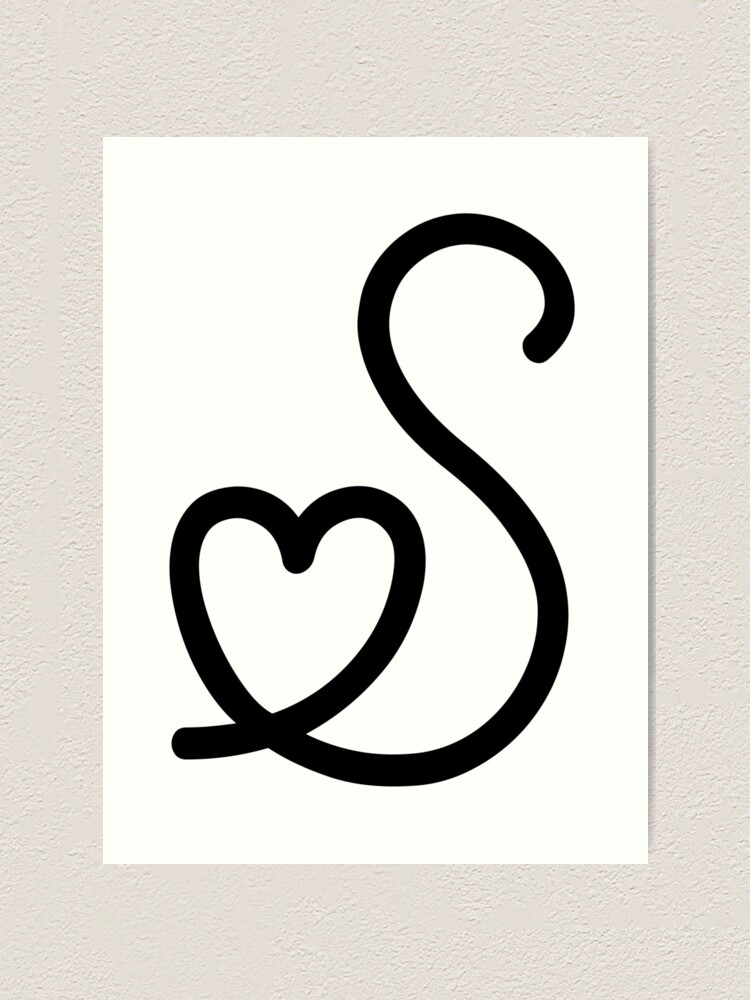
Often referred to as offshoring, outsourcing is a strategy that allows companies to cut costs while focusing on their core business. It is also an effective way for companies to increase their competitiveness. We will be covering the basics of outsourcing and some of its drawbacks.
Offshoring is one form of outsourcing
Offshoring, which involves the transfer of production and services to another country, is a common method to cut costs. The practice can be used for various purposes, such as reducing labor costs or lowering the price of product and services. However, it does not always improve efficiency.
Offshoring is the process of bringing in a team outside of your company to do a particular task. This outsourcing typically involves monotonous, repetitive and time-consuming tasks. These tasks can be outsourced in order to increase productivity, efficiency, or quality. Although most of these tasks can be done internally, there are many that cannot be completed by one employee. This makes them ideal for outsourcing.
