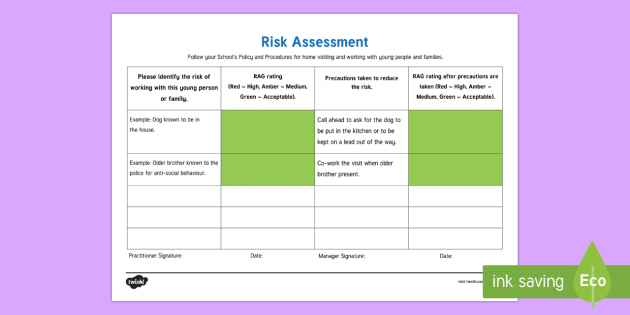
Management of supply chain risks involves many types of risk. These risks could be related either to the demand for a product or to the supply of raw material. Demand risks arise from underestimating the demand for a product. Supply risks are caused by delays in receiving raw materials. These risks can cause disruptions in product flow. In the supply chain, there can be environmental risks due to social, political, or environmental issues.
Cybersecurity is a critical component of supply chain risk and management
Cybersecurity measures can be taken to safeguard critical assets. Supply chain risk management also includes cybersecurity measures. These measures may include developing a cybersecurity policy and establishing controls for suppliers. In addition, businesses should create contracts stating their security requirements. These contracts should outline what they are expected to do to protect your assets. If a supplier fails to meet these standards, the company should consider escrow services to ensure that sensitive information is not misused.
Cyber threats become more complex in the supply chain. They must be assessed and managed carefully. Cyber threats can occur at any stage of the chain, and their impact can be devastating to a company's financial, brand, and operational health. Companies must address cybersecurity concerns at each stage of the supply-chain.
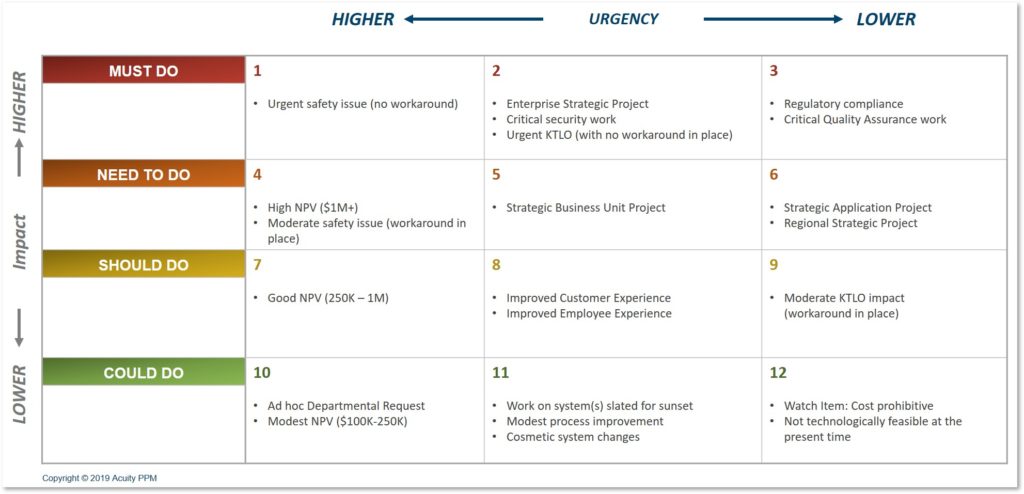
It requires a crossfunctional team
Supply chain risk management requires a cross-functional team in order to manage the risks that are associated with the entire supply chains. This strategy must include preparation, response, recovery. Preparation is about identifying high-risk areas, and developing contingency plans to deal with them. The plan should prioritize risks according to likelihood and severity. Visibility is another important aspect of a supply chain management strategy.
Despite the importance of supply chain risk management, it has been slow to be tackled by executives. Sixty-eight percent of 639 executives surveyed said their companies were more likely to suffer from supply chain disruptions today than they were two year ago. And 72 percent predicted that these risks would continue to grow. Although several government agencies have been established to address supply chain risks, the private sector continues to search for a proven approach that will minimize business disruption.
Supply chain boards that are effective review the major risks in the supply chain to identify mitigation steps. Each participant can take ownership of the mitigation steps during the review. A procurement representative, for example, is responsible to define the qualification of a new supplier and onboard them.
Technology is required
Organizations are looking to cut costs and increase resilience by rethinking how they manage supply chain risks. They are turning to technology to help them gain better visibility and manage risks before they arise. Companies can create stronger global networks and resilient supply chains with the right technology. However, to fully leverage the benefits of technology, companies need accurate data and visibility platforms. Without these, they will be forced to handle supply chain risk management on a reactive basis.
