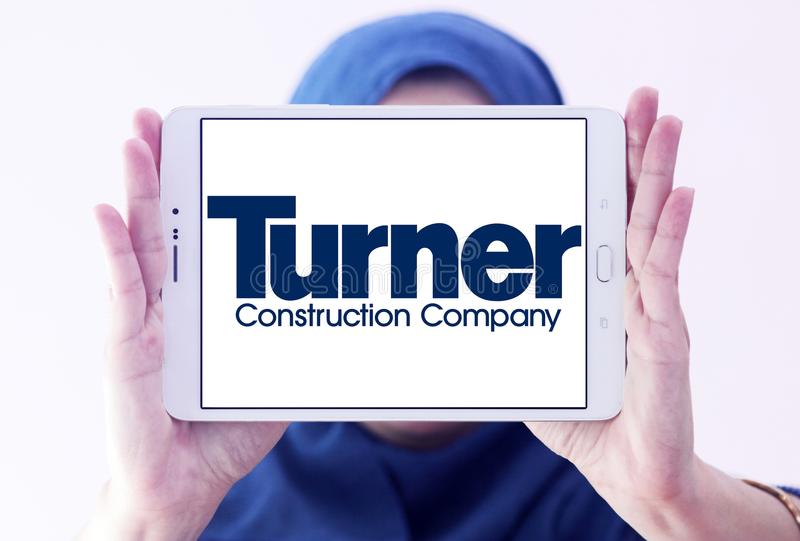
Software that manages supply chain processes is called supply chain management software. It is an enterprise resource planning (ERP software). This software helps companies manage their supply chain transactions and control the business processes. It can also be used to manage supplier relationships and control the associated business processes. There are many different types of supply-chain management software. These are just a few examples.
Software for managing open source supply chains
It is vital to manage the supply chain in a business. Management of suppliers and sales can be difficult. This is why you need to pay extra attention to ensure everything runs smoothly. Negligence can lead to lower sales or even closure of your business. To solve this problem, software engineers have developed solutions that will automate and simplify business processes. They are accessible on GitHub. These software solutions will streamline the supply chain for your business.
Supply chain management software can help you manage all aspects of your supply chain. This software will allow you to manage all activities including the procurement of goods, services, coordination of orders and execution of those orders. This software will also give you insight on any risks in your business, and will suggest strategies to avoid or minimize them. There are many open-source software solutions for supply chain management available on the market today. These include E2open SAP SCM and Logility, Perfect Commerce, Oracle SCM and Perfect Commerce. If you decide to use one of these software systems, you will be amazed at the business benefits it offers.
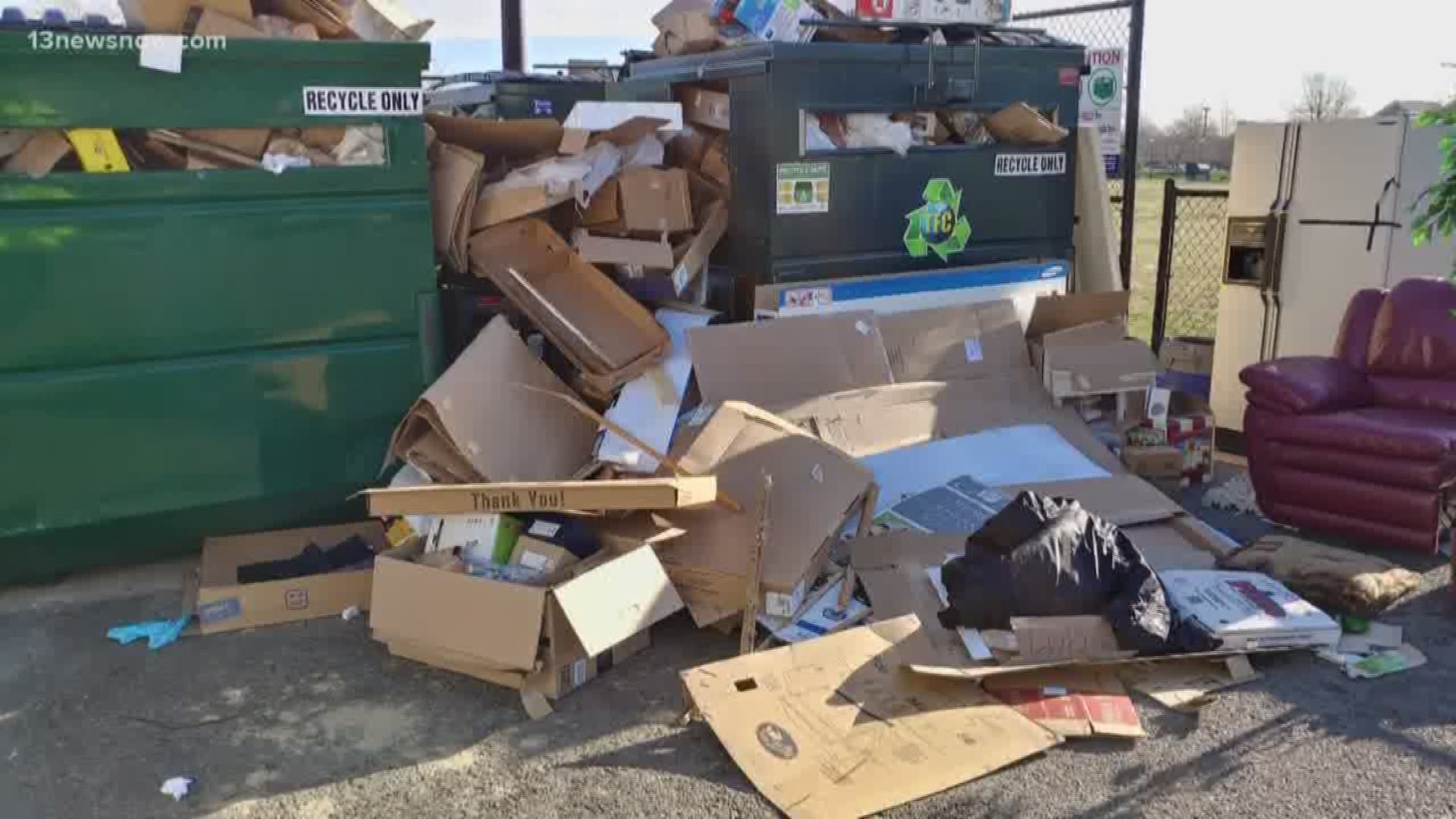
Enterprise resource planning
