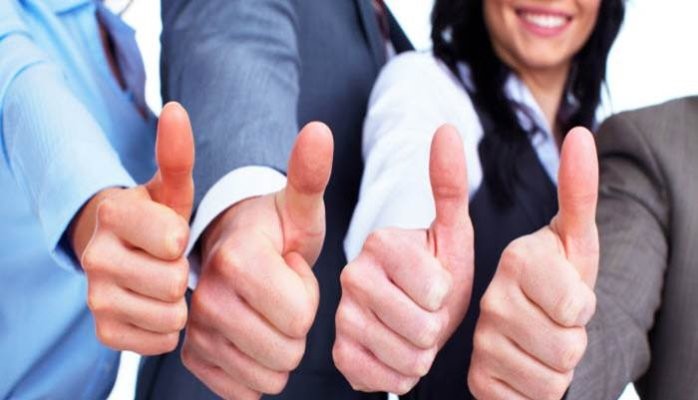
A certified building manager is a qualified professional working in construction. To prove their knowledge, certified construction managers must pass a formal examination. The exam is practical and measures the knowledge of the candidate in the field of construction. The exam duration depends on the level of qualification. Passing the examination takes on average four hours.
Earnings potential
Earning a degree as a construction manager can be a lucrative option. A four-year education is typical, but it is possible in as little as one to earn a master’s in construction administration. You will need to have one year of experience working under the supervision and guidance of a construction manager before you can start your journey towards certification.
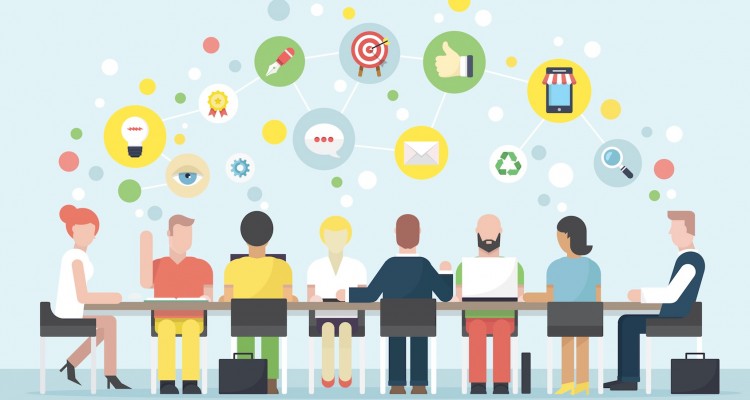
Earning a certificate for construction management can help increase your earnings potential and keep your licenses and certifications current. You can also take certification courses to stay up-to-date on safety and compliance guidelines.
Credentials required
Whether you want a career in construction management, or are just looking for a way to improve your resume, certification is the perfect way to enhance your credentials. You can get the job you want by proving your dedication and education. There are many certifications to choose from. Make sure you find the one that is right for your career.
You must pass a 600-question, six hour exam in order to earn the credential. The test is a practical assessment that tests your knowledge of safety and construction management. You can become a Certified Construction manager by passing the test. You can keep the credential for seven years once you have earned it, but you must take it again every seven years.
Duties of the job
A construction manager is someone with expertise in building construction. To complete a project, they work closely with civil engineers as well as other building specialists. They manage and negotiate construction terms. They also oversee the selection of contractors and subcontractors. They may have to interact with lawyers or officials from the local government.
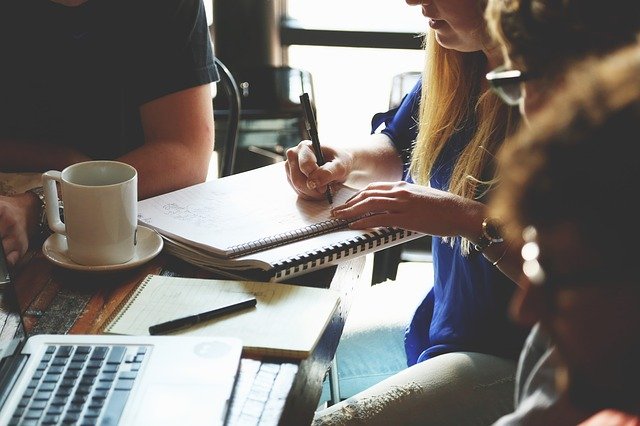
Construction managers must be able to identify and mitigate risks to ensure a successful project. Additionally, they need to be able interact with multiple groups to ensure that all aspects are handled according to highest standards. This position typically requires a bachelor's in construction management and at least five years of relevant work experience. To effectively manage multiple audiences, and to resolve issues and disputes, construction managers must be excellent communicators.