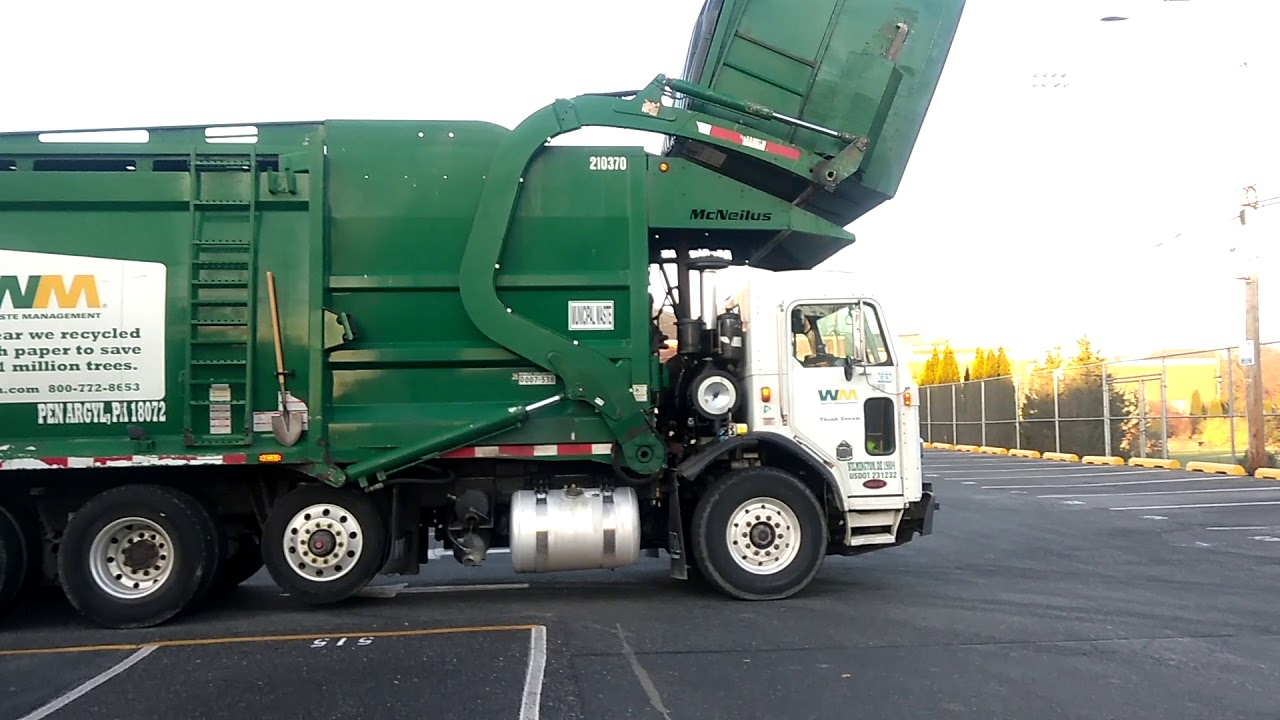
Management of supply chain risk is complex and multifaceted. A recent survey of 639 industry leaders found that 71% thought their supply chain was more vulnerable than it used to be and that the risk would increase. In response, the United States government has launched a series of agencies to address supply chain risk, including the Protecting Critical Technology Task Force at the Department of Defense. Private companies are now looking for proven strategies that can help minimize the impact of supply chains risks on their business.
FAQ
What are management concepts?
Management Concepts are the principles and practices managers use to manage people and resources. They cover topics such as job descriptions and performance evaluations, human resource policies, training programs, employee motivation, compens systems, organizational structure, among others.
What is TQM, exactly?
The industrial revolution led to the birth and growth of the quality movement. Manufacturing companies realized they couldn't compete solely on price. They needed to improve the quality and efficiency of their products if they were to be competitive.
To address this need for improvement management created Total Quality Management (TQM) which aimed to improve all aspects of an organization's performance. It included continuous improvement, employee involvement and customer satisfaction.
What kind of people use Six Sigma
People who have worked with statistics and operations research will usually be familiar with the concepts behind six sigma. Anybody involved in any aspect or business can benefit.
It requires high levels of commitment and leadership skills to be successful.
How do you manage employees effectively?
Effectively managing employees requires that you ensure their happiness and productivity.
It means setting clear expectations for them and keeping an eye on their performance.
Managers need clear goals to be able to accomplish this.
They should communicate clearly with employees. They need to communicate clearly with their staff.
They must also keep records of team activities. These include:
-
What was achieved?
-
What was the work involved?
-
Who did it, anyway?
-
What was the moment it was completed?
-
Why?
This information can be used to monitor performance and evaluate results.
Statistics
- The average salary for financial advisors in 2021 is around $60,000 per year, with the top 10% of the profession making more than $111,000 per year. (wgu.edu)
- UpCounsel accepts only the top 5 percent of lawyers on its site. (upcounsel.com)
- This field is expected to grow about 7% by 2028, a bit faster than the national average for job growth. (wgu.edu)
- As of 2020, personal bankers or tellers make an average of $32,620 per year, according to the BLS. (wgu.edu)
- Hire the top business lawyers and save up to 60% on legal fees (upcounsel.com)
External Links
How To
How do I get my Six Sigma certification?
Six Sigma is an effective quality management tool that can improve processes and increase productivity. It is a process that helps businesses achieve consistent results in their operations. The name comes from the first two letters of the Greek word "sigmas" which mean "six." Motorola created this process in 1986. Motorola realized that standardizing manufacturing processes was necessary to make products more efficient and less expensive. Because of the number of people involved in the work, they had problems maintaining consistency. They decided to use statistical tools like control charts and Pareto analysis to solve the problem. Then, they would apply these techniques in every area of the operation. They would then be able make improvements where needed. There are three main steps to follow when trying to get your Six Sigma certification. The first step is to find out if you're qualified. Before you can take any tests, you will need to take some classes. Once you've passed those classes, you'll start taking the tests. You'll want to study everything you learned during the class beforehand. You'll then be prepared to take the exam. If you pass, you'll get certified. Finally, your certifications will be added to your resume.