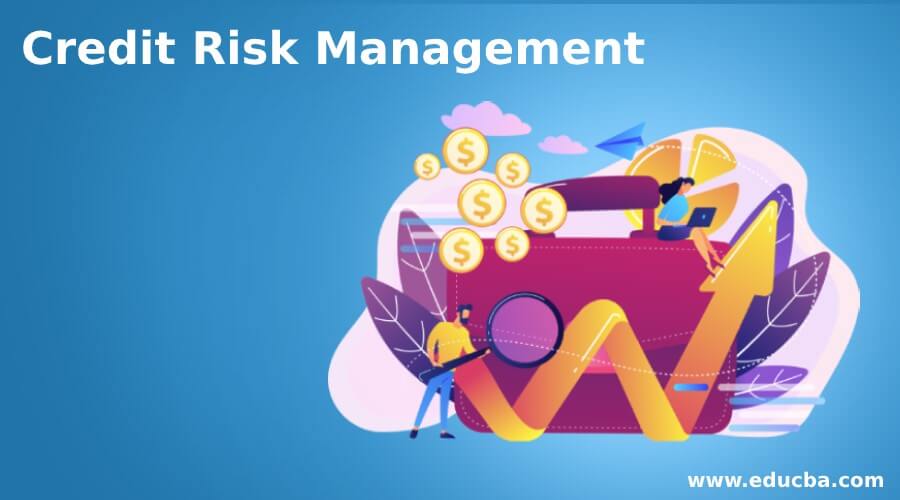
After action reviews can help you make sure your team is aware of how they are performing. These reviews can be used to learn from past projects. We'll be discussing the benefits of these meetings, how they can be conducted, and how stakeholders can get involved. Here are four key steps for conducting an effective review.
Leçons learned from previous projects
After action reviews allow teams to look back at their projects and identify what needs to be changed. It is important to ask why the results were not as expected. and explore the reasons behind the differences. Often the answer is internal and can easily be controlled by team members. Sometimes, however, there may be a reason external to the project that led to a different outcome. The team should not try to impose blame but rather openly discuss the reasons.
After-action reports can be useful in identifying best practices, identifying gaps, and learning from them. They can also help to assess national response capacities. These reports should list the steps necessary to improve the response to a potential disaster. This approach is essential in a culture of continuous improvement.
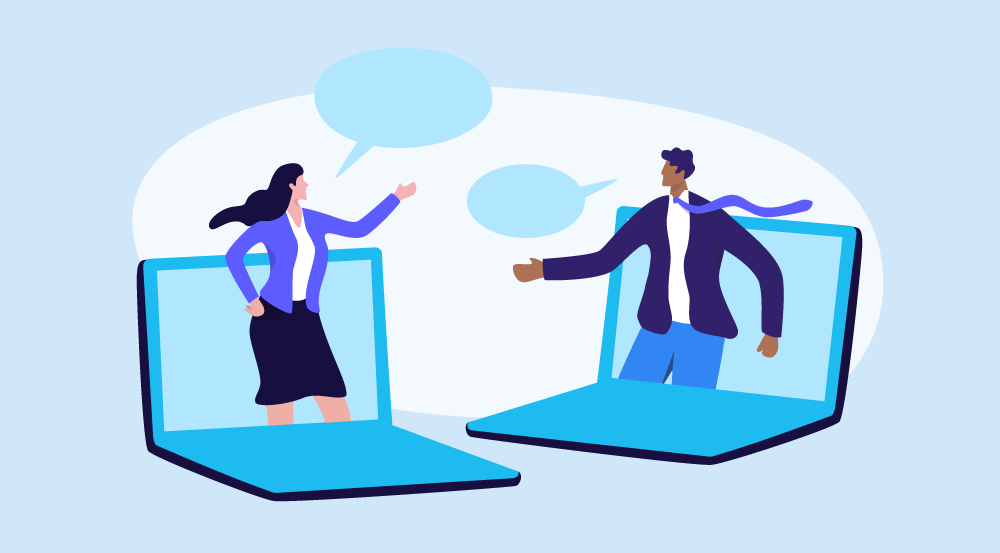
Benefits to team members
After action reviews foster a culture of continuous learning for team members and improve feedback. They are a great way to encourage critical thinking, and to discuss the merits as well as the demerits of every project. These reviews can be a great way to create best practices for future project development if they are done properly. This type review can be beneficial for team members and organizations as long as it is performed in a structured manner and is consistent. After-action reviews are a great way to improve feedback and can identify areas that need improvement.
After-action reviews can be held almost anywhere. You don't have to plan ahead and you can make them as long or short as you need. They can also be used to increase trust and combat negative attitudes within the team. In addition, they can help overcome blame culture and the fear of making mistakes. Moreover, they are extremely beneficial for teams, especially at key stages of a project, since they can use the lessons they learn to improve their work right away. But, they're only as effective as skilled facilitation and done correctly.
Ways to conduct them
After action reviews can be useful in a number of ways. You can get feedback about how your project is going and also discuss what went wrong and how to improve. This type of review should occur at the conclusion of a project, or at the start of a new one.