FAQ
What are the main four functions of management
Management is responsible of planning, organizing, leading, and controlling people as well as resources. Management also involves setting goals and developing policies.
Organizations can achieve their goals through management. This includes leadership, coordination, control and motivation.
The four main functions of management are:
Planning - Planning is about determining what must be done.
Organizing is the act of deciding how things should go.
Direction - This is the art of getting people to follow your instructions.
Controlling - This is the ability to control people and ensure that they do their jobs according to plan.
What are the 3 basic management styles?
These are the three most common management styles: participative (authoritarian), laissez-faire (leavez-faire), and authoritarian. Each style has its strengths and weaknesses. Which style do you prefer? Why?
Authoritarian - The leader sets the direction and expects everyone to comply with it. This style works best in large organizations that are stable and well-organized.
Laissez-faire: The leader lets each person decide for themselves. This style works best when an organization is small and dynamic.
Participative – Leaders are open to suggestions and ideas from everyone. This style works best in smaller organizations where everyone feels valued.
How do we create a company culture that is productive?
A successful company culture is one that makes people feel valued and respected.
It's founded on three principal principles:
-
Everyone has something to contribute
-
People are treated fairly
-
It is possible to have mutual respect between groups and individuals
These values are reflected in the way people behave. They will treat others with kindness and consideration.
They will listen respectfully to the opinions of others.
They encourage others to express their feelings and ideas.
The company culture promotes collaboration and open communication.
People are free to speak out without fear of reprisal.
They know that they will not be judged if they make mistakes, as long as the matter is dealt with honestly.
The company culture encourages honesty and integrity.
Everyone understands that the truth is always best.
Everyone understands that there are rules and regulations which apply to them.
Everyone does not expect to receive special treatment.
What are the steps that management takes to reach a decision?
Managers have to make complex decisions. It involves many elements, including analysis, strategy. planning. implementation. measurement. evaluation. feedback.
When managing people, the most important thing to remember is that they are just human beings like you and make mistakes. You can always improve your performance, provided you are willing to make the effort.
This video shows you how management makes decisions. We discuss the different types of decisions and why they are important, every manager should know how to navigate them. You'll learn about the following topics:
How do you manage employees effectively?
Managing employees effectively means ensuring that they are happy and productive.
It also means having clear expectations of their behavior and keeping track of their performance.
Managers must be clear about their goals and those of their teams in order to succeed.
They should communicate clearly to staff members. They must communicate clearly with staff members.
They also need to keep records of their team's activities. These include:
-
What was accomplished?
-
How much work were you able to accomplish?
-
Who did it?
-
How did it get done?
-
Why was it done?
This information can help you monitor your performance and to evaluate your results.
Statistics
- 100% of the courses are offered online, and no campus visits are required — a big time-saver for you. (online.uc.edu)
- The BLS says that financial services jobs like banking are expected to grow 4% by 2030, about as fast as the national average. (wgu.edu)
- The profession is expected to grow 7% by 2028, a bit faster than the national average. (wgu.edu)
- As of 2020, personal bankers or tellers make an average of $32,620 per year, according to the BLS. (wgu.edu)
- This field is expected to grow about 7% by 2028, a bit faster than the national average for job growth. (wgu.edu)
External Links
How To
How can Lean Manufacturing be done?
Lean Manufacturing techniques are used to reduce waste while increasing efficiency by using structured methods. These processes were created by Toyota Motor Corporation, Japan in the 1980s. The main goal was to produce products at lower costs while maintaining quality. Lean manufacturing emphasizes removing unnecessary steps from the production process. It includes five main elements: pull systems (continuous improvement), continuous improvement (just-in-time), kaizen (5S), and continuous change (continuous changes). Pull systems are able to produce exactly what the customer requires without extra work. Continuous improvement is constantly improving upon existing processes. Just-intime refers the time components and materials arrive at the exact place where they are needed. Kaizen means continuous improvement, which is achieved by implementing small changes continuously. Last but not least, 5S is for sort. These five elements are combined to give you the best possible results.
Lean Production System
Six key concepts form the foundation of the lean production system:
-
Flow is about moving material and information as near as customers can.
-
Value stream mapping - break down each stage of a process into discrete tasks and create a flowchart of the entire process;
-
Five S's, Sort, Set in Order, Shine. Standardize. and Sustain.
-
Kanban - use visual signals such as colored tape, stickers, or other visual cues to keep track of inventory;
-
Theory of constraints: Identify bottlenecks and use lean tools such as kanban boards to eliminate them.
-
Just-in-time delivery - Deliver components and materials right to your point of use.
-
Continuous improvement: Make incremental improvements to the process instead of overhauling it completely.