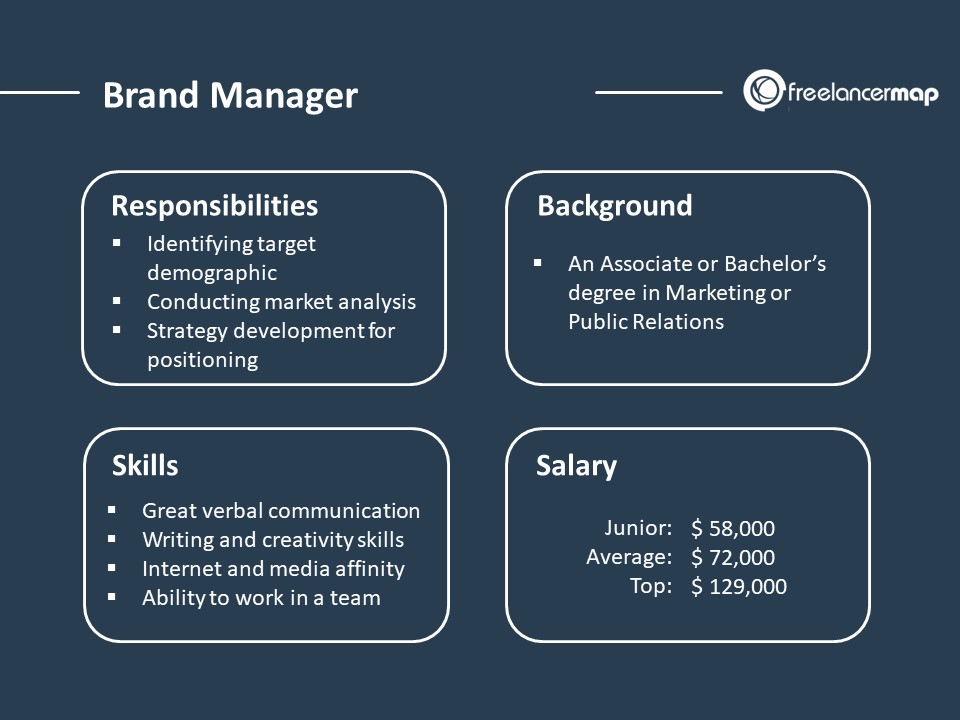
It is cost-savings.
Outsourcing services and tasks can help companies cut costs. Outsourcing can be beneficial for companies in different industries. Additionally, it can increase shareholder value. Outsourcing can help companies increase their core competencies, improve IT knowledge, and implement planned improvements within the company. However, outsourcing business operations can be complex.
Outsourcing reduces staff time spent on noncore tasks like technical support and telephone marketing. They can focus on other areas of business, like product development. This frees up their time for creative and innovative projects. They can also focus on brainstorming new ideas for products and services, helping the company grow.
It allows companies to focus on their core business
Outsourcing has become a popular option among companies looking to cut costs and increase productivity. Outsourcing is common for functions such as accounting, customer service and marketing. Companies can outsource these functions to help them focus on their core competencies and lower their payroll costs. Companies can also outsource to help them focus on their core competencies such as product development, sales, and customer service.
Outsourcing can reduce risk for businesses. The outside provider often has an experienced staff that can provide valuable advice and insights. This makes it easier for you to make the necessary changes. If call volume fluctuates, for example, an outsourcing customer service team can add agents quickly. For accounting and marketing functions, a provider can scale up or down as needed.
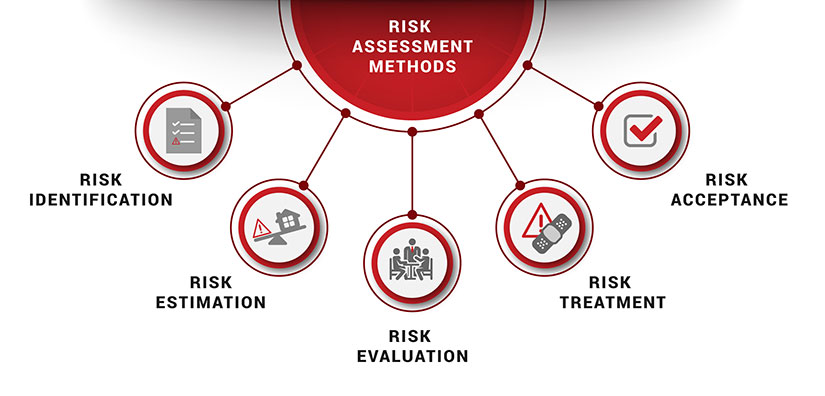
It helps them be more competitive.
Companies are beginning to see the value of outsourcing non-core functions and are building strong vendor-purchaser relationships. This type of relationship involves complete partnership between the organizations involved and regular reviews of progress and performance. This ensures that the vendor is acting in the organization's best interests while also providing a method to resolve issues. Outsourcing comes with risk. Therefore, companies need to be careful about choosing outsourcing partners.