ERP software is a suite of integrated business applications designed to streamline the critical operations of a company. It improves data flow and collaboration among stakeholders across different departments, and makes decisions easier for everyone involved. Because of its flexibility tools and customizable features, it allows businesses to grow and become better at their jobs. It's ideal for businesses who manage multiple suppliers and distribute products in different locations. It is simple to use and implement, which will ensure that your business runs smoothly.
ERP software is an ideal solution for companies who need to manage their supply chain in a comprehensive and accurate manner. It makes information and data available to all department heads for team members. It invests heavily in visualization and analysis tools, which allow team members to create reports and notify their colleagues of wins and losses. ERP software provides a single source of truth that is accurate for all company operations. Read on to learn more about ERP software.
ShipBob
ShipBob is an innovative supply chain management software which combines proprietary technology and order fulfillment services with ecommerce inventory control. It allows merchants the ability to quickly and affordably ship products and manage inventory across multiple stores. ShipBob has warehouses throughout the continental US, making it a good choice for merchants looking to deliver products quickly. ShipBob's software helps merchants find the perfect warehouse location for their orders.
It is easy to use, and includes a dashboard that allows users to track shipments. The software offers multiple shipping options, including international and domestic shipping. You can also use the tools to manage orders and ship returns. ShipBob also supports EDI compliance with major retailers. It offers seamless integrations with major e-commerce platforms and online marketplaces as well as analytics. ShipBob, despite its many benefits, is not an ideal choice for international shipment.
