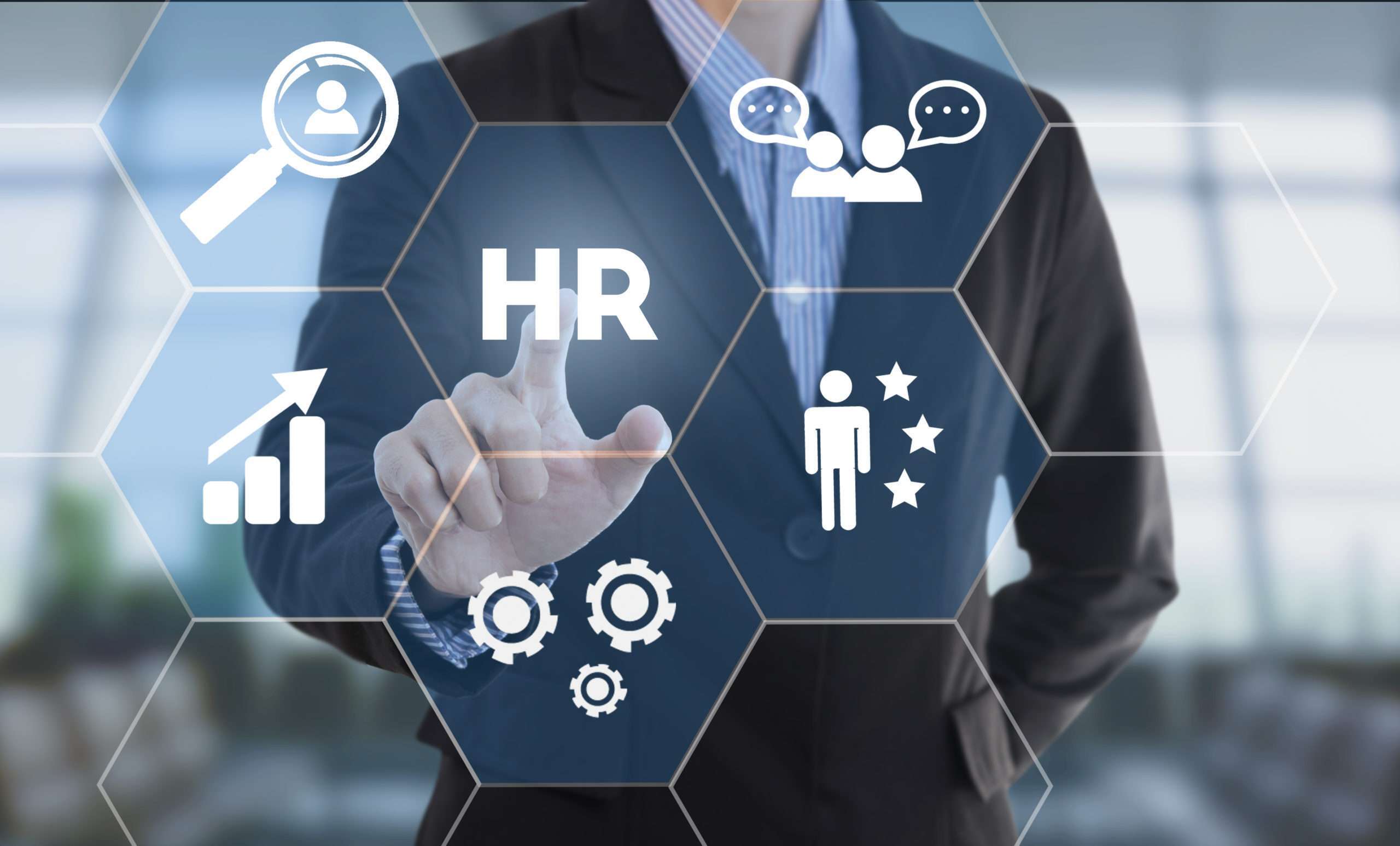
Integrated supply chain management is a holistic approach to managing a business. It involves the "cradle management" of a business. This management approach is marked by the creation of asymmetrical relationships among buyers and sellers. It aims to improve quality and decrease costs. It involves visibility from all points of the supply chain. This is an important component of fully integrated supply chains. But not all companies want to use this approach.
Integrated supply chain management can be described as a "cradle–to-grave" approach.