Outsourcing allows businesses to tap into a global resource and knowledge base. Outsourcing companies spend a lot of time and money selecting the best professionals in specific fields. This allows them to stay competitive while offering their customers the best possible service at a lower price.
FAQ
What are the most common errors made by managers?
Sometimes managers make their job harder than they need to.
They may not be able to delegate enough responsibility to staff or provide adequate support.
Many managers lack the communication skills to motivate and lead their employees.
Managers set unrealistic expectations and make it difficult for their team.
Managers might try to solve every problem by themselves rather than delegating the responsibility.
How does Six Sigma work
Six Sigma uses statistical analyses to locate problems, measure them, analyze root cause, fix problems and learn from the experience.
The first step is identifying the problem.
Next, data is collected and analyzed to identify trends and patterns.
Next, corrective steps are taken to fix the problem.
Finally, the data are reanalyzed in order to determine if it has been resolved.
This continues until you solve the problem.
What is the difference of a program and project?
A program is permanent while a project can be temporary.
A project is usually defined by a clear goal and a set deadline.
This is often done by a group of people who report to one another.
A program usually has a set of goals and objectives.
It is usually implemented by a single person.
What are management concepts, you ask?
Management concepts are the fundamental principles and practices that managers use when managing people and their resources. They cover topics such as job descriptions and performance evaluations, human resource policies, training programs, employee motivation, compens systems, organizational structure, among others.
How do you define Six Sigma?
Six Sigma is well-known to those who have worked in operations research and statistics. But anyone can benefit from it.
Because it requires a high degree of commitment, only leaders with strong leadership skills can implement it successfully.
What is the role of a manager in a company?
The role of a manager varies from one industry to another.
A manager is generally responsible for overseeing the day to day operations of a company.
He/she makes sure that the company meets its financial obligations, and that it produces goods or services that customers desire.
He/she makes sure that employees adhere to the rules and regulations as well as quality standards.
He/she plans new products and services and oversees marketing campaigns.
How can a manager enhance his/her leadership skills?
By practicing good management skills at all times.
Managers must constantly monitor the performance of their subordinates.
If you notice your subordinate isn't performing up to par, you must take action quickly.
You must be able to spot what is lacking and how you can improve it.
Statistics
- The profession is expected to grow 7% by 2028, a bit faster than the national average. (wgu.edu)
- This field is expected to grow about 7% by 2028, a bit faster than the national average for job growth. (wgu.edu)
- 100% of the courses are offered online, and no campus visits are required — a big time-saver for you. (online.uc.edu)
- Your choice in Step 5 may very likely be the same or similar to the alternative you placed at the top of your list at the end of Step 4. (umassd.edu)
- UpCounsel accepts only the top 5 percent of lawyers on its site. (upcounsel.com)
External Links
How To
How can you implement the Kaizen technique?
Kaizen means continuous improvement. The Japanese philosophy emphasizes small, incremental improvements to achieve continuous improvement. This term was created by Toyota Motor Corporation in 1950. It is a process where people come together to improve their processes.
Kaizen is one the most important methods of Lean Manufacturing. The concept involves employees responsible for manufacturing identifying problems and trying to fix them before they become serious issues. This will increase the quality and decrease the cost of the products.
Kaizen is an approach to making every worker aware and alert to what is happening around them. If something is wrong, it should be corrected immediately so that no problem occurs. If someone spots a problem while at work, they should immediately report it to their manager.
Kaizen has a set of basic principles that we all follow. Start with the end product, and then move to the beginning. In order to improve our factory's production, we must first fix the machines producing the final product. Next, we fix the machines which produce components. We then fix the workers that work with those machines.
This approach is called 'kaizen' because it focuses on improving everything steps by step. Once we have finished fixing the factory, we return to the beginning and work until perfection.
You need to know how to measure the effectiveness of kaizen within your business. There are many ways you can determine if kaizen has been implemented well. Another method is to see how many defects are found on the products. Another way is to check how much productivity has grown since kaizen was implemented.
Another way to know whether kaizen is working is to ask yourself why did you decide to implement kaizen. You were trying to save money or obey the law? You really believed it would make you successful?
Let's say you answered yes or all of these questions. Congratulations! Now you're ready for kaizen.