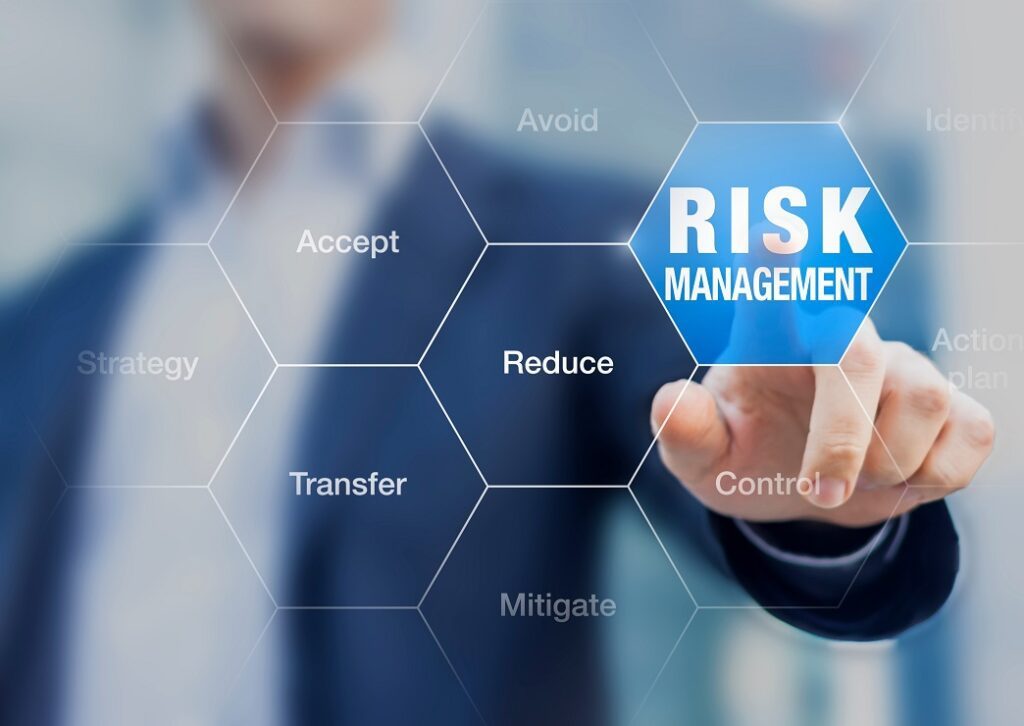
For
Infor is a top provider of enterprise software. They supply supply chain management software (SCM), for more than 70,000 companies in 194 different countries. Infor offers deep industry-specific apps, suites optimized for speed, and flexible deployment options. The company's services cover all phases of the business cycle, from product design to inventory management. Customers can rely on the company to provide them with the information they need to make informed business decisions and keep their business agile.
Infor's SCM software allows for real-time orchestration and collaboration with suppliers. It also offers transportation management. It can also help organizations optimize their delivery performance. This makes it a great choice especially for medium-sized, product-centric companies. Infor SCM has been designed for cloud computing and combines industry-specific functionality, advanced artificial intelligence, and makes it more profitable. Its cloud-based architecture enhances security and reliability. Infor's SCM Suite combines the power and intelligence of analytics with Infor Coleman AI intelligence to create a smarter supply chain.
FAQ
What kind people use Six Sigma?
Six Sigma is well-known to those who have worked in operations research and statistics. Anybody involved in any aspect or business can benefit.
It is a commitment-intensive task that requires strong leadership skills.
How does a manager learn to manage?
It is important to have good management skills.
Managers must monitor the performance of subordinates constantly.
You must quickly take action if your subordinate fails to perform.
You must be able to spot what is lacking and how you can improve it.
How does a manager motivate their employees?
Motivation is the desire for success.
It is possible to be motivated by doing something you enjoy.