Integrated supply chain management is an all-encompassing concept that addresses all aspects of the product life cycle, from raw materials to consumer products. It encompasses forward and back logistics, information flows, cash flows, and information flows. It typically runs from the producers to distributors to the retailers. The ultimate goal of supply chain management is to reduce waste and maximize the benefits for the end consumer. Supply chain managers need to understand how to use outside resources and recycle materials at their end.
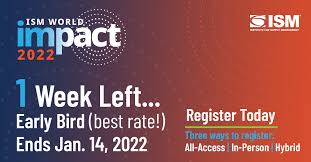
It is marked by adversarial relationships between buyers, sellers, and other participants
The integration of supply chain management requires reducing the number transactions and maximising the performance. It requires disciplined managerial skills, technologies, process, and a clear focus on key capabilities. All participants should strive for higher profitability and lower risk. This is often difficult to achieve in the current global economic climate. With some common practices, however, integration of supply chain management can be a cost-effective and efficient strategy.
It reduces costs
Integrated supply chain management can reduce costs for your business in many ways. You will first need to ensure your suppliers meet all your requirements. A good reputation is essential, as well as the ability to deliver your goods on time. This is especially important for those who deal with perishable items. Implementing better supply chain management practices will increase efficiency in your business.
It improves quality
Integrated supply chain management allows for a single view of the entire supply chain. This centralized view is easy to update without needing hardware and software. It allows for agile and scalable supply chains. By leveraging real-time intelligence, organizations can plan better, coordinate with vendors, and maximize their business' performance. All parties benefit. These are just some of the benefits you get from integrating your supply chain.
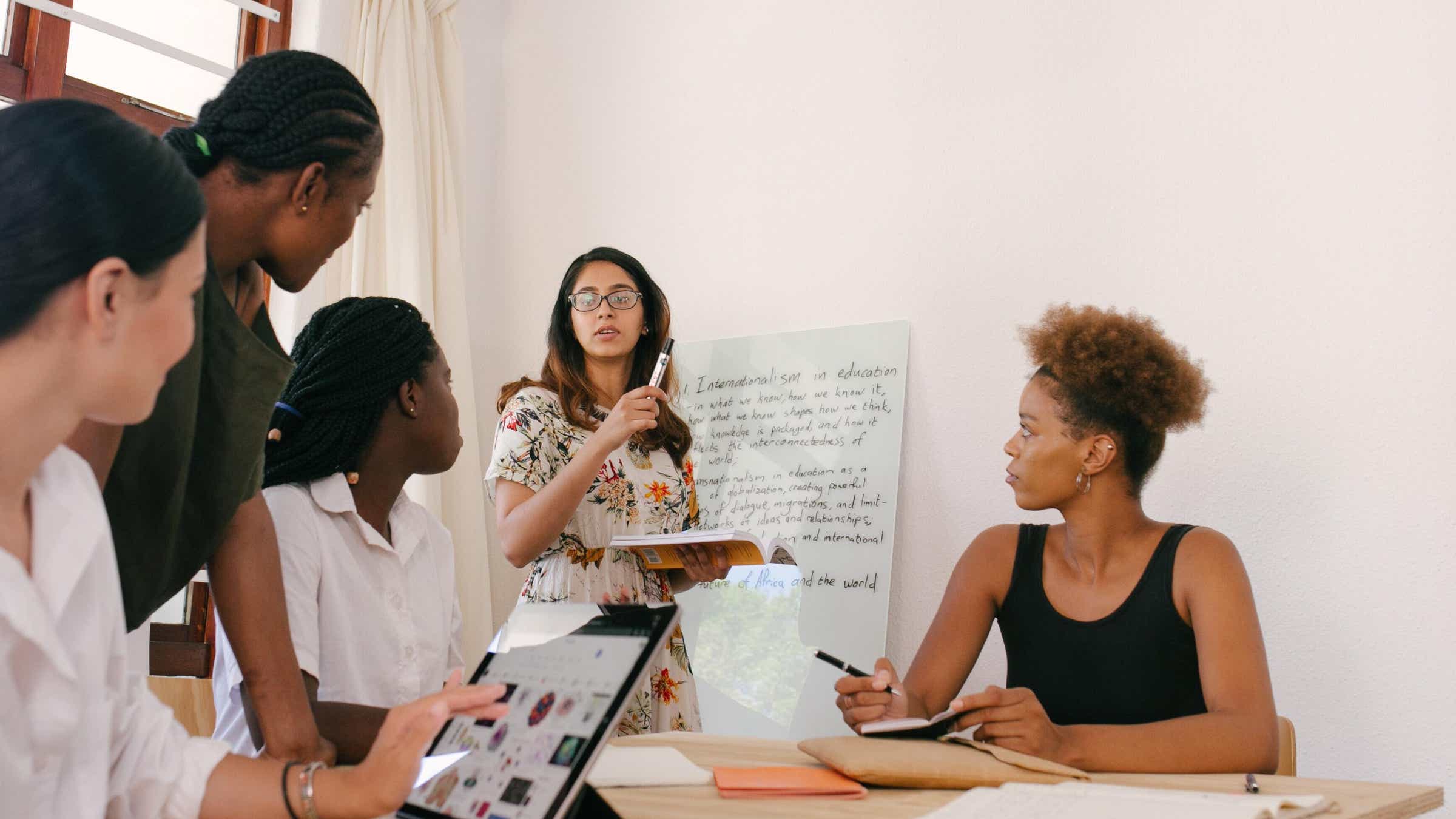
It allows rapid product design, fabrication and assembly
Manufacturers can now design and produce complete products in a fraction of the time it used to take before integrated supply chain management was invented. This trend can reduce material waste as well as warehouse costs. On-demand production also offers better customer service. The only downside is the steep learning curve. But, it is possible to create products in as little as one day using new materials and hardware. It can also enhance the product's quality.
FAQ
What is Kaizen?
Kaizen is a Japanese term which means "continuous improvement." This philosophy encourages employees to continually look for ways to improve the work environment.
Kaizen is based on the belief that every person should be able to do his or her job well.
Why is it important for companies to use project management techniques?
Project management techniques ensure that projects run smoothly while meeting deadlines.
This is because most businesses rely on project work for their products and services.
These projects require companies to be efficient and effective managers.