After-action reviews can be performed on a single project, or on an individual element of a particular project. After the project is complete, however, it might be more beneficial to conduct an after-action review. Some people may want to evaluate a project or activity just completed, while others prefer to wait to do so. Others may worry that an after-action review could take away from the work on a project.
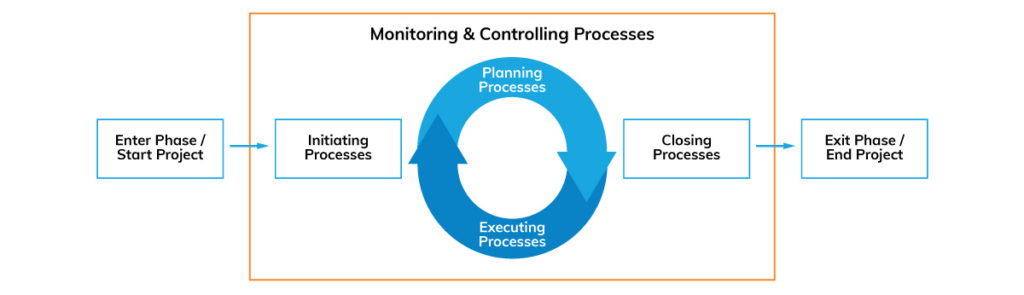
Stakeholders are involved
After Action Reviews are a great way to collect the lessons learned during a project. After-action Reviews are an effective way to share the lessons learned with others. They can also be used to identify areas for improvement and foster continuous learning.
Customers, project executives, and team members can all participate in after-action reviews. The preparation phase of the AAR involves gathering materials and discussing them with team members. The final report should provide an explanation of what happened and what needs to be improved.
FAQ
What are the 3 basic management styles?
There are three main management styles: participative, laissez-faire and authoritarian. Each style has its strengths and weaknesses. What style do you prefer? Why?
Autoritarian - The leader sets direction and expects everyone else to follow it. This style works well if an organization is large and stable.
Laissez-faire: The leader lets each person decide for themselves. This style is most effective when the organization's size and dynamics are small.
Participative - Leaders listen to all ideas and suggestions. This style is best for small organizations where everyone feels valued.
What is TQM?
The quality movement was born during the industrial revolution when manufacturing companies realized they could not compete on price alone. They had to improve efficiency and quality if they were to remain competitive.
Management realized the need to improve and created Total Quality Management, which focused on improving all aspects within an organization's performance. It included continual improvement processes, employee involvement, customer satisfaction, and customer satisfaction.
How can a manager enhance his/her leadership skills?
It is important to have good management skills.
Managers need to monitor their subordinates' performance.
If you notice your subordinate isn't performing up to par, you must take action quickly.
It is important to be able identify areas that need improvement and what can be done to improve them.
Six Sigma is so beloved.
Six Sigma is easy to use and can lead to significant improvements. Six Sigma provides a framework to measure improvements and allows companies to focus on the most important things.
What is Six Sigma and how can it help you?
This is a method of quality improvement that emphasizes customer service, continuous learning, and customer service. It is a method that eliminates defects using statistical techniques.
Six Sigma was developed at Motorola in 1986 as part of its efforts to improve manufacturing processes.
The idea spread quickly in the industry. Today many organizations use six-sigma techniques to improve product design.
Statistics
- As of 2020, personal bankers or tellers make an average of $32,620 per year, according to the BLS. (wgu.edu)
- The BLS says that financial services jobs like banking are expected to grow 4% by 2030, about as fast as the national average. (wgu.edu)
- UpCounsel accepts only the top 5 percent of lawyers on its site. (upcounsel.com)
- The profession is expected to grow 7% by 2028, a bit faster than the national average. (wgu.edu)
- This field is expected to grow about 7% by 2028, a bit faster than the national average for job growth. (wgu.edu)
External Links
How To
What is Lean Manufacturing?
Lean Manufacturing is a method to reduce waste and increase efficiency using structured methods. They were created in Japan by Toyota Motor Corporation during the 1980s. The main goal was to produce products at lower costs while maintaining quality. Lean manufacturing is about eliminating redundant steps and activities from the manufacturing process. It consists of five basic elements: pull systems, continuous improvement, just-in-time, kaizen (continuous change), and 5S. Pull systems allow customers to get exactly what they want without having to do extra work. Continuous improvement is the continuous improvement of existing processes. Just-in–time refers when components or materials are delivered immediately to their intended destination. Kaizen stands for continuous improvement. Kaizen can be described as a process of making small improvements continuously. Last but not least, 5S is for sort. To achieve the best results, these five elements must be used together.
The Lean Production System
Six key concepts form the foundation of the lean production system:
-
Flow - focuses on moving information and materials as close to customers as possible.
-
Value stream mapping is the ability to divide a process into smaller tasks, and then create a flowchart that shows the entire process.
-
Five S's, Sort, Set in Order, Shine. Standardize. and Sustain.
-
Kanban - visual cues such as stickers or colored tape can be used to track inventory.
-
Theory of constraints: identify bottlenecks in your process and eliminate them using lean tools, such as kanban board.
-
Just-in-time delivery - Deliver components and materials right to your point of use.
-
Continuous improvement - make incremental improvements to the process rather than overhauling it all at once.