You can also be motivated by the idea of making a difference to the success and growth of your organization.
If you are a doctor and want to be one, it will likely be more rewarding to see patients than to read medical books every day.
The inner motivation is another type.
You may feel strongly that you are responsible to help others.
Or you might enjoy working hard.
Ask yourself why you feel so motivated.
Then think about how you can make your life more motivating.
How does Six Sigma function?
Six Sigma uses statistical analyses to locate problems, measure them, analyze root cause, fix problems and learn from the experience.
The first step to solving the problem is to identify it.
The data is then analyzed and collected to identify trends.
Next, corrective steps are taken to fix the problem.
Finally, the data are reanalyzed in order to determine if it has been resolved.
This continues until you solve the problem.
What is the difference between a project and a program?
A program is permanent while a project can be temporary.
Projects usually have a goal and a deadline.
It is often performed by a team of people, who report back on someone else.
A program usually has a set of goals and objectives.
It is usually implemented by a single person.
What's the difference between Six Sigma and TQM?
The key difference between the two quality management tools is that while six-sigma focuses its efforts on eliminating defects, total quality management (TQM), focuses more on improving processes and reducing cost.
Six Sigma stands for continuous improvement. This approach emphasizes eliminating defects through statistical methods like control charts, Pareto analysis, and p-charts.
This method has the goal to reduce variation of product output. This is accomplished by identifying the root cause of problems and fixing them.
Total Quality Management involves monitoring and measuring every aspect of the organization. It also involves training employees to improve performance.
It is often used to increase productivity.
What are the main styles of management?
There are three main management styles: participative, laissez-faire and authoritarian. Each style has its strengths and weaknesses. Which style do your prefer? Why?
Authoritarian - The leader sets the direction and expects everyone to comply with it. This style is best when the organization has a large and stable workforce.
Laissez-faire: The leader lets each person decide for themselves. This style works best when the organization is small and dynamic.
Participative – The leader listens and takes in ideas from all. This approach works best in small organizations where everyone feels valued.
Statistics
- Our program is 100% engineered for your success. (online.uc.edu)
- Hire the top business lawyers and save up to 60% on legal fees (upcounsel.com)
- The profession is expected to grow 7% by 2028, a bit faster than the national average. (wgu.edu)
- The BLS says that financial services jobs like banking are expected to grow 4% by 2030, about as fast as the national average. (wgu.edu)
- UpCounsel accepts only the top 5 percent of lawyers on its site. (upcounsel.com)
External Links
How To
How do you do the Kaizen method?
Kaizen means continuous improvement. This term was first used by Toyota Motor Corporation in the 1950s. It refers to the Japanese philosophy that emphasizes continuous improvement through small incremental changes. It's a team effort to continuously improve processes.
Kaizen is one of the most effective methods used in Lean Manufacturing. Employees responsible for the production line should identify potential problems in the manufacturing process and work together to resolve them. This improves the quality of products, while reducing the cost.
Kaizen is an approach to making every worker aware and alert to what is happening around them. It is important to correct any problems immediately if they are discovered. So, if someone notices a problem while working, he/she should report it to his/her manager.
Kaizen has a set of basic principles that we all follow. The end product is always our starting point and we work toward the beginning. For example, if we want to improve our factory, we first fix the machines that produce the final product. Next, we fix the machines which produce components. We then fix the workers that work with those machines.
This method, called 'kaizen', focuses on improving each and every step of the process. Once we have finished fixing the factory, we return to the beginning and work until perfection.
Before you can implement kaizen into your business, it is necessary to learn how to measure its effectiveness. There are several ways to determine whether kaizen is working well. One method is to inspect the finished products for defects. Another way is to check how much productivity has grown since kaizen was implemented.
A good way to determine whether kaizen has been implemented is to ask why. It was because of the law, or simply because you wanted to save some money. Did you really think that it would help you achieve success?
Let's say you answered yes or all of these questions. Congratulations! Now you're ready for kaizen.