Companies can lose time, money, and reputation if they don't have a good project management system.
What is the difference of leadership and management?
Leadership is about influencing others. Management is about controlling others.
Leaders inspire followers, while managers direct workers.
A leader motivates people and keeps them on task.
A leader develops people; a manager manages people.
What does Six Sigma mean?
Six Sigma uses statistics to measure problems, find root causes, fix them, and learn from past mistakes.
The first step in solving a problem is to identify it.
The next step is to collect data and analyze it in order to identify trends or patterns.
Then corrective actions are taken to solve the problem.
The data are then reanalyzed to see if the problem is solved.
This continues until the problem has been solved.
How to effectively manage employees
Effectively managing employees requires that you ensure their happiness and productivity.
This also involves setting clear expectations and monitoring their performance.
Managers need clear goals to be able to accomplish this.
They need to communicate clearly and openly with staff members. They also need to make sure that they discipline and reward the best performers.
They will also need to keep records about their team's activities. These include:
-
What did you accomplish?
-
How much work was put in?
-
Who did it?
-
How did it get done?
-
Why?
This information can be used for monitoring performance and evaluating results.
Statistics
- Our program is 100% engineered for your success. (online.uc.edu)
- UpCounsel accepts only the top 5 percent of lawyers on its site. (upcounsel.com)
- The profession is expected to grow 7% by 2028, a bit faster than the national average. (wgu.edu)
- As of 2020, personal bankers or tellers make an average of $32,620 per year, according to the BLS. (wgu.edu)
- The BLS says that financial services jobs like banking are expected to grow 4% by 2030, about as fast as the national average. (wgu.edu)
External Links
How To
How do you get your Six Sigma license?
Six Sigma can be used to improve quality and efficiency. It is a process that helps businesses achieve consistent results in their operations. The name "Sigmas" comes from the Greek words "sigmas", meaning "six". Motorola created this process in 1986. Motorola realized that standardizing manufacturing processes was necessary to make products more efficient and less expensive. Because of the number of people involved in the work, they had problems maintaining consistency. They used statistical tools such as Pareto analysis, control charts, and Pareto analysis to resolve the problem. They would then apply these techniques to all aspects of their operation. This would allow them to make any necessary changes. The Six Sigma certification process involves three major steps. Finding out if the certification is available for you is the first step. You'll want to take some classes and pass them before you start taking any tests. After passing the classes, you will be able to take the tests. It is important to review everything that you have learned in class. Then, you'll be ready to take the test. You will be certified if you pass the test. Finally, you can add your certifications on to